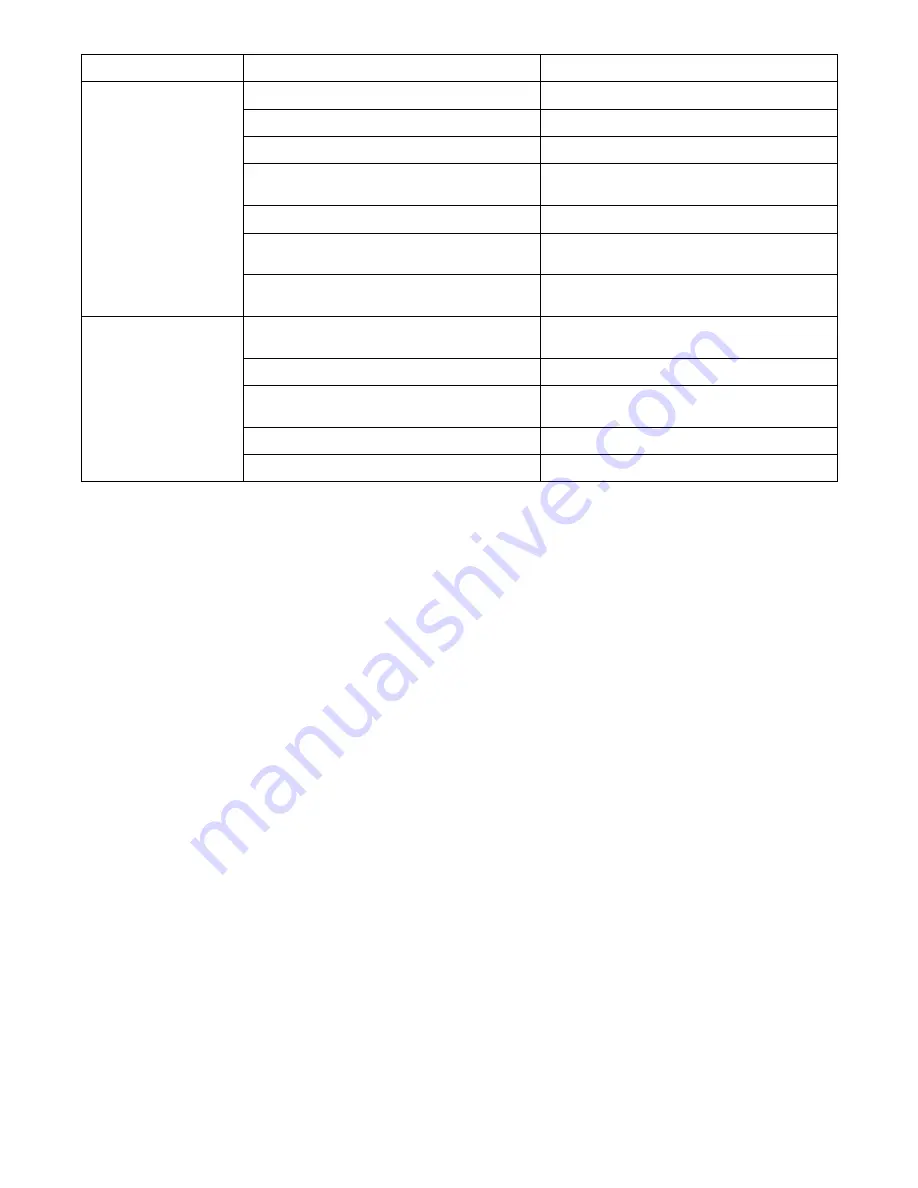
OM-260 274 Page 39
Problem
Remedy
Probable Cause
Wire feeds, but no gas flows. Gas cylinder empty.
Replace empty gas cylinder.
Gas nozzle plugged.
Clean or replace gas nozzle.
Gas cylinder valve not open or flowmeter not adjusted. Open gas valve at cylinder and adjust flow rate.
Restriction in gas line.
Check gas hose between flowmeter and wire feeder, and
gas hose in gun and cable assembly.
Loose or broken wires to gas solenoid.
Have Factory Authorized Service Agent repair wiring.
Gas solenoid valve not operating.
Have Factory Authorized Service Agent replace gas
solenoid valve.
Incorrect primary voltage connected to welding power
source.
Check primary voltage and relink welding power source
for correct voltage.
Welding arc not stable.
Wire slipping in drive rolls.
Adjust pressure setting on wire feed rolls. Replace worn
drive rolls if necessary.
Wrong size gun liner or contact tip.
Match liner and contact tip to wire size and type.
Incorrect voltage setting for selected wire feed speed on
welding power source.
Readjust welding parameters.
Loose connections at the gun weld cable or work cable. Check and tighten all connections.
Gun in poor shape or loose connection inside gun.
Repair or replace gun as necessary.