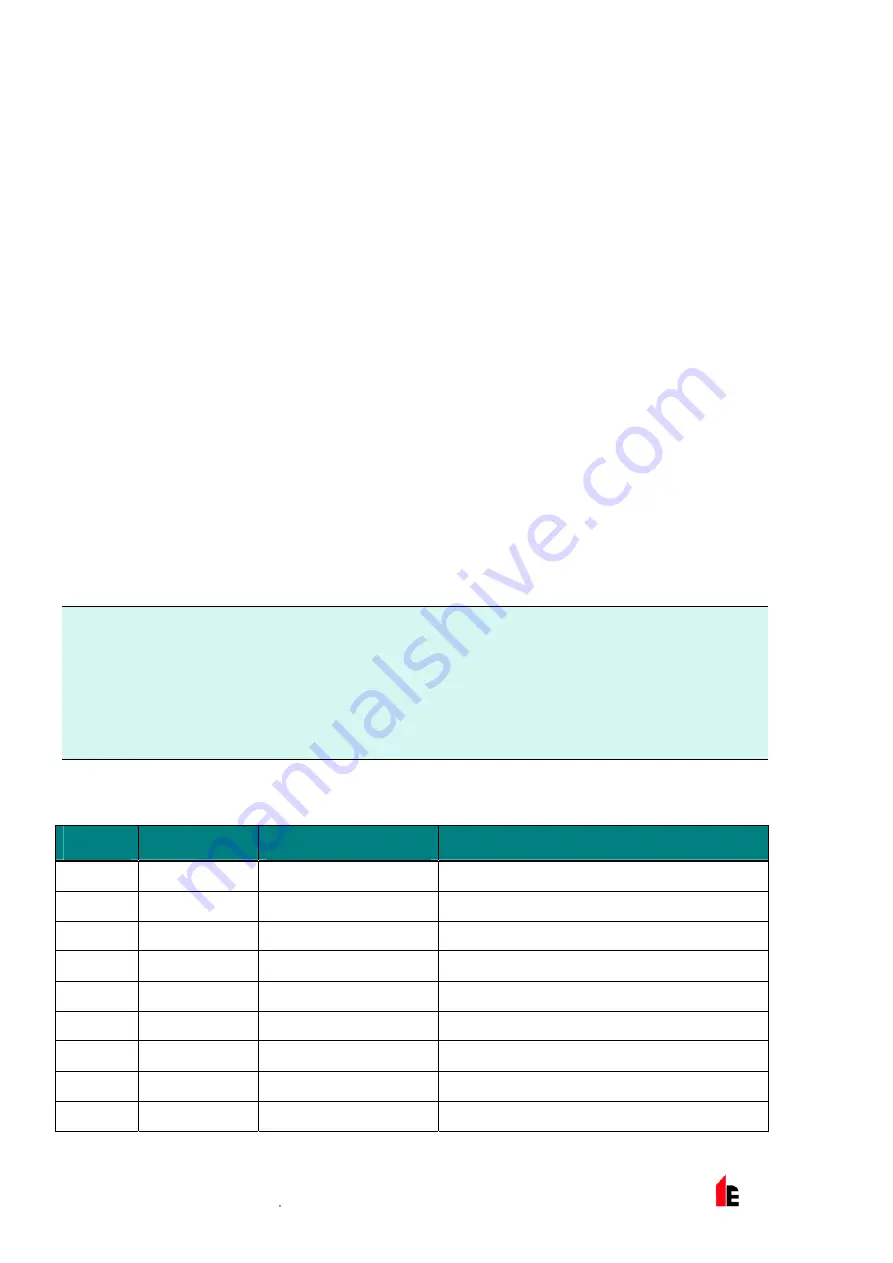
Page 10 of 40
FIRElink-25 – Installation Manual
©
2010 Hochiki Europe (UK) Ltd
9-5-0-344/ISS4/OCT10
2.2 Alarm Levels and Delays Tab
2.2.1
Alarm Levels - (Level subgroup)
The value set in the Fire, Pre-Alarm and Aux functions in the Level subgroup is the relatively scaled
bargraph level at which the appropriate alarm is initiated on the detector. The Fire 2 level assigns an
absolutely scaled alarm level in % obs/m.
The Aux level is set by factory default at level 10 which means that this alarm will occur after the Fire
alarm. The default level settings for Pre-Alarm and Fire 1 are 6 and 8 respectively. The default setting for
Fire 2 is 20% obs/m.
2.2.2
Alarm Delays - (Delay subgroup)
The alarm delay is the number of seconds that an alarm level has to be continuously sensed before the
alarm is initiated. Each alarm level has a programmable delay of between 0 and 90 seconds. The default
delay for each alarm level is 5 seconds.
2.2.3 ClassiFire®
Override
This function has no current use on the FIRElink-25 but is reserved for future expansion purposes.
2.2.4 Alarm
Factor
The detector sensitivity is set with this entry, which will also affect the probability of nuisance alarms. 0 =
high sensitivity, higher probability, 8 = low sensitivity, lower probability. The default alarm factor is 4.
Note: The highest sensitivity setting is suitable for clean, environmentally controlled environments, e.g.
semiconductor manufacturing clean rooms where airborne pollutants are kept to an absolute
minimum and the least contamination is cause for alarm.
Use of this setting in a busy machine shop would lead to relatively frequent nuisance alarms due
to the normal variation of atmospheric contamination and a lower sensitivity setting is
recommended. It is therefore important that the alarm factor chosen is suitable for the area to be
protected. When the appropriate alarm factor for the protected area has been set, nuisance
alarms will be reduced to an absolute minimum.
The following table gives suggested settings of ClassiFire alarm setting for different locations:
0
Extremely High Once per year
Semiconductor manufacturing clean room
1
Once per 5 years
Computer room
2
Once per 10 years
Non-smoking office
3
Once per 50 years
Clean factory
4
Medium
Once per 1000 years
Warehouse
5
Medium
Once per 5000 years
Warehouse with diesel trucks operating
6
Medium
Once per 10000 years
Warehouse with diesel trucks operating
7
Low
Once per 20000 years
Warehouse with diesel trucks operating
8
Low
Once per 100000 years
Warehouse with diesel trucks operating
Alarm
Factor
Sensitivity
Probability of
Nuisance Alarm
Suggested Protected Area