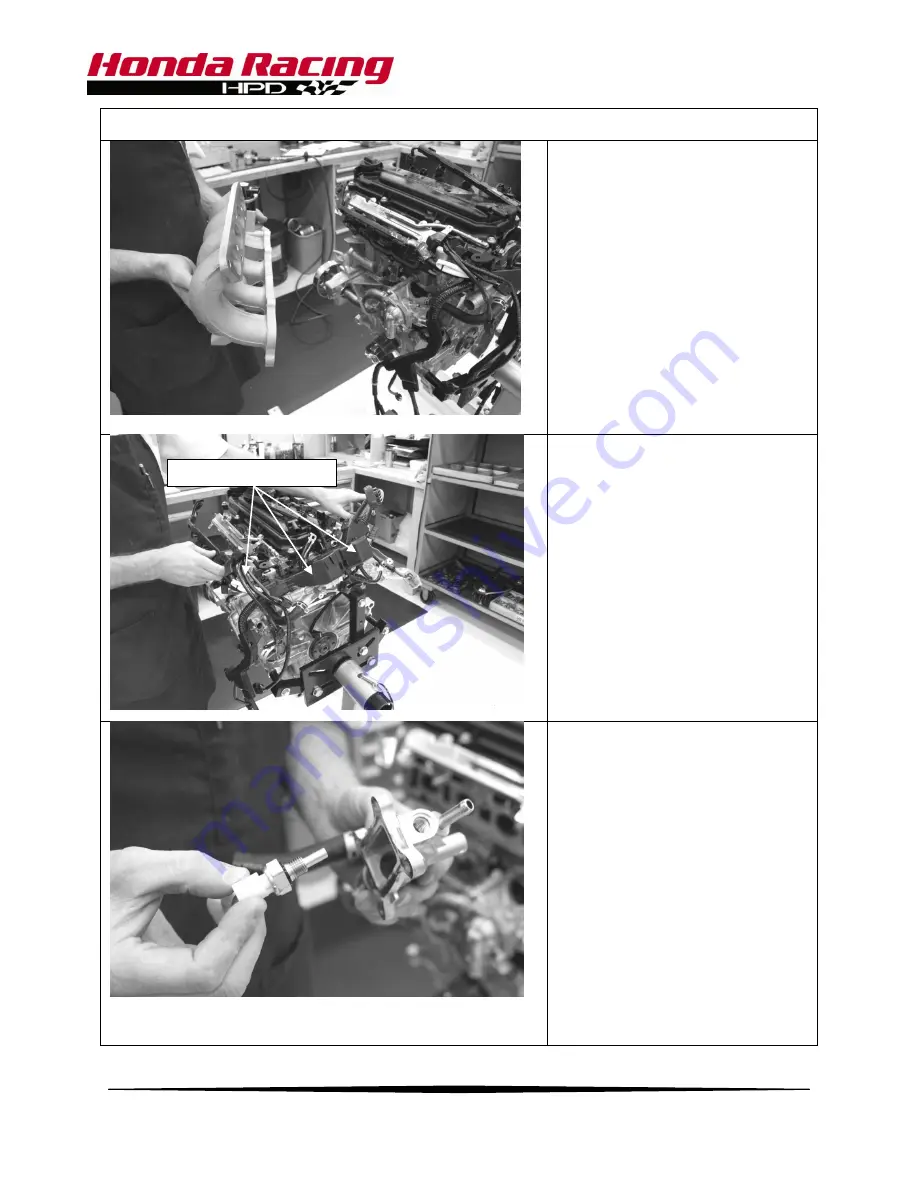
HPD L15A7 Engine Kit Assembly Manual
8
8/2012
Prepare The L15A7 Honda Engine For The Engine Kit Installation
Remove the intake runner. Save the
intake runner and gasket for reuse in
the HPD engine kit.
Remove the wiring harness and
bracket.
Remove the water outlet. Save the 4
x 16mm bolts for reuse in the HPD
engine kit.
Remove the water temperature
sensor and O-ring from the water
outlet housing. Save them for reuse in
the HPD engine kit.
Wiring Harness and Bracket
Summary of Contents for HPD L15A7
Page 1: ......