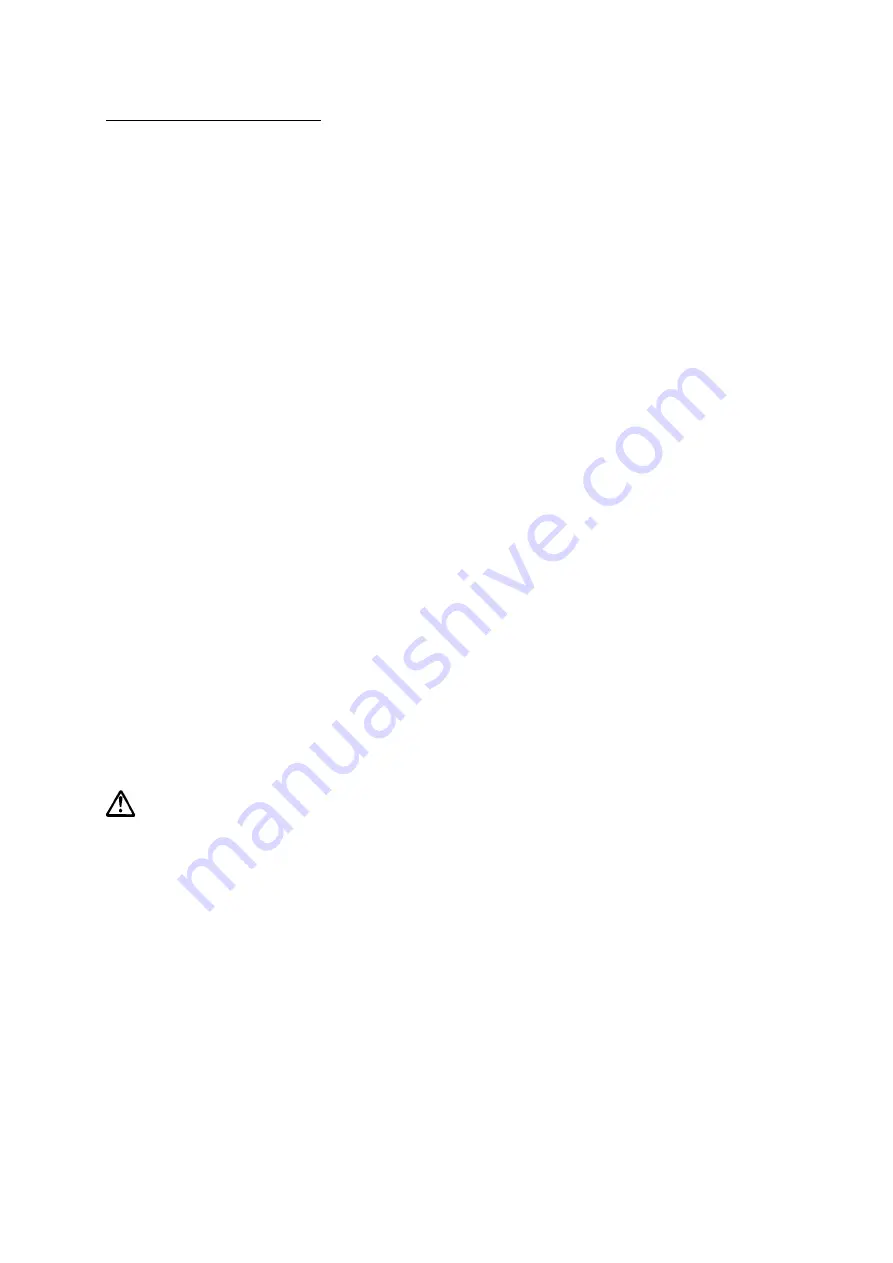
51
7.5. ELECTRICAL INSTALLATION
7.5.1. GENERAL GUIDELINES
All electrical work shall be carried out under the supervision of an authorized, licensed electrician.
The present
state adopted edition of the National Electrical Code as well as all local codes and regulations shall be
complied with.
7.5.2. VERIFICATION OF POWER SUPPLY
Prior to making any electrical connections or applying power to the pump, compare the power supply available at
the pump station to the data on the unit's nameplate. Confirm that both voltage and phase match between pump
and control panel. The voltage supplied at the pump shall be +5 / -10% of the nameplate value, frequency shall be
+ / - 1% of the nameplate value, the voltage phase balance shall be within 1% and the maximum corrected power
factor shall be 1.0.
7.5.3. POWER LEAD WIRING
HOMA pumps may be provided with 1 or more cables, depending on motor horsepower and operating voltage.
Power leads L1, L2, & L3 may be provided as single conductor, or as multiple conductors. Multiple conductor
configurations may use leads from separate cables, or may use two conductors within one cable. Please refer to
wiring diagram in the appendix for specific connection details. The pump must be connected electrically through a
motor starter with proper circuit breaker protection in order to validate warranty. Do not splice cables.
7.5.4. THERMAL SWITCH WIRING
Pumps are equipped with thermal switches embedded in the stator windings which are normally closed,
automatically resetting switches. Switches will open when the internal temperature rises above the design
temperature, and will close when the temperature returns to normal. Thermal switches must be wired to a current
regulated control circuit in accordance with the NEC.
Identify thermal switch leads marked T1 and T3 in the power or control cable.
The resistance across the leads will be 0.5 Ohms. Thermal leads must be connected to the thermal overload relay
located in the control panel. Thermal switch leads must be connected to validate warranty.
Note: All sizes of Class 1, Div. 1 pumps for hazardous service must have thermal switch leads connected
to a current regulated control circuit in accordance with NEC.
7.5.5. SEAL PROBE WIRING
The mechanical seal leak detector probe utilized in the pump is a conductive probe which is normally open. The
intrusion of water into the seal chamber completes the electrical circuit. Control panel provisions will sense this
circuit closure, and will provide indication or alarm functions depending on the panel design.
Either single or dual wire systems may be provided. Single wire systems utilize one energizing conductor, and the
pump casing and neutral lead as the ground or return portion of the circuit. The dual wire systems utilize two
separate conductors for each leg of the circuit.
With either system, the seal probe leads must be wired into a control circuit provided in the control panel. This
control circuit must energize the probe with a regulated power source, and sense the closed circuit in event of
water intrusion Indication and alarm functions must also be provided in the control circuit. Please see control
panel wiring diagram for seal probe connection points.
For Hazardous Area Classification Pumps, leak detector circuit must be in conformance with applicable NEC
codes and regulations.
7.5.6. START / RUN CAPACITORS AND RELAYS:
All single phase motors require start and run capacitors along with a start relay to operate. Capacitors and relays
must be sized for the specific motor.
Capacitors are sized based on ideal conditions.
The run capacitor may need to be resized to match the available field voltage. Each cap kit shipped is supplied
with a wiring diagram and start up procedure.
7.5.7. Variable Frequency Drives
Special considerations must be taken when operating pumps with variable frequency drives (inverters).
The inverter circuit design, horsepower required by pump, motor cooling system, power cable length, operating
voltage, and anticipated turndown ratio must be fully evaluated during the design stage of the installation.
As a minimum, properly sized load reactors and filters must be installed between the inverter and the
pump to protect the pump motor from damaging voltage spikes.
Warranty coverage will not be provided on
any pump motor that is operated with a variable frequency drive, unless the load side of the inverter is properly
isolated from the pump.