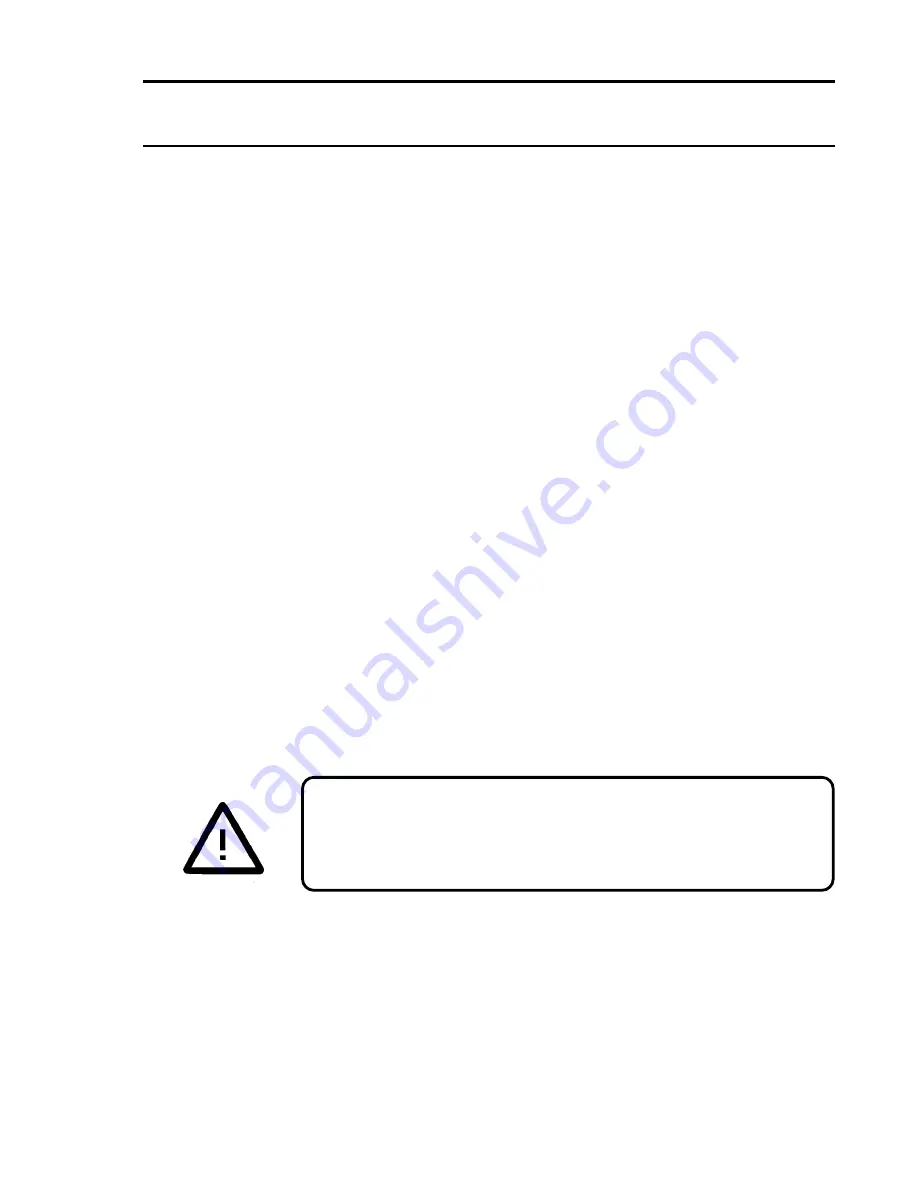
MAN0443.P65 Issue 13 Aug 04
5701 Control System
05701-M-5001 A02279
CHAPTER 4 - INSTALLATION INSTRUCTIONS
4 - 7
3.
LOCATION
The control system must be installed in a safe area such as a control
or equipment room, away from sources of heat, with adequate
ventilation and protected from the weather.
There are two different System 57 rack configurations to accommodate
either front or rear field wiring entry. Each configuration is available in
half or full 19" width. The three most common mounting methods are:
a.
19" Mounting Frame
The System 57 19" 6U front and 3U rear access racks are compatible
with the standard 19" (483mm) sub-rack format and may therefore
be fitted into any suitable 19" mounting frame.
b.
Cabinet
Wall mounting cabinets are available in two sizes to accommodate
the 19" and half 19" 6U front access rack assemblies.
c.
Panel
Alternatively all the racks are suitable for fitting directly into a panel
cutout aperture.
Power supply units are available, in both 19" and half 19" 1U formats,
for applications where an ac input power source is to be used. It is
recommended that the power supply units are mounted directly above
the System 57 rack.
CAUTION
3U rear access racks should always be supported at the rear of
the unit to prevent distortion and excessive loading of the front
flange plates.