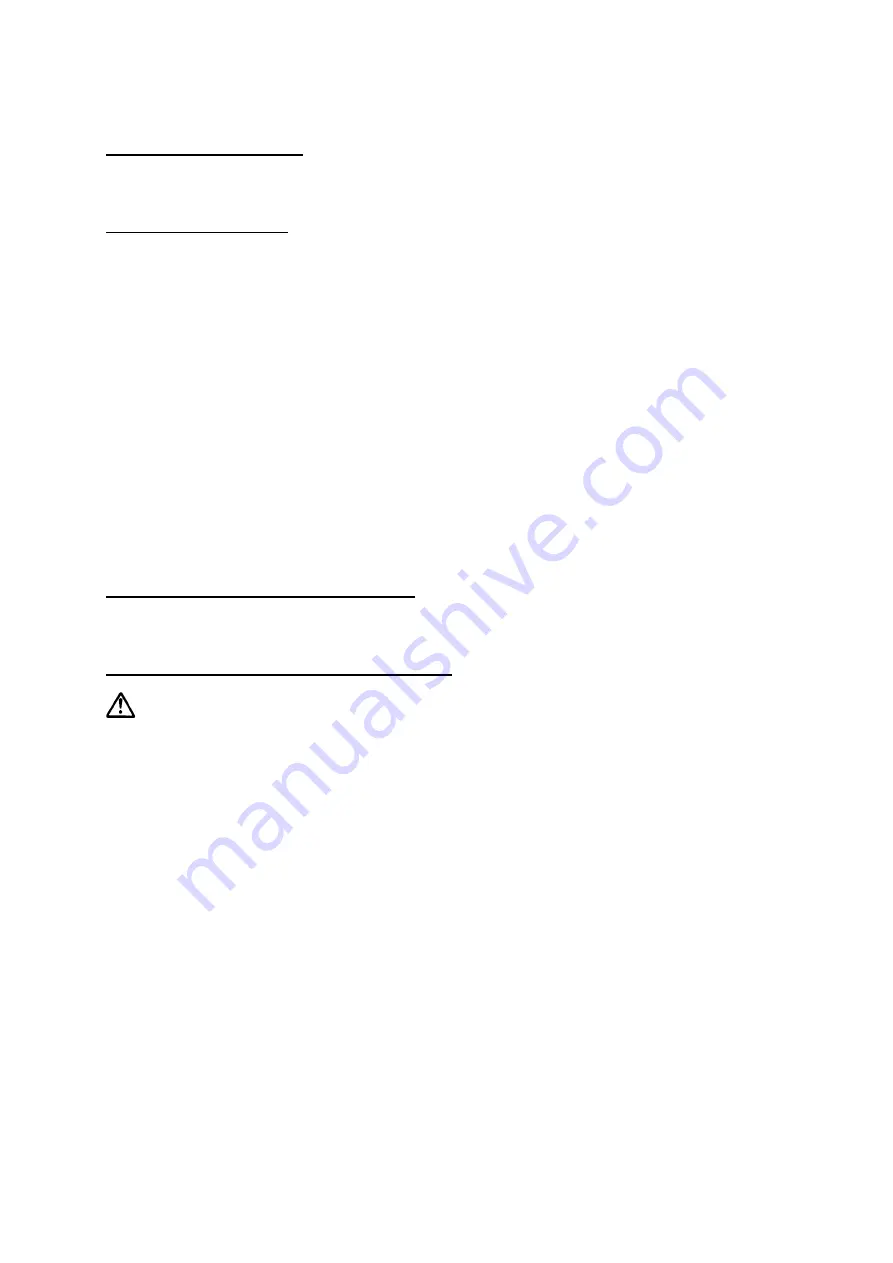
50
7. Additional for FM submersible pumps
7.1. GENERAL INSTRUCTIONS
This manual is intended to provide basic installation and start-up guidance. It is to be read and thoroughly studied
prior to attempting to install or operate any of the equipment supplied. Equipment damage, which occurs by not
following these instructions will void the warranty.
7.2. SAFETY PRECAUTIONS
Only trained qualified personnel shall be utilized for installation and start-up.
The following is a general list of safety precautions that should be followed when installation starting-up or
servicing the pump
.
The pump station owner or operator is ultimately responsible for ensuring that all equipment is installed,
started up and operated in a safe manner.
•
Do not work alone.
•
Double check to make sure that all lifting equipment is in good working order and that it has adequate lifting
capacity for the weight that it will handle.
•
Wear safety helmet, goggles and protective shoes, or appropriate safety materials required.
•
Before working on the pump make sure that the power is disconnected and cannot be energized by others.
Lockout and tag the control panel circuit breaker.
•
Do not stand under suspended loads!
•
Never enter or work within a wet well without first checking to make sure sufficient oxygen is present and that
there are no explosive or poisonous gases present.
•
All personnel, who work with sewage pumping equipment and systems shall be vaccinated against diseases
that can occur. If there are any questions or doubts in this area it is strongly suggested that the local health
agency be contacted.
•
For Hazardous Area Classifications, only use pumps with suitable Explosion Proof Rating.
7.3. EQUIPMENT INVENTORY AND INSPECTION
Upon arrival of pump shipment carefully unpack all components and compare with shipping and purchase order
documents to ensure that the order is complete. Also inspect equipment for any damage that might have occurred
in shipment. If any problems are detected contact an authorized HOMA customer service immediately.
7.4. TRANSPORTATION AND STORAGE PROCEDURE
Always lift the pump by its lifting bail or eye bolt.
Never lift the pump by its power cable! Jacketed pump should never stored or shipped with the
pump by the jacket. Damage to Sealing O ring may result.
Pumps should be stored in an upright position, taking extreme care to protect the power cable and control cables
from crushing, nicks or tears which would permit water intrusion.
Power cable ends must be protected from immersion in water as well as moisture intrusion. The cable will wick
water into the pump if it is not protected properly. Power cable leads should be covered with shrink tubing or
suitable sealing material during storage.
Short Term Storage
: Short term storage is defined as any time less than six months. We recommend that pump
and accessories be stored in its original shipping container in a dry, temperature controlled area. If climate
controlled storage is not possible, all exposed parts should be inspected before storage and all surfaces that have
the paint scratched, damaged or worn should be re-coated with air dry enamel paint. The pump should be stored
in an upright position.
Long Term Storage
: Any storage time exceeding six months is considered long term. In addition to the
safeguards specified above, the impeller should be rotated once a month to prevent the mechanical seals from
being damaged, and the pump should be inspected. The seal chamber oil should be drained and replaced prior to
commissioning. The pump should be stored in an upright position.