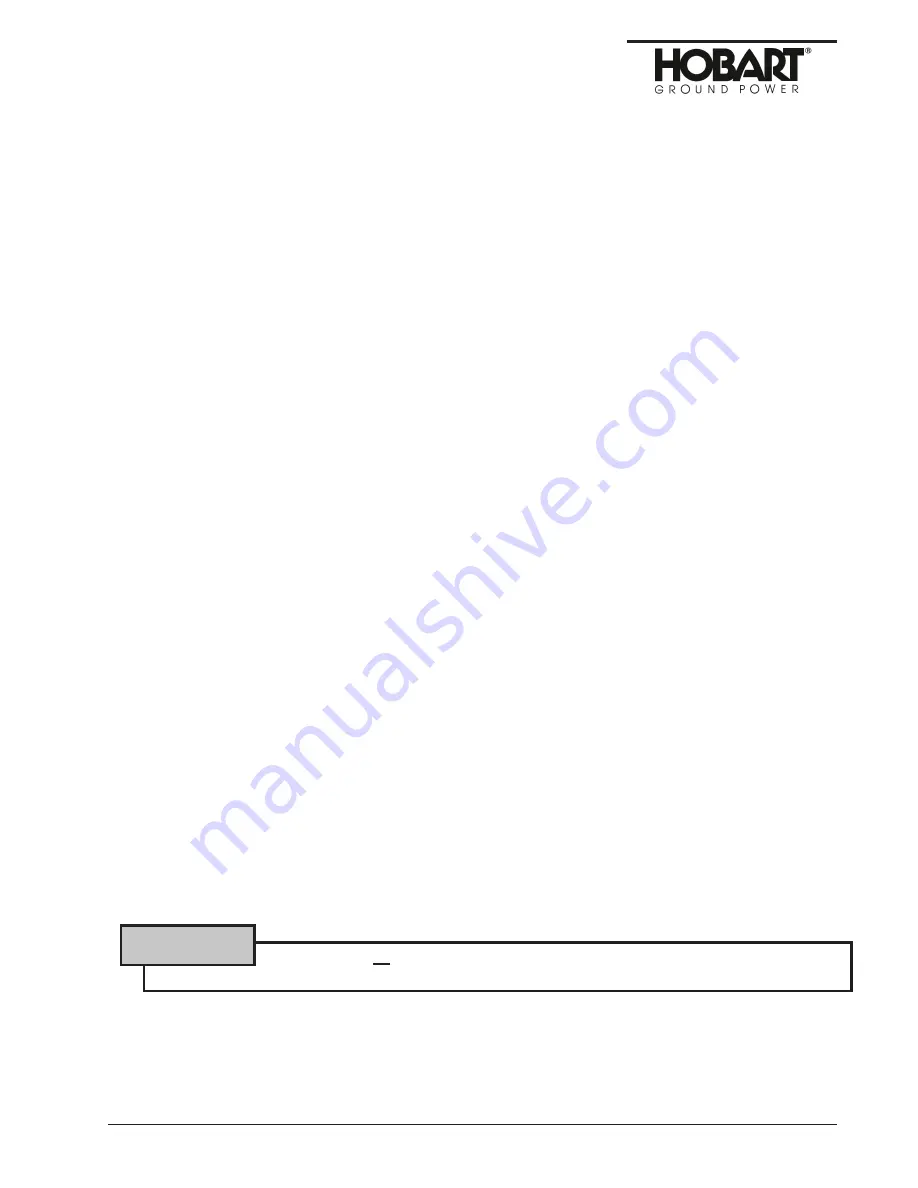
(1)
Actuator linkage adjustment
The proper adjustment of the mechanical linkage between the electric actuator and engine
speed control lever is important to the satisfactory operation of the complete system.
Exact adjustment instructions such as effective length of rod assembly
(6, Fig. 5)
, or which hole
in actuator lever to attach ball joint
(4)
cannot be determined because of slight variations in
brackets, mountings, and engine performance characteristics. However, definite rules must be
followed in making the adjustment:
1. First, adjust linkage to use the FULL TRAVEL of actuator output shaft
(2)
.
2. Second, make certain that linkage is adjusted such that it can move speed control lever
(8)
from FULL IDLE to FULL SPEED position, or VERY CLOSE to FULL SPEED position
to allow engine to pull 125% load.
Check and adjust linkage as follows, with engine stopped.
a. Before making adjustment, observe and note which hole in actuator lever (3) is used to
mount ball joint (4). It does not necessarily have to be the same hole as shown in illustration
(Fig. 5), however, rod connection to fuel control lever (8) is always in the upper hole (the hole
nearest the fuel pump).
b. Be sure levers (3 and 8) have not slipped on shafts. In
IDLE
position actuator lever (3)
should point forward and upward at an angle of 15 to 20 degrees. Speed control lever (8)
should point forward in a near horizontal position. If a lever has slipped, position correctly
and tighten securely.
c. Place both levers (3 and 8) in FULL IDLE position and attempt to connect ball joint (4) at hole
in lever (3) from which it was removed in step (a). If connection cannot be made, loosen
nuts, (5) and adjust effective length of rod so that connection may be made.
d. Manually operate actuator lever back and forth between FULL IDLE and FULL SPEED
positions. Speed control lever (8) should be moved freely through its full range between
FULL IDLE AND FULL SPEED. If adjustment is unsatisfactory, try another hole mounting in
ACTUATOR lever and readjust rod length.
e. Tighten all parts securely when adjustment is completed.
(2)
Magnetic pickup adjustment
The strength of the magnetic pickup signal to the control box can be weakened if the tip of the
pickup is too far from the flywheel ring gear. If the pickup is to be removed for any reason, or if
the signal is weak, as indicated by test
[see Para. 4, E, (4), (b)].
a. Disconnect “pull-apart” connector (1, Fig. 6).
b. Loosen nut (3) and remove magnetic pick-up (2).
c. Inspect to make certain the tip is not damaged from contact with the ring gear teeth (replace
pickup if damaged).
d. Rotate the engine as required to locate a ring gear tooth directly below the tapped, pickup
mounting hole. An imaginary line should pass through the center of the mounting hole, the
center of a flywheel tooth and the center of the flywheel.
e. Install the magnetic pickup and thread into the mounting hole until the tip touches the “in-line”
flywheel gear tooth.
The pickup tip must be directly over a tooth and not between teeth when
adjustment is made.
f. Back the pickup outward (COUNTERCLOCKWISE) 1/2 turn. Hold the pickup securely in this
position and tighten nut (3). This adjustment will result in a clearance of approximately 0.028
inch between the pickup tip and the flywheel teeth and give an operating AC voltage of 4 V to
8 V at the control box terminals 5 and 6 when the engine is running at no load and governed
speed.
CAUTION
OM-2040 / Operation and Maintenance Manual
90D20 / Generator Sets
February 28/94 Revised
Chapter 2-3
Page 11
Summary of Contents for 6921 Series
Page 2: ...This page intentionally left blank ...
Page 223: ......
Page 224: ......
Page 225: ......
Page 226: ......
Page 227: ......
Page 228: ......
Page 229: ......
Page 230: ......
Page 231: ......
Page 232: ......
Page 233: ......
Page 234: ......
Page 235: ......
Page 236: ......
Page 237: ......
Page 238: ......
Page 239: ......
Page 240: ......
Page 241: ......
Page 242: ......
Page 243: ......
Page 244: ......
Page 245: ......
Page 246: ......
Page 247: ......
Page 248: ......
Page 249: ......
Page 250: ......
Page 251: ......
Page 252: ......
Page 253: ......
Page 254: ......
Page 255: ......
Page 256: ......
Page 257: ......
Page 258: ......
Page 259: ......
Page 260: ......