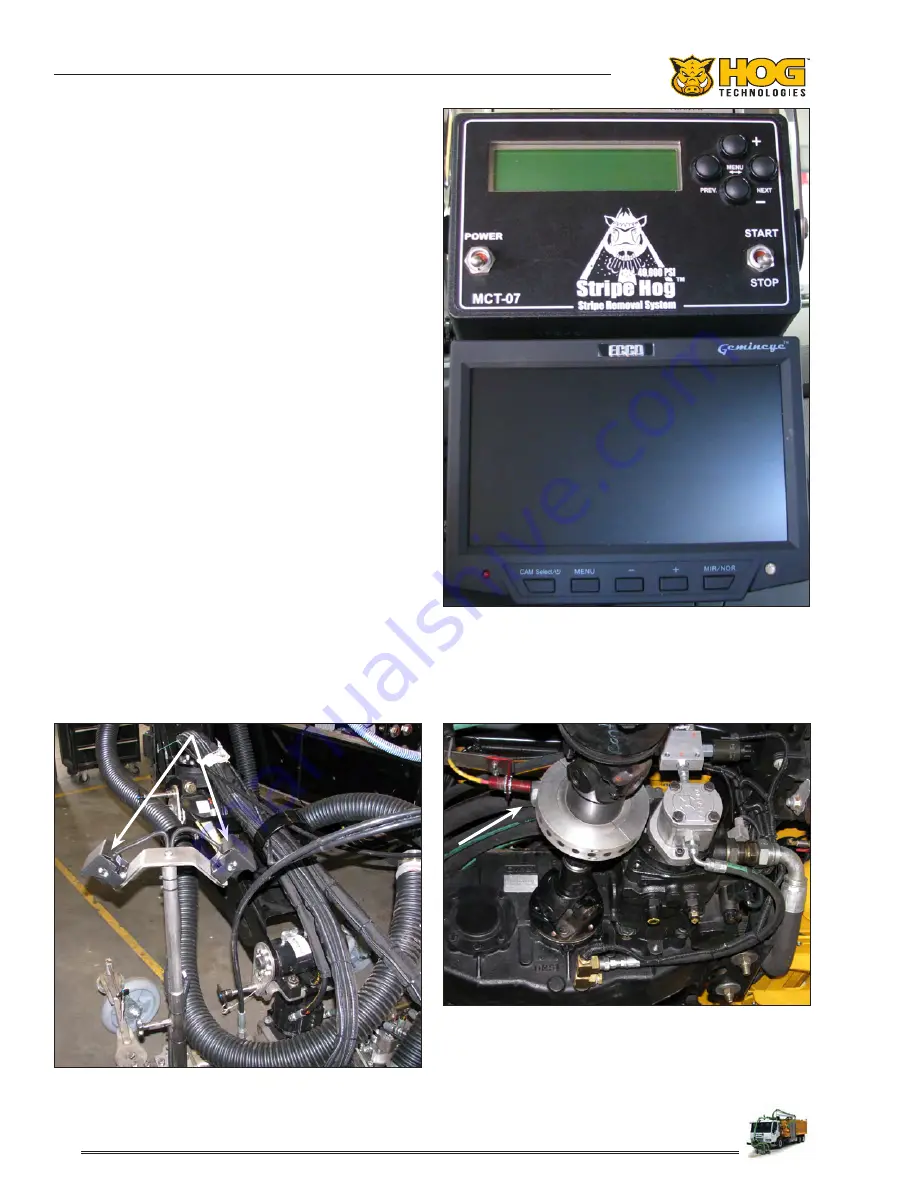
62
62
Section 2 - Stripe Hog Systems
2.11 Skip Meter, & Video System
Skip Meter
Most trucks are equipped with a skip meter that
records the distance traveled while in Work mode.
When the meter is activated, an inductive sensor
records the revolutions of the truck drive shaft and
converts the readings into linear feet or meters.
The data is recorded and saved until the operator
deletes it.
There are two toggle switches on the front of the
meter. One toggle switch turns the meter ON or
OFF, the other toggle switch is used to start the
meter when blasting operations begin and stop
the meter when operations stop or are paused.
Menu buttons select the meter to read in feet or
meters and various recording and data modes.
An operating manual for the Skip Meter has been
included with your Stripe Hog that provides de-
tailed information on its operation and available
data modes.
Video Systems (Optional)
Video systems are optional features that enable
better visibility for the operator while blasting
operations are underway. The video system can
also provide improved visibility while backing the
vehicle. Video systems are unique to the options
selected. Refer to the truck and video manufac-
turers information for instructions on operating
and maintaining video systems.
Skip Meter & Video Screen
Typical Skip Meter Inductive Pickup On Drive Shaft
Typical Hog Head Mounted Video Cameras
Summary of Contents for STRIPE SH7500
Page 1: ...75 H Operations Manual...
Page 2: ......
Page 72: ...72 NOTES...
Page 108: ...108 NOTES...
Page 161: ...161 Section 5 Scheduled Maintenance...
Page 167: ...167 Appendix 2 Tools Spare Parts...
Page 168: ...168 Appendix 2 Tools Spare Parts...
Page 169: ...169 Appendix 3 Daily Report Pre Op Checklist 1 877 HOG ROAD WWW STRIPEHOGSUPPORT COM 60...
Page 178: ...178 NOTES...
Page 185: ......
Page 186: ......