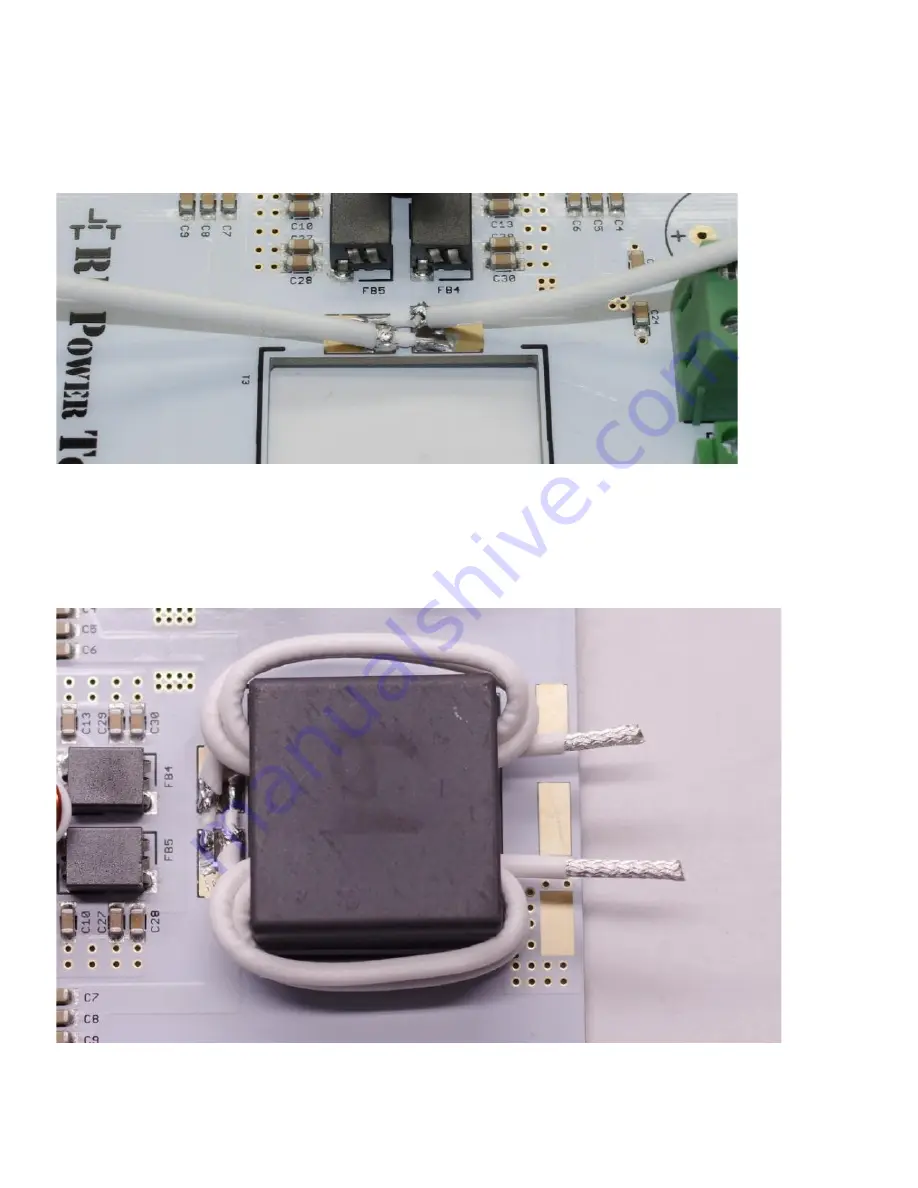
[70]
□
Step 9: T3 Coax to PCB –
Solder the shield of one of the pieces of coax and the center conductor of the
other to one of the pads of T3 on the PCB, repeat the process for the other shield and center conductor.
The pad is split with wider side for the shield and the narrow side for the center conductor.
□
Step 10: Wind T3 –
Place the rectangular core into the opening in the PCB with the holes in the core
adjacent to the coax sections. Pass the coax pieces through the holes in the core then around the outside of the
core and through the hole again a total of three passes through the core.