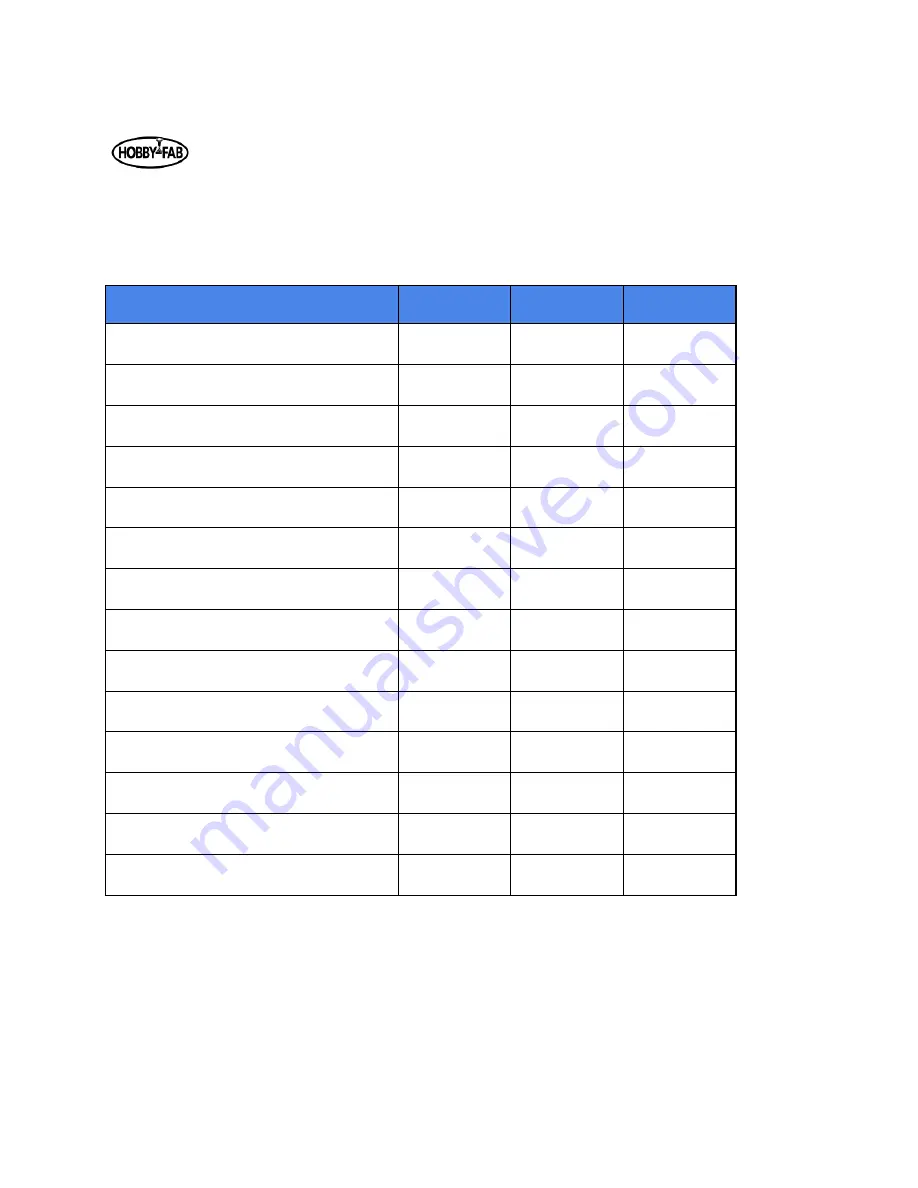
Last updated: 08/13/20108 Rev. 9
22
Step 7:
Step seven will be the build of the Y gantries. Your machine is really going to take shape after this step.
This step is much of a repeat of the last, but we will be mounting end caps instead of Y gantry plates.
Step 7
Qty
Smw3d
Builder
NEMA 23 2.8A
2
6.35x8 Coupler
2
Machined end corner caps
4
Lock collar
2
608ZZ
4
C-Beam 1000mm
2
1.5" spacers
4
M5x55mm bolts
4
M5x20mm bolts
20
Single corner bracket
4
M5 nuts
4
1000mm ACME
2
ACME flange nut
1
Shim: 8mm
4
Each corner bracket holds the ACME in place and retains the build to the board.
Summary of Contents for R7
Page 6: ...Last updated 08 13 20108 Rev 9 6 Limit switch and barrier block shown installed ...
Page 19: ...Last updated 08 13 20108 Rev 9 19 ...
Page 27: ...Last updated 08 13 20108 Rev 9 27 ...
Page 28: ...Last updated 08 13 20108 Rev 9 28 ...
Page 30: ...Last updated 08 13 20108 Rev 9 30 ...