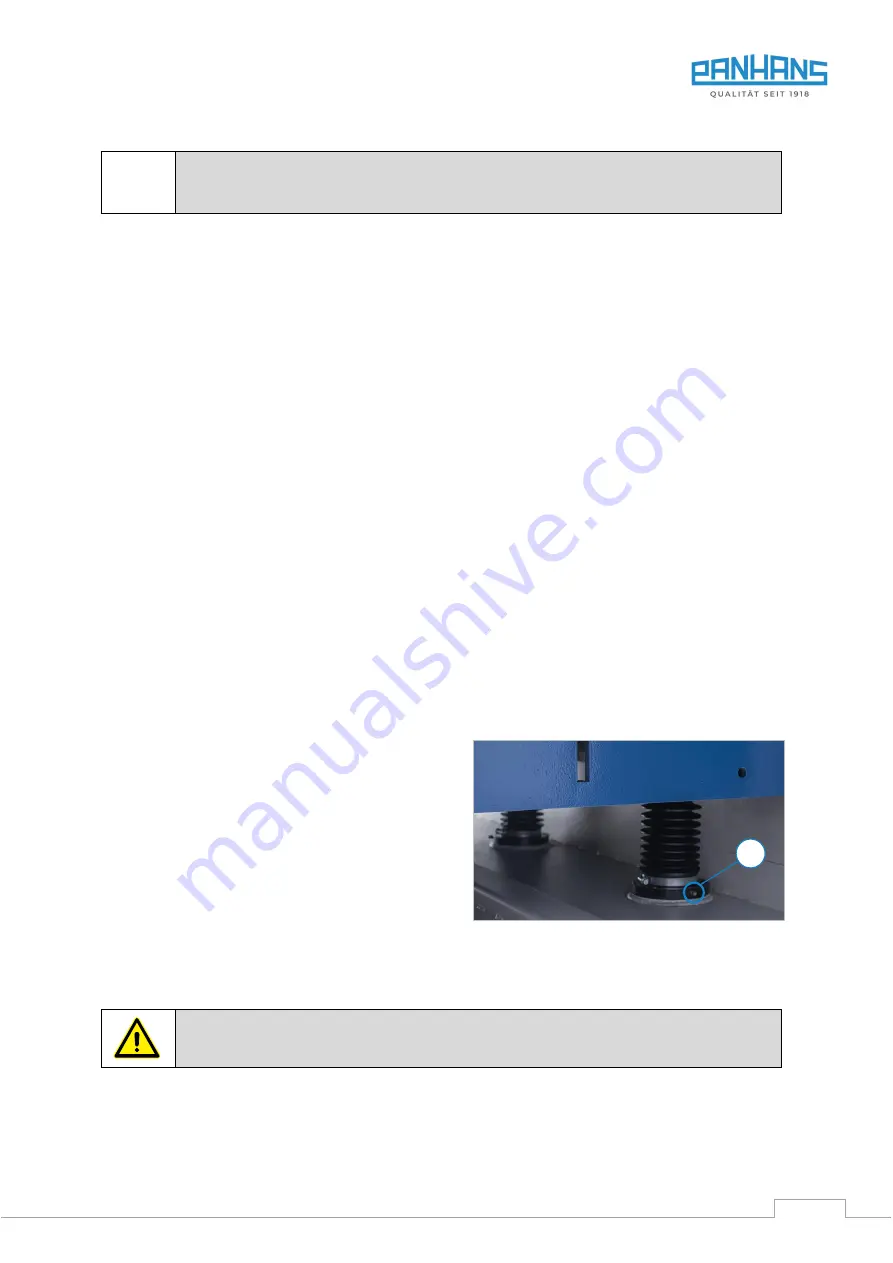
BA_PH_546-100_EN_06-22.docx
48
15
Maintenance and Inspection
Before any maintenance and inspection work is carried out, chapter
4 "Safety" must
be read carefully and observed!
Operational malfunctions caused by insufficient or improper maintenance can result in very high repair costs
and long machine downtimes. Regular maintenance is therefore essential.
•
Clean the machine daily.
•
Check all sliding or rolling parts weekly for smooth running and lubricate with a thin-bodied oil if necessary.
•
The anti-kickback device of the thicknessing table must always be kept in good condition: Therefore, at
least once per work shift, check the contact surface of the anti-kickback fingers for tarnishing and make
sure that they drop down freely under their own weight. If necessary, adjust the anti-kickback fingers ac-
cording to section
•
Inspect electrical equipment/components weekly for externally visible damage and have them repaired by
a qualified electrician if necessary.
•
Immediately remove and replace damaged guards. Never work with damaged equipment!
•
Before starting work, check the extraction system for full function every day.
•
The extraction system must be checked for obvious defects before initial commissioning, daily and monthly
to ensure its effectiveness.
•
The air velocity to the extraction system must be checked before the initial commissioning and after signif-
icant modifications.
•
The function of the gas springs should be checked occasionally. If it takes a lot of force to open the protec-
tive cover, the gas springs must be replaced.
•
Do not use the machine until these conditions are met.
Due to the different operating conditions, it is not possible to determine in advance how often a wear check,
inspection or maintenance is required. Inspection intervals are to be determined appropriately according to the
respective operating conditions.
15.1
Lubrication Instructions
The machine was subjected to a longer test run at the
factory and has already been lubricated ready for oper-
ation. Relubrication before commissioning is therefore
not necessary. Lubricate the machine only with special
grease, e.g.
•
PANHANS ZET-GE M 50
•
ARCANOL BN 102
•
CALIPSOL H442B
•
Shell Gadus S2 V100 3 (ehemals SHELL Alvania 3)
For oil lubrication we recommend:
•
Engine oil 20 W 40
Figure 60: Grease nipples for adjusting spindles
Always use the same grease/oil and the supplied grease gun!
Switch off the machine during maintenance and repair work and secure it against being
switched on again unexpectedly! Lock the main switch with a padlock!
•
Check all sliding or rolling parts weekly for smooth running and lubricate with a thin oil if necessary.
•
Lubricate feed chain every 6 months with a suitable grease.
•
Apply weekly a few drops of oil on the threads of clamping and adjusting levers.
•
Lubricate the 4 adjusting spindles (
N
) of the thicknessing table monthly with 2 grease shots (
N