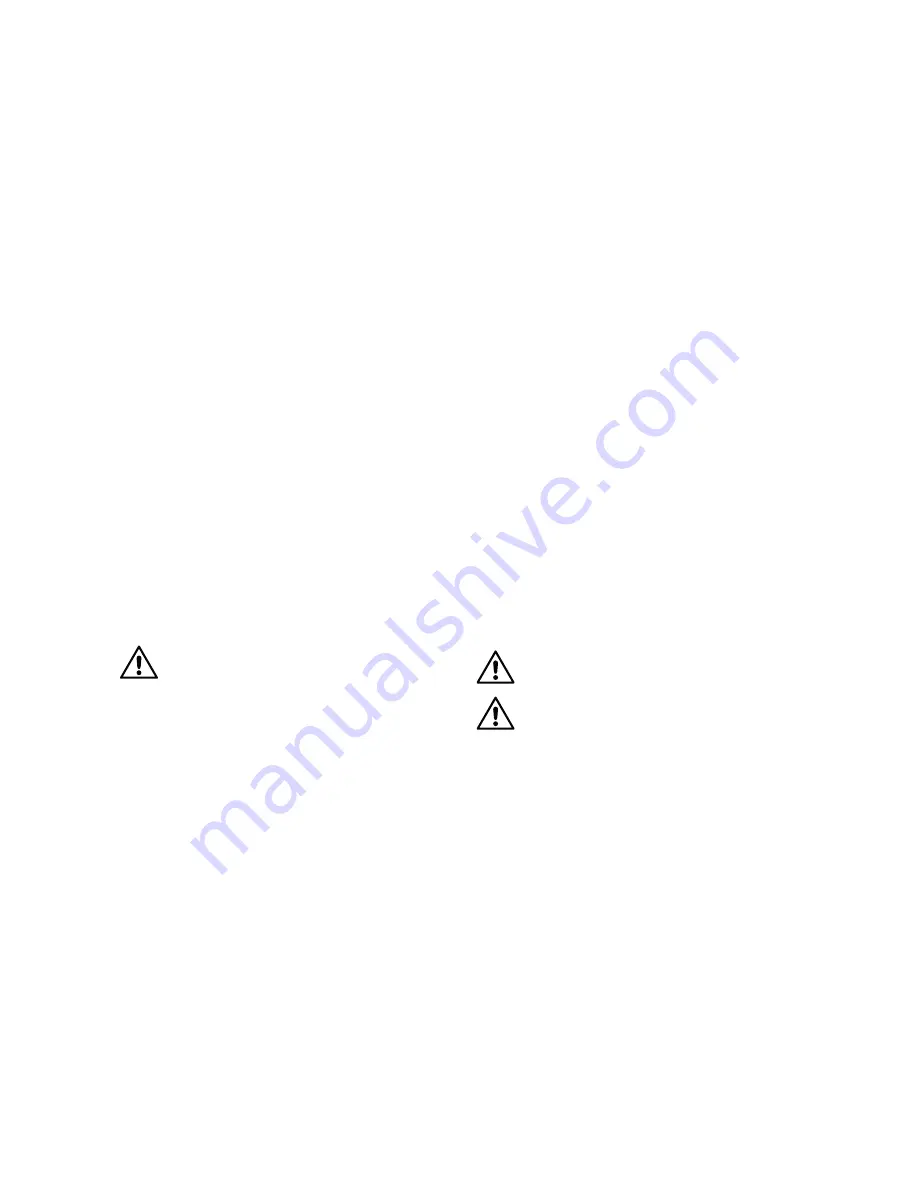
EngliSH | 27
Connecting the pressure sensors (Saniquick UFT)
When connecting the PVC hose to the nipple of the con-
trol unit, perfect tightness must be ensured. To ensure
that the control unit functions perfectly, it is important to
ensure that the PVC hose is laid in a continuously rising
line from the Pitot tube to the control unit without loops,
bends and without being crushed.
Automatic float switch (Saniquick UF)
If the water level increases to a determined maximum lev-
el (switching point), the floating float switches the pump
automatically on. If the water level is sunk to a determined
minimum level (tripping point) due to pumping down, the
float switches the pump off. The reacting distance, e.g.
the water level difference between switching point and
tripping point can be determined individually.
Please note the following information for perfect function:
•
The mountings as well as the length of the freely
moveable end of the float cable must be adjusted to
the desired switch level. It has to be ensured here
that the switch level of the pump is below the en-
trance pipe so that an obstruction of the pumping
medium can be avoided. The tripping point must be
above the upper edge of the pump casing so that no
air pockets can develop in the pump, which requires
under circumstances de-aerating of the pump.
•
Under no circumstances the float with the cable must
be thrown into the medium, since correct switch is
only possible with a rotational movement of the float
around the mounting point of the cable. Possible con-
sequences in the event of non-compliance are flood-
ing (the pump does not start)/destruction of the pump
due to dry run (the pump does not switch off).
After each change of the mounting of the float a cor-
rect function of the float switch must be checked
with a test run.
Assembly of pump and installation kit at Saniquick UF
The lifting system consists of 3 components, the shaft,
the installation kit and the pump.
For the assembly, proceed as follows:
1. Screw the check valve, included with the pump, to
the pressure outlet of the pump. Use a suitable seal-
ing tape to seal the threaded screw.
2. Screw the stem extension to the check valve. Also,
use a suitable sealing tape for sealing.
3. Put the unit into the shaft and align the pump so that
it can float freely from the float unit and cannot stick
to the shaft or the internals.
4. Connect the stem extension to the pressure outlet
of the chute by tightening the nut of the stem ex-
tension.
Installation of the shaft extension
1. Lift the cover plate with frame and bottom drain off
of the storage tank and pull out the compensation
framework.
2. Place the shaft extension into the storage tank until
the desired height has been achieved.
3. Then, place the compensation framework back onto
the shaft extension. Place the cover plate with bot-
tom drain back onto the compensation framework.
5.3. Commissioning
This chapter contains all important instructions for oper-
ating personnel for safe commissioning and operation of
the machinery. The following must be complied with and
checked:
•
Type of installation
•
Operation mode
•
Minimal submersion in water / maximum submersion
depth
After a longer downtime these points must also be
checked and detected defaults must be repaired!
The operation and maintenance manual must always
be kept with the machinery, or in a dedicated place
where it is accessible for the entire operating person-
nel.
The following points must be taken into account to avoid
personal and material damage when troubleshooting ma-
chinery failures:
•
The commissioning of the machinery must only be
carried out by qualified and trained personnel in com-
pliance with the safety regulations.
•
All personnel that is working on the machinery must
have received, read and understood the operating in-
structions.
•
Activate all safety equipment and emergency switch-
offs before commissioning.
•
Electrotechnical and mechanical settings must only
be carried out by specialists.
•
This machinery is only suitable for the use under the
indicated operating conditions.
Never let the pump run dry for longer periods of time
(risk of overheating).
Before commissioning the system, existing pipe
valves or gate valves must be opened.
5.4. Preparatory work
The machinery was constructed and fitted according to
the latest technology, so that it works for a long time and
reliably under normal operating conditions. This requires
however that you comply with all requirements and infor-
mations. Small oil leakages of the floating ring seals on
delivery are not problematic, but they must be removed
before lowering/immersion into the medium.
Please check the following points:
•
Cable run - no loops, slightly tightened
•
Check temperature of the medium and submersion
depth - see machinery data sheet
•
If a tube is used for pressure, this must be rinsed with
clear water so that no deposits lead to obstruction.
•
The pump pit must be cleaned for wet installation
•
The pressure-sided and suction-sided pipework sys-
tem must be cleaned and all gate valves must be
opened
•
The pump casing must be flooded, e.g. it must be filled
completely with the medium and it must not contain an air.
The de-aeration can be carried out by means of suit-
Summary of Contents for C250WA
Page 33: ...English 33 Notizen Notes ...
Page 65: ...Nedlerlands 65 Notizen Notes ...
Page 70: ...70 Notizen Notes ...
Page 71: ...71 Notizen Notes ...