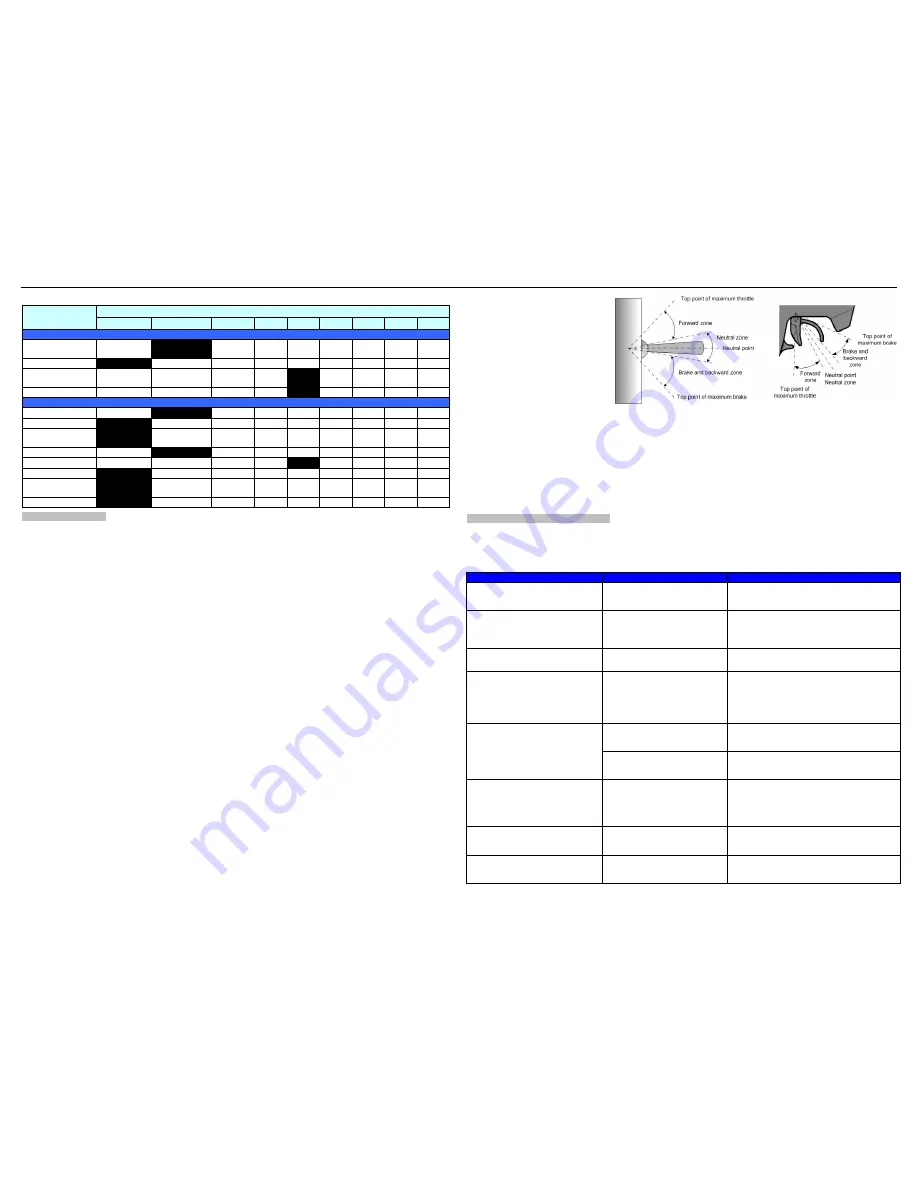
USER MANUAL OF
EZRUN-WP-SC8 & EZRUN-WP-SC10
ESC
HW-SM414ENG-20140305 Page 2 of 3
【
PROGRAMMABLE ITEMS LIST
】
(
The
italics texts in the following form are the default settings
)
1
2
3
4
5
6
7
8
9
1. Running Mode
Forward
with Brake
Forward/Reverse
with Brake
Forward and
Reverse
2.Drag Brake Force
0%
5%
10%
20%
40%
60%
80%
100%
3.Low Voltage
Cut-Off Threshold
Non-Protection
2.6V/Cell
2.8V/Cell
3.0V
/Cell
3.2V
/Cell
3.4V
/Cell
4.Start Mode(Punch)
Level1
Level2
Level3
Level4
Level5
Level6
Level7
Level8
Level9
5.Max Brake Force
25%
50%
75%
100%
Disable
6.Max Reverse Force
25%
50%
75%
100%
7.Initial Brake Force
= Drag Brake
Force
0%
20%
40%
8.Neutral Range
6% (Narrow)
9% (Normal)
12% (Wide)
9.Timing
0.00 °
3.75 °
7.50 °
11.25 °
15.00 °
18.75 °
22.50°
26.25°
10.Over-heat
Protection
Enable
Disable
11.Motor Rotation
Counter
Clockwise
Clockwise
12.Lipo Cells
Auto Calculate
2 Cells
3 Cells
4 Cells
Programmable
Items
Programmable Value
Basic Items
Advanced Items
Programmable Values
1.1.
Running Mode:
In
“Forward with Brake” mode, the car can go forward and brake, but cannot go backward, this
mode is suitable for competition;
“Forward/Reverse with Brake” mode provides backward function, which is suitable for
daily training.
Note:
“Forward/Reverse with Brake” mode uses “Double-click” method to make the car go backward
. When you
move the throttle stick from forward zone to backward zone for the first time (The 1
st
“click”), the ESC begins to brake the
motor, the motor speeds down but it is still running, not completely stopped, so the backward action is NOT happened
immediately. When the throttle stick is moved to the backward zone again (The 2
nd
“click”), if the motor speed is slowed
down to zero (i.e. stopped), the backward action will happen. The
“Double-Click” method can prevent mistakenly
reversing action when the brake function is frequently used in steering.
By the way, in the process of braking or reversing, if the throttle stick is moved to forward zone, the motor will run forward
at once.
“Forward/Reverse” mode uses “Single-click” method to make the car go backward.
When you move the throttle
stick from forward zone to backward zone, the car will go backward immediately. This mode is usually used for the Rock
Crawler.
1.2.
Drag Brake Force:
Set the amount of drag brake applied at neutral throttle to simulate the slight braking effect of a
neutral brushed motor while coasting.
1.3.
Low Voltage Cut-Off:
The function prevents the lithium battery pack from over discharging.
The ESC detects the
battery
’s voltage at any time, if the voltage is lower than the threshold for 2 seconds, the output power will be cut off, and
the red LED flashes in such a way:
“
☆
-,
☆
-,
☆
-
”.
There are 6 preset options for this item. You can customize the cutoff threshold by using a LCD program box (optional
equipment) to trim it with a step of 0.1V, so it will be more suitable for all kinds of batteries (NiMH, NiCd, Li-ion, Lipo,
LFP,etc).
1.4.
Start Mode (Also called
“Punch”):
Select from
“Level1” to “Level9” as your like, Level1 has a very soft start
effect, while level9 has a very aggressive start effect. From Level1 to Level9, the start force is increasing. Please note
that if you choose
“Level7” to “Level9” mode, you must use good quality battery pack with powerful discharge ability,
otherwise these modes cannot get the burst start effect as you want. If the motor cannot run smoothly (the motor is
trembling), it may caused by the weak discharge ability of the battery pack, please choose a better battery or a softer
gear ratio.
1.5.
Maximum Brake Force:
The ESC provides proportional brake function. The brake force is related to the position
of the throttle stick. Maximum brake force refers to the force when the throttle stick is located at the end point of the
backward zone. A very large brake force can shorten the brake time, but it may damage the gears.
The
“Disable” option
inhibits the inherent brake function of the speed controller. When this option is selected, the brake function is realized by
a traditional mechanical disc-brake system driven by a servo.
1.6.
Maximum Reverse Force:
Sets how much power will be applied in the reverse direction. Different value makes
different reverse speed.
1.7.
Initial Brake Force:
It is also called
“minimum brake force”, and it refers to the force when the throttle stick is
located at the initial position of the backward zone. The default value is equal to the drag brake force, so the brake effect
can be very smoothly.
1.8.
Throttle Neutral Range:
Please
refer to the picture on the right side to
adjust the neutral range as your like.
1.9.
Timing:
There
are
many
differences among structures and
parameters
of
different
brushless
motors, so a fixed timing ESC is difficult
to compatible with all brushless motors.
It is necessary to make the timing value
programmable. Please select the most
suitable timing value according to the
motor you are just using. Generally,
higher timing value brings out higher power output, but the whole efficiency of the system will be slightly lower down.
1.10.
Over-Heat Protection:
If the function is activated, the output power will be cut-off when the temperature of the
ESC is higher than a factory-preset value for 5 seconds. When the protection happens, the Green LED will flash in such
a way:
“
☆
-,
☆
-,
☆
-
”.
1.11.
Motor Rotation:
You can use this item to change the rotation direction. Face to the motor shaft (That means the
rear cover of the motor is far from your face), and move the throttle stick to the top point of the forward zone. If this item is
set to
“CCW”, the shaft runs counter-clockwise; If this item is set to “CW”, the shaft runs clockwise.
1.12.
Lipo Cells:
We strongly suggest setting the
“Lipo Cells” item manually because sometimes the default setting
“Auto Calculate” will cause mistake. For example, if you are using a discharged 4S Lipo battery, the ESC may mistakenly
consider it as a fully charged 3S Lipo battery, and then the
“Low voltage cut-off” protection function will be inordinate.
2. Reset All Items To Default Values
At any time when the throttle is located in neutral zone (except in the throttle calibration or parameters program process),
hold the
“SET” key for over 3 seconds, the red LED and green LED will flash at the same time , which means each
programmable item has be reset to its default value.
It needs to be restarted to complete the whole process.
【
TROUBLE SHOOTING
】
Trouble
Possible Reason
Solution
After power on, motor doesn’t work,
and the cooling fan doesn
’t work
The
connections
between
battery pack and ESC are not
correct
Check the power connections
Replace the connectors
After power on
, motor can’t work,
but emits “beep-beep-, beep-beep-”
alert tone. (Every “beep-beep-” has
a time interval of 1 second )
Input voltage is abnormal, too
high or too low
Check the voltage of the battery pack
After power on, red LED always
lights, the motor doesn
’t work
Throttle signal is abnormal
Plug the control wire into the throttle channel
of the receiver correctly.
The motor runs in the opposite
direction when it is accelerated
1)The wire connections between
ESC and the motor are not
correct
2)The chassis is different from
the popular design
Swap any two wire connections between the
ESC and the motor. Or change the
programmable item #11 (Motor Rotation) to
“CW(Clockwise)”
The motor suddenly stops running
while in working state
The throttle signal is lost
Check the transmitter and the receiver
Check the signal wire from the throttle channel
of your receiver
The ESC has entered the Low
Voltage Protection Mode or
Over-heat Protection Mode
Red LED flashing means Low Voltage. Green
LED flashing means Over-heat
When accelerating quickly, the
motor stops or trembles
1) The battery has a bad
discharge performance
2) Gear ratio is too aggressive
3) The
“Start Mode (Punch)” of
the ESC is too aggressive
1) Use a better battery
2) Use lower KV motor or softer gear ratio
3) Set the
“Start Mode (Punch)” to a softer
value
When the throttle stick is in the
neutral range, the red LED and the
green LED flashes synchronously
Over current protection, motor
demagnetization, or motor is
over load
1) Reduce the load (Use softer gear ratio or
reduce the input voltage)
2) Change the motor
Cannot connected with the LED
Program Card or LCD Program Box
Mistakenly uses the Rx wire to
connect
to
the
program
card/box.
Connect the program card/box to the special
pr
ogramming port of the ESC, don’t use the
Rx wire.