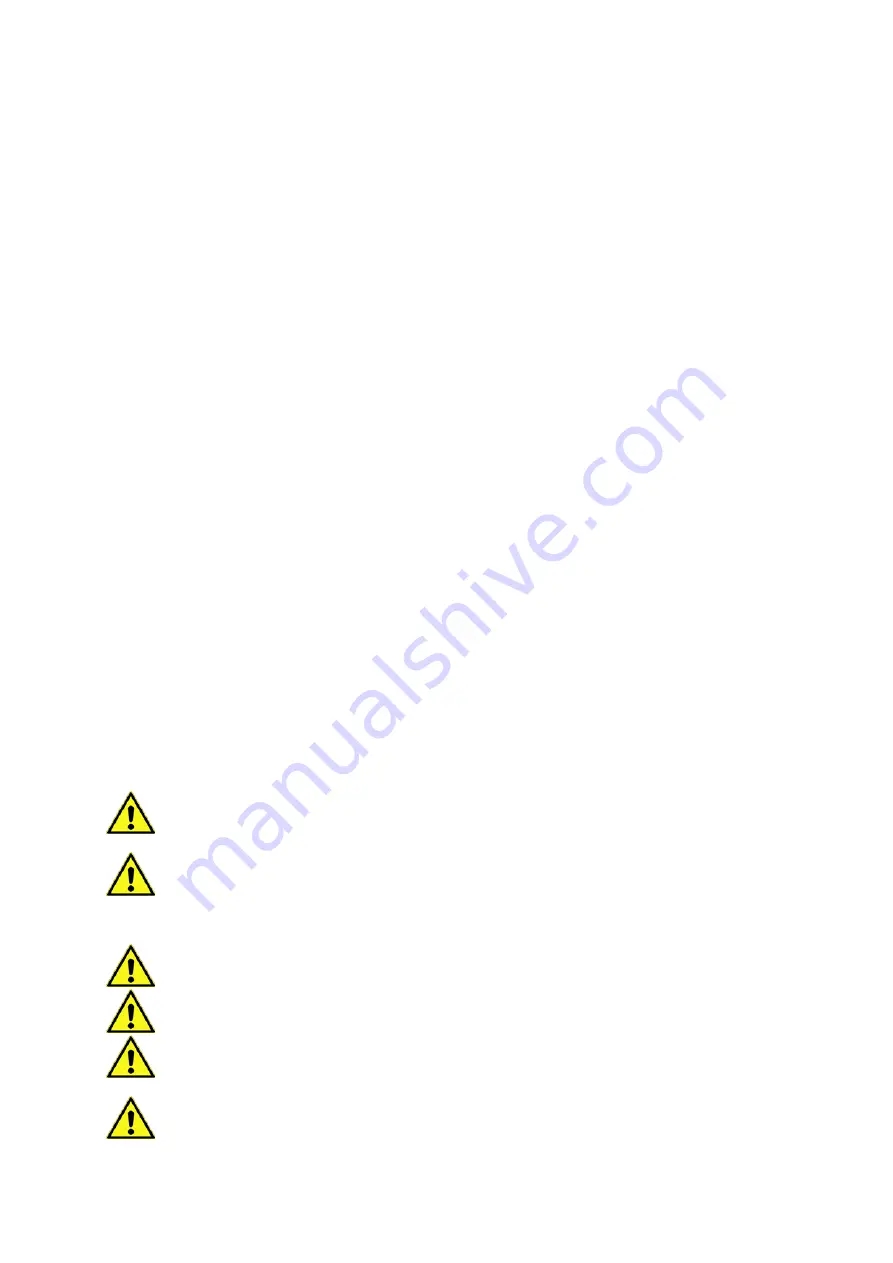
47
6. Maintenance
6.1 General
The machine and the entire system must be inspected and maintained at regular intervals. The time limit for
maintenance is set by the manufacturer and applies to the general conditions of use. The manufacturer should be
consulted if the system is to be used with corrosive and/or abrasive pumped liquids, as the time limit between
inspections may need to be reduced.
Note the following information:
•
The operating and maintenance manual must be available to the maintenance personnel and its
instructions followed. Only the repair and maintenance measures listed here may be performed.
•
All maintenance, inspection and cleaning work on the machine and the system may only be carried
out by trained specialists exercising extreme care in a safe workplace. Proper protective clothing is
to be worn. The machine must be disconnected from the electricity supply before any work is carried
out. There must be no way that it can be inadvertently switched on. Additionally, the appropriate
protective measures as defined by the BGV/GNV should be enforced when working in basins and/or
containers.
•
Above a weight of 50kg, only hoisting gear which has been officially approved and which is in a
technically perfect condition should be used for lowering and raising the machine.
Make sure that all fastening devices, ropes and safety devices of the hand winch are in a technically
perfect condition. Work may only commence if the auxiliary hoisting gear has been checked and found to
be in perfect working order. If it is not inspected, danger to personnel may result!
•
Wiring work on the machine and system must be carried out by an electrician. For machines
approved for work in areas subject to explosion danger, please refer to the “Explosion protection in
accordance with the regulation” chapter.
•
When working with inflammable solvents and cleaning agents, fires, unshielded lighting and
smoking are prohibited.
•
Machines which circulate fluids hazardous to health, or which come into contact with them, must be
decontaminated. It must be ensured that no dangerous gases can form or are present.
•
Ensure that all necessary tools and materials are available. Tidiness and cleanliness guarantee safe
and problem-free operation of the machine. After working on the machine all cleaning materials and
tools should be removed from it. All materials and tools should be stored in an appropriate place.
•
Operating supplies such as oil and lubricants must be collected in appropriate vessels and properly
disposed of (in accordance with the 75/439/EEC directive and with §§5a, 5b AbfG). Appropriate
protective clothing is to be worn for cleaning and maintenance jobs. This is to be disposed of in
accordance with waste code TA 524 02 and EC Directive 91/689/EEC. Only lubricants expressly
recommended by the manufacturer may be used. Oils and lubricants should not be mixed. Only use
genuine parts made by the manufacturer.
A trial run or functional test of the machine must be performed as instructed in the general operating
conditions.
Before maintenance or repair disconnect the mixer from the power supply to prevent accidental starting
of the mixer!
In accordance with the product liability law we point out that we shall not be liable for damages caused by
our product due to unauthorized repair by persons other than the manufacturer or an authorized workshop or due
to the use of spare parts other than original HOMA parts. The same product liability limitations are valid for
accessories.
Before maintenance or repair make sure that all rotating parts stand still!
Before carrying out maintenance and service, the mixer must be thoroughly flushed with clean water.
When loosening of the oil chamber control screw, overpressure can escape. Release the screw only
when pressure balance is secured.
If not otherwise stated, the torque values of the be-low tables should be used.
Values stated are for clean, lubricated screws.