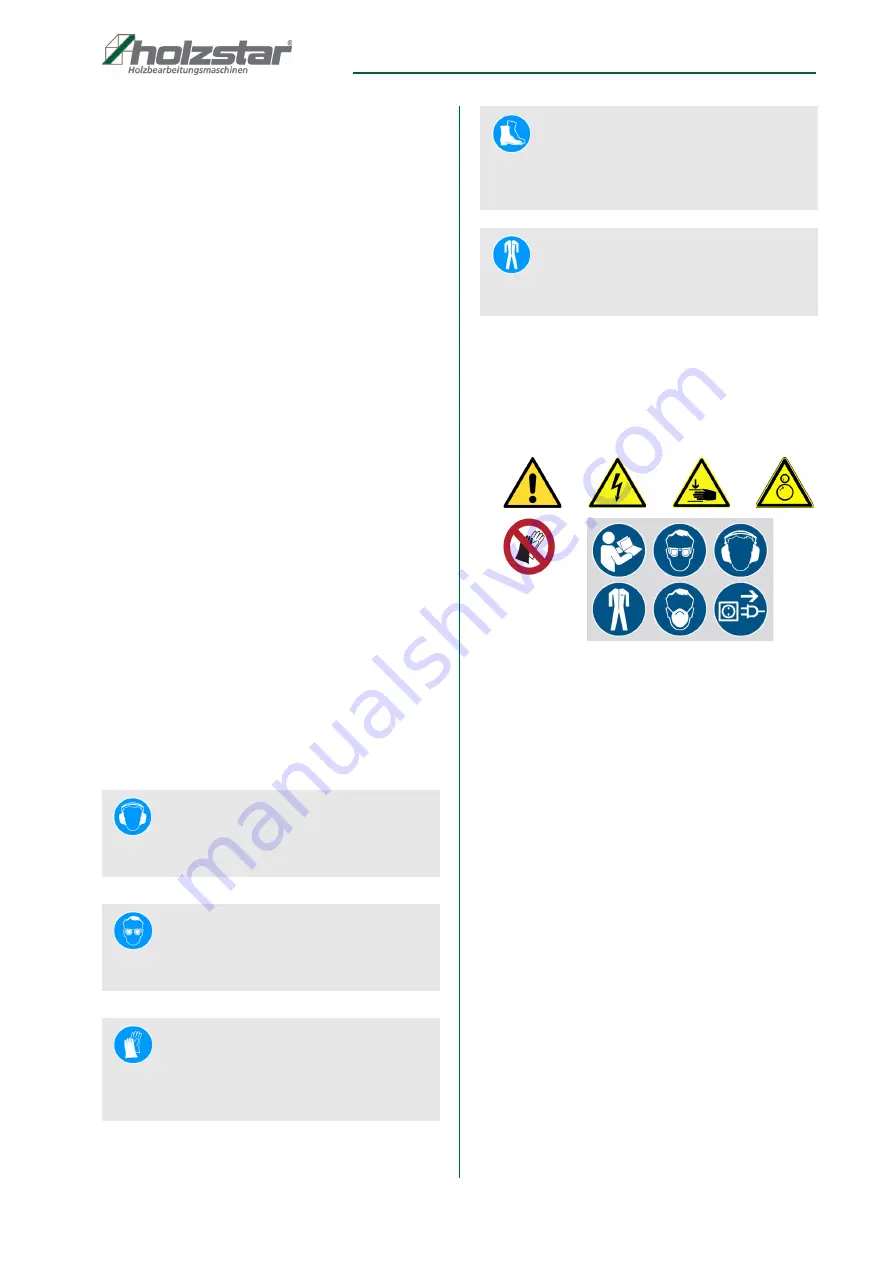
Safety
ADH-Series | Version 1.05
5
resulting from improper behaviour. Tasks which go bey-
ond normal operation may only be carried out by the
operator if they are listed in the operation manual and
the operator has made him/herself familiar with them.
Qualified electrician:
Due to the electrician's specialised training, know-how,
experience and knowledge of pertinent standards and
regulations the electrician is in a position to work on the
electrical systems, and autonomously identify and avoid
potential hazards.
Specialist staff:
As a result of specialist training, expertise, experience
and skills in terms of the relevant standards and regula-
tions, specialist staff is able to complete the tasks they
are entrusted with and independently identify hazards
and avert risks.
Manufacturer:
Certain work must be carried out by manufacturer
specialist staff only. Other staff is not permitted to carry
out this work. Contact our customer service to have the
work carried out.
2.4 Personal protective equipment
Personal protective equipment is intended to protect the
health and safety of persons at work. Staff must wear the
personal protective equipment indicated in individual
sections of these operating instructions when carrying
out the different tasks on the machine.
The personal protective equipment is described in the
following section:
2.5 Safety labels on the Planer-Thicknesser
The following safety labels and instructions are attached
to the Planer-Thicknesser s (Fig. 1) and must be
observed.
Fig. 1: Safety labels:1 Warning of dangers | 2 Warning of dangerous
electrical voltage | 3 Warning of hand injuries
4 Warning of entanglement hazard | 5 Use of gloves prohibited
6 Safety instructions
If safety labels on the machine are damaged or missing,
this can cause errors, personal injury and material
damage. The safety symbols attached to the machine
must not be removed. Damaged safety symbols must
be replaced immediately.
As soon as the signs are not clearly visible and com-
prehensible at first glance, the machine must be stop-
ped until new signs have been attached..
2.6 Safety devices
Kickback guard
When thicknessing, the kickback guards prevent the
workpiece from kicking back. It must not be bent.
Safety switch of the chip extraction hood
The safety switch of the chip extraction hood is installed
under the work table. When the chip extraction hood is
not mounted, the switch prevents the starting the
engine.
Ear protection
The hearing protection protects the ears against
damages of hearing due to noise.
Eye protection
Protective glasses protect the eyes against pro-
jected parts and splashes of liquid.
Protective gloves
Protective gloves protect the hands from com-
ponents with sharp objects as well as friction, abra-
sion, and deep-cut injuries.
Safety boots
The safety boots protect the feet against crushes,
falling parts and slipping over on slippery under-
ground.
Protective clothing
Protective work clothing means tight-fitting clothing
with low tear resistance.
2
3
1
4
6
5
Summary of Contents for ADH 200
Page 1: ...Instruction manual ADH S ERIES Planer Thicknesser ADH 200 ADH 250 ADH 305 ADH 250 ADH 200 ...
Page 19: ...Spare parts ADH Series Version 1 05 19 Fig 18 Spare parts drawing ADH 250 ...
Page 20: ...20 ADH Series Version 1 05 Spare parts Fig 19 Spare parts drawing ADH 305 ...
Page 22: ...www holzstar de ...