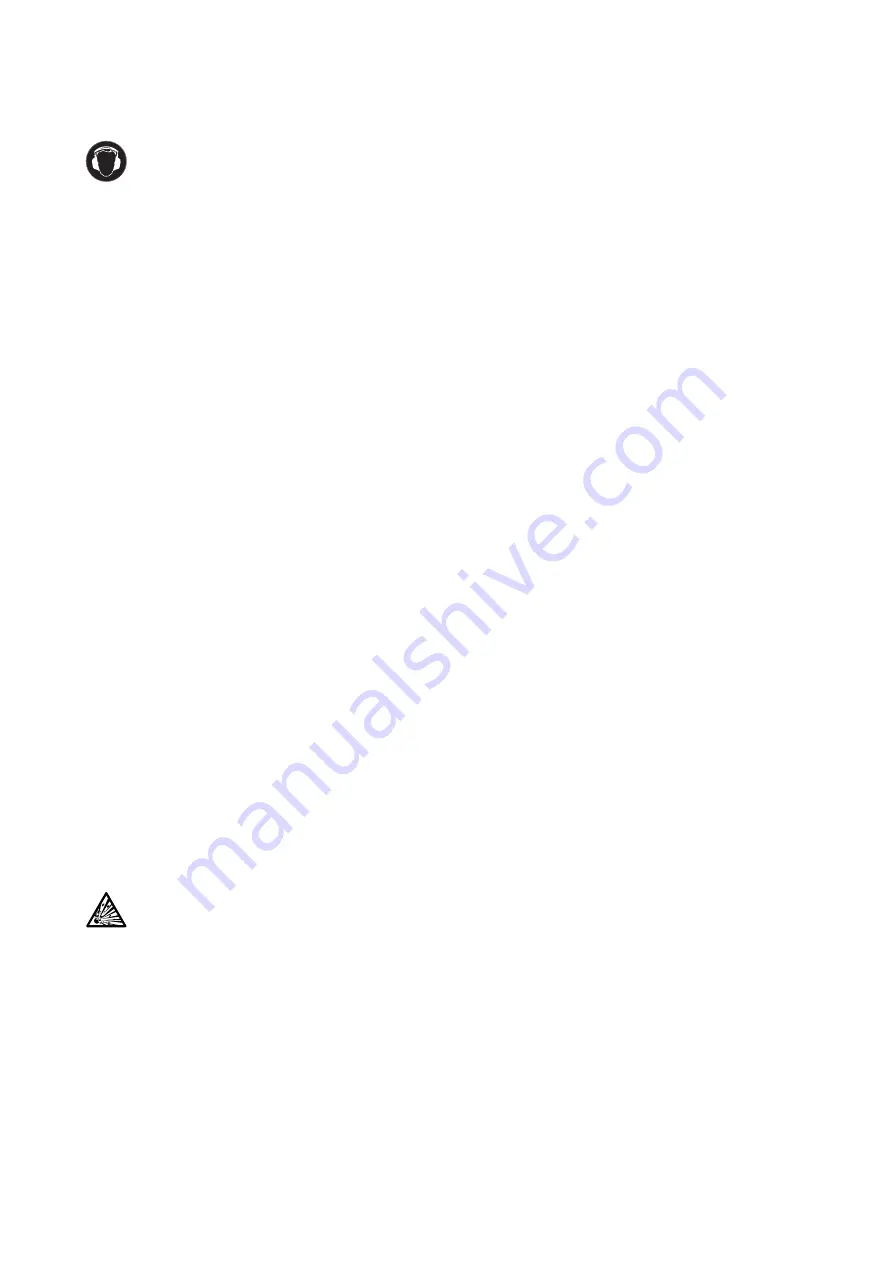
06 | ENGLISH
3. General description
3.1. Application
Pump is suitable for pumping drainage water, effluents
and surface water. The pumps are used for installations
in public and private sector, building trades, and industry.
The pumps can convey abrasive medium as surface wa-
ter. For highly abrasive content, such as concrete-gravel
and sand in the medium, it is necessary to protect the im-
peller and pump housing against excessive abrasion or to
shorten the maintenance interval. Before the pumping of
chemically aggressive liquids, the resistance of the pump
materials must be checked.
The pumps are available in high quality materials of all
components (Stainless steel).
The machine must be submerged in pumped liquid at
least up to the top edge of the motor housing.
The temperature of the pumped medium may be up to
104°F or up to 140°F for a short period. The maximum den-
sity of the medium is 0.03757 lbs/in³ and the pH may be
from 6 – 11.
Stainless steel variants can be used at a pH of 4 - 14.
However, the pH alone only serves as a guideline. Consult
factory for assistance with chemically aggressive liquids.
Depending on the composition, it may be necessary to
use special sealing materials.
3.2. Types of use
The motors are designed for continuous operation (S1),
maximum 15 starts per hour. The hydraulic is designed for
permanent operation, e.g. supply of industrial water.
the operator make additional measurements under all op-
erating conditions.
Caution: Wear ear protectors!
In accordance with the laws in effect, guidelines,
standards and regulations, ear protection must be
worn if the sound pressure is greater than 85 dB (A)!
The operator is responsible for ensuring that this is
observed!
Mise en garde : Portez des protecteurs auditifs !
Conformément aux lois en vigueur, aux directives,
aux normes et aux règlements, le port de protecteurs
d‘oreilles est obligatoire si la pression acoustique est
supérieure à 85 dB (A) ! L‘opérateur est responsable
du respect de cette consigne !
2.9. Pumped fluids
Each pumped fluid differs in regard to composition, cor-
rosiveness, abrasiveness, TS content and many other
aspects. Generally, our products can be used for many
applications. For more precise details, see chapter 3, the
machine data sheet and the order confirmation. It should
be remembered that if the density, viscosity or the general
composition change, this can also alter many parameters
of the product. Different materials and impeller shapes
are required for different pumped fluids. The more exact
your specifications on your order, the more exactly we can
modify our product to meet your requirements.
If the area of application and/or the pumped fluid change,
we will be happy to offer supportive advice.
When switching the product into another pumped fluid,
observe the following points:
• Products which have been operated in sewage or
waste water must be thoroughly cleaned with pure
water or drinking water before use.
• Products which have pumped fluids which are haz-
ardous to health must always be decontaminated be-
fore changing to a new fluid. Also clarify whether the
product may be used in a different pumped fluid.
• With products which have been operated with a
lubricant or cooling fluid (such as oil), this can escape
into the pumped fluid if the mechanical shaft seal is
defective.
Danger - explosive fluids!
It is absolutely prohibited to pump explosive liquids
(e.g. gasoline, kerosene, etc.). The products are not
designed for these liquids!
Danger - fluides explosifs !
Il est absolument interdit de pomper des liquides
explosifs (par exemple, de l‘essence, du kérosène,
etc.). Les produits ne sont pas conçus pour ces liq-
uides !
2.10. Danger due to spark generation
Mechanically generated sparks can ignite flammable gas-
es and condensates. According to EN1127-1 Para.6.4.4,
sparks must also be excluded for category 2 in normal
operation. In normal operation no spark generation is pos-
sible due to fluid covering (medium covering of the pump
hydraulic).
The ingress or suction of foreign bodies (stones, pieces
of metal, etc.) through the suction nozzles into the pump
hydraulic is not possible in an expected case of malfunc-
tion in which the enclosure fails as the pump cannot suck
up pumping medium nor its containing solids. In the ven-
tilated shaft, the explosion-protected submersible motor
pumps are drained via a drain system with two guide
tubes of galvanized steel, between their guide claws of
grey cast iron that guide into the automatic coupling ar-
rangement. The guide velocity, with max 0.1 m/s (10cm/s)
is so low that no sparks can be generated even in the
most disadvantaged conditions. In the first installation,
the guide claws of the drain arrangement should be lubri-
cated with ball bearing grease in order to suppress heat
and spark generation in the most disadvantaged case.