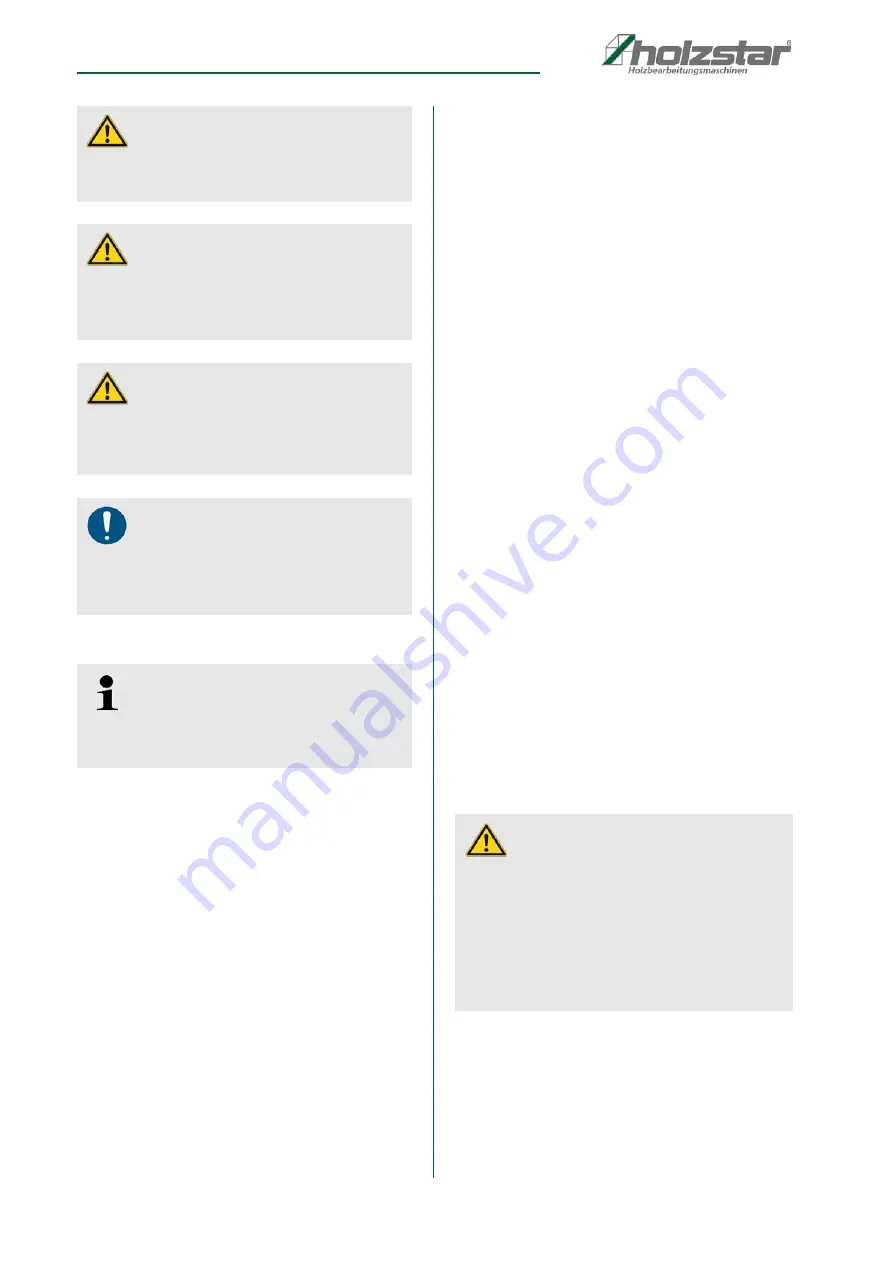
4
ADH-Series | Version 1.02
Safety
Tips and recommendations
Observe the safety information in these operating in-
structions to minimise the risk of personal injury as well
as material damage and prevent hazardous situations.
2.2 Operator responsibility
Operators are defined as the persons who operate the
machine for commercial or profitbased purposes or pro-
vide the machine to third parties for use or application
and bear the legal product responsibility in terms of the
protection of users, staff or third parties during operation.
Obligations of the operator:
If the machine is used for commercial purposes, opera-
tors are subject to the legal stipulations in terms of occu-
pational safety. For this reason, the safety instructions in
these operating instructions as well as the safety, acci-
dent prevention and environmental protection regulati-
ons valid at the installation location must be complied
with. In this process, the following shall apply in
particular:
- Operators shall obtain information about valid oc-
cupational safety regulations and determine addi-
tional hazards as part of a risk assessment which
result from the specific operating conditions at the
machine's installation location. Said risk as-
sessment shall be reflected in operating instructi-
ons for machine operation.
- During the entire machine operating time operators
must check whether the operating instructions they
created meet current standards and adapt the ope-
rating instructions where necessary.
- Operators shall clearly manage and specify the re-
sponsibilities for installation, operation, trouble-
shooting, maintenance and cleaning.
- Operators must make sure that all persons hand-
ling the machine have read and understood these
operating instructions. Operators must also regu-
larly train staff and notify of the hazards.
- Operators shall provide staff with the required pro-
tective equipment and wearing the required protec-
tive equipment shall be mandatory.
Operators shall also be responsible for maintaining the
machine in a technically perfect condition. For this rea-
son, the following shall apply:
- Operators shall make sure that the maintenance in-
tervals described in these operating instructions
are complied with.
- Operators shall regularly check that the safety
equipment is fully functional and complete.
2.3 Operating staff qualification
The different tasks described in these operating instructi-
ons require different levels of skills in terms of the qualifi-
cations of operating staff working with the machine.
Exclusively persons of whom it can be expected that they
reliably complete assigned tasks shall be authorised to
carry out any tasks. Persons whose reactions have been
impaired shall not be authorized, e.g. drug users, users
under the influence of alcohol or medication.
These operating instructions specify the following perso-
nal qualifications for the different tasks:
DANGER!
This combination of symbol and signal term indica-
tes a immediate dangerous situation which may
cause death or serious injury if not averted.
CAUTION!
This combination of symbol and signal term indica-
tes a potentially hazardous situation which may
cause minor or light injuries if it is not averted.
ATTENTION!
This combination of symbol and signal term indica-
tes a potentially dangerous situation which may
cause material damage or harm the environment if it
is not averted.
NOTE!
This combination of symbol and signal term indic tes
a potentially dangerous situation which may cause
material damage or harm the environment if it is not
averted.
Tips and recommendations
This symbol highlights useful tips and recommendati-
ons as well as information for efficient and reliable
operation.
WARNING!
Risk from inadequately qualified
persons!
Inadequately qualified persons are unable to assess
the risks when handling the machine, thus putting
themselves and others at risk of severe injuries.
- All work must be carried out by qualified persons
only.
- Keep inadequately qualified persons and children
away from the work area.
Summary of Contents for ADH 2540 230V
Page 26: ...www holzstar de ...