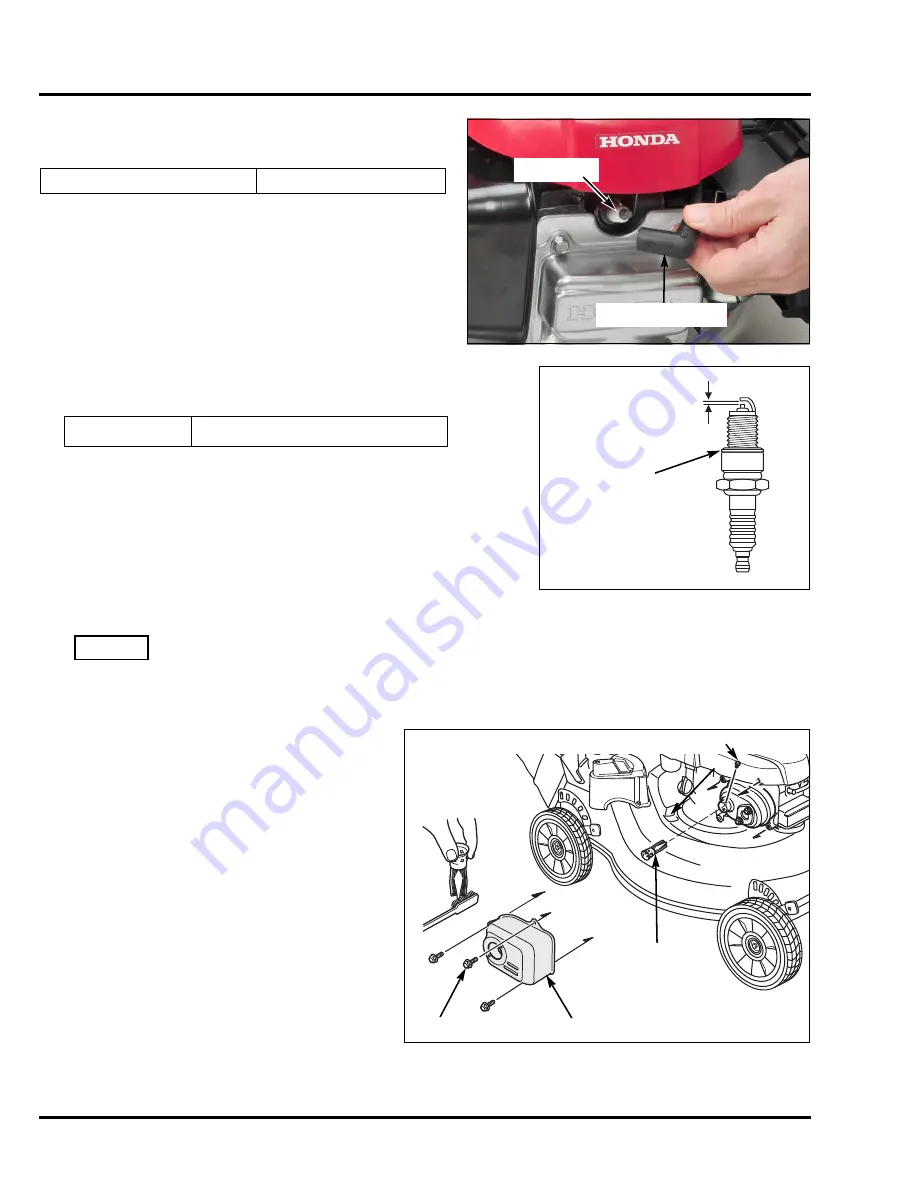
MAINTENANCE
HRR216PKA
3-8
9. SPARK PLUG INSPECTION
Using an incorrect spark plug can cause engine damage. Use
the recommended spark plug or an exact equivalent.
1. Remove the spark plug with a 13/16 in (21 mm) spark plug
wrench.
2. Visually inspect the spark plug. Discard the plug if the
insulator is cracked or chipped.
3. Measure the plug gap with a wire-type gauge. If
necessary, adjust the gap by bending the side electrode.
4. Make sure the sealing washer is in good condition and replace if
necessary.
5. Install the plug finger-tight to seat the washer, then tighten with a plug
wrench to compress the sealing washer:
Tighten a new plug 1/2 turn after the plug seats.
Tighten a reused plug 1/8 ~ 1/4 turn after the plug seats.
TORQUE:
20 N•m (14 ft-lb)
NOTICE
A loose spark plug can overheat and damage the engine. Overtightening can
damage the threads in the cylinder head.
10. SPARK ARRESTER
CLEANING
(OPTIONAL PART)
The spark arrester must be serviced every 100 hours
to keep it functioning as designed.
1. Remove the three flange bolts from the muffler
protector.
2. Remove the 4 x 6 mm self-tapping screw from
the spark arrester, and remove the spark
arrester from the muffler. Be careful not to
damage the spark arrester screen.
3. Check for carbon deposits around the exhaust
port and spark arrester. Clean with a wire brush,
if necessary. Replace the spark arrester if there
are any breaks or tears.
4. Install the spark arrester and muffler protector in the reverse order of disassembly.
Recommended spark plug
NGK BPR5ES
Spark plug gap
0.7 ~ 0.8 mm (0.028 ~ 0.031 in)
SPARK PLUG CAP
SPARK PLUG
0.028 ~ 0.031 in
(0.7 ~ 0.8 mm)
SEALING
WASHER
HO
SETSCREW
SPARK ARRESTER
FLANGE BOLT (3)
HEAT SHIELD
Summary of Contents for HRR216PKA
Page 5: ...iv HRR216PKA NOTES...
Page 9: ...SPECIFICATIONS HRR216PKA 1 4 NOTES...
Page 45: ...MUFFLER HRR216PKA 5 2 NOTES...
Page 49: ...RECOIL STARTER HRR216PKA 6 4 NOTES...