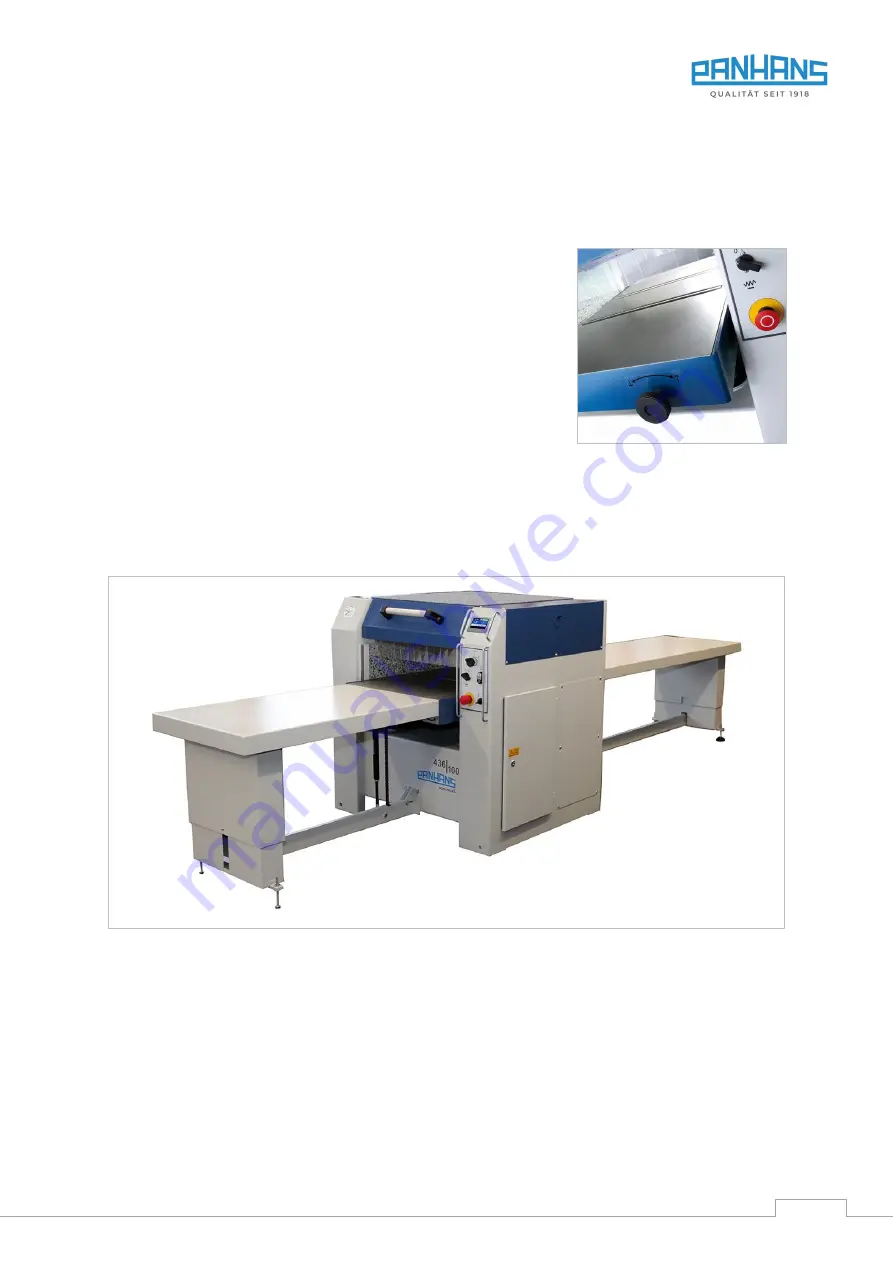
BA_PH_436-100_EN_44-21.docx
36
11
Fine adjustable Table Rollers
(Option)
When equipped with this option, two adjustable table rollers are built into the thicknessing table for better
sliding of the wood.
11.1
Adjusting the Table Rollers
•
The knurled thumbwheel (see figure on the right) is used to adjust the
rollers according to the condition of the wood. The adjustment range is
approx. 1 mm. The planing result deteriorates the higher the table roll-
ers are set.
•
With full stop left, the rollers are in lowest position
→
Use this setting on dry, well-dressed wood.
•
With full stop on the right, the rollers are in the uppermost position
→
Use this setting on damp, resin-rich or non-straightened wood to
ensure safe feeding.
The article number of this option can be found in section
Figure 40: Adjusting the table rollers
12
Thickness Table Extensions
For machining long workpieces, the use of the optionally available thickness table extensions is recommended.
These are available in lengths of 400 mm, 1000 mm and 2000 mm.
Figure 41: Optional table extensions
When attaching the table extensions, make sure that they are aligned on all sides with a spirit level to the correct
height and parallelism to the machine table. The adjustment is made via the adjustment screws attached to the
feet.
For more information on the option and corresponding article numbers, refer to section