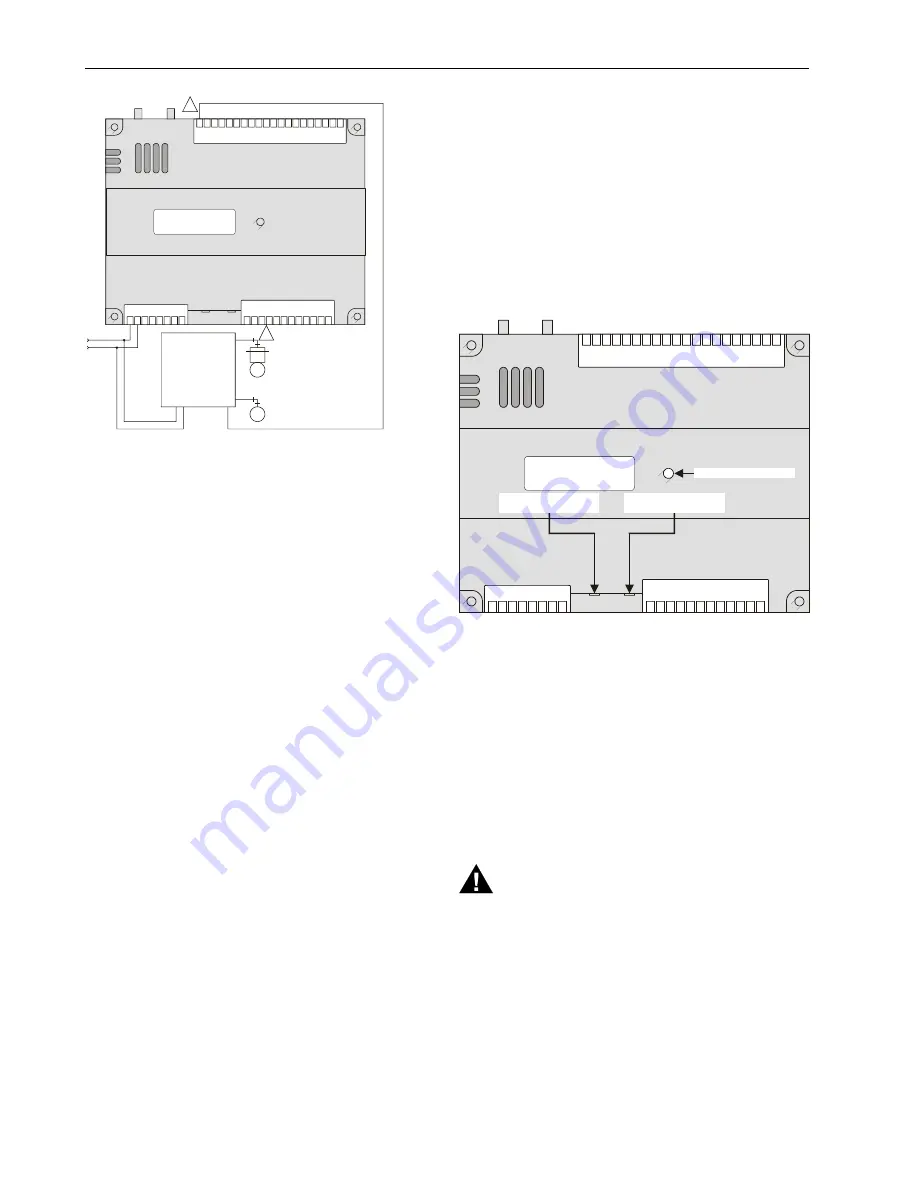
LYNX LON PROGRAMMABLE, VAV/UNITARY CONTROLLERS – PRODUCT DATA
EN0Z-0957GE51 R0615
14
1 2 3 4 5 6 7 8 9 0 1 2 3 4 5 6 7 8 9 0
2 2 2 2 2 2 2 2 2 2 3 3 3 3 3 3 3 3 3 4
1 2 3 4 5 6 7 8
1
1 1 1 1 1 1 1 1 1 2
1
2 3 4 5 6 7 8 9 0
0
9
CLLYUL6438S
24 V
A
C
24 V
AC COM
E GN
D
SH
L
D
SB
U
S
1
SB
U
S
2
NE
T-
1
NE
T-
2
DO
-1
DO
-2
CO
M
CO
M
CO
M
CO
M
DO
-3
DO
-4
DO
-5
DO
-6
DO
-7
DO
-8
AO
-1
AO
-2
AO
-3
DI
-1
DI
-2
DI-3 DI
-4
20VD
C
UI
-1
UI
-2
UI-3
UI
-4
UI
-5
UI
-6
CO
M
CO
M
CO
M
CO
M
CO
M
CO
M
24VAC
24VAC
COM
RP7517B
PNEUMATIC
VALVE
ACTUATOR
BROWN
BLACK
BLUE
2B
1M
2
M
1
Fig. 21. Controller wiring diagram (CLLYUL6438S shown)
for RP7517B pneumatic transducer
NOTE 1:
Use 6 mm tubing. Minimum branch line must be
1.8 m or longer.
NOTE 2:
Terminals 21, 23, and 24 are analog outputs.
CHECKOUT
Step 1. Check Installation and Wiring
Inspect all wiring connections at the controller terminals, and
verify compliance with installation wiring diagrams. If any
wiring changes are required,
first
be sure to remove power
from the controller
before
starting work. Pay particular
attention to:
24 VAC power connections. Verify that multiple controllers
being powered by the same transformer are wired with the
transformer secondary connected to the same input
terminal numbers on each controller. Use a meter to
measure 24 VAC at the appropriate terminals (see Fig.
11). Controller configurations are not necessarily limited to
three devices, but the total power draw, including
accessories, cannot exceed 100 VA when powered by the
same transformer (U.S., only).
Ensure that each controller has terminal 3 wired to a
verified earth ground, using a wire run as short as possible
with the heaviest gauge wire available, up to 2.0 mm
2
with
a min. of 1.0 mm
2
for each controller in the group (see Fig.
11).
Verify that triac wiring of the digital outputs to external
devices uses the proper load power and 24 VAC common
terminal (digital output common terminals) for high-side
switching.
NOTE:
All wiring must comply with applicable electrical
codes and ordinances or as specified on
installation wiring diagrams.
For guidelines for wiring run lengths and power budget, see
section “Power” on page 6.
Verify Termination Module Placement (Multiple Controllers,
Only)
The installation wiring diagrams should indicate the locations
for 209541B termination module(s). See Fig. 12 and refer to
Excel 50/500/800 L
ON
W
ORKS
® Mechanisms (EN0B-
0270GE51).
Correct placement of the end-of-line termination resistors is
required for proper L
ON
W
ORKS
® Bus communications.
Step 2. Startup
See Fig. 22 and the following text for startup information.
1 2 3 4 5 6 7 8 9 0 1 2 3 4 5 6 7 8 9 0
2 2 2 2 2 2 2 2 2 2 3 3 3 3 3 3 3 3 3 4
1 2 3 4 5 6 7 8
1
1 1 1 1 1 1 1 1 1 2
1
2 3 4 5 6 7 8 9 0
0
9
CLLYVL6438NS
24 V
A
C
24 V
AC CO
M
E GND SHLD SBU
S
1
SBU
S
2
NET
-1
NET
-2
DO
-1
DO
-2
CO
M
CO
M
CO
M
CO
M
DO
-3
DO
-4
DO
-5
DO
-6
DO
-7
DO
-8
AO
-1
AO-
2
AO
-3
DI
-1
DI-
2
DI
-3
DI-
4
20VD
C
UI
-1
UI-
2
UI
-3
UI-
4
UI-
5
UI
-6
CO
M
CO
M
CO
M
CO
M
CO
M
CO
M
TERMINALS 21-40
TERMINALS 9-20
TERMINALS 1-8
LonWorks Bus Jack
(labelled SRV JCK)
Neuron Service Pin
(labelled SRV PIN)
HOST STATUS LED
Fig. 22. LED, service, network, and terminal connections
Broadcast the Service Message
The Service Message allows a device on the L
ON
W
ORKS
®
Bus to be positively identified. The Service Message contains
the controller's N
EURON
® ID number and node type. This is
used to confirm the physical location of a particular LYNX
L
ON
W
ORKS
® device in a building.
To send the Service Message from the controller, press the
N
EURON
® Service Pin pushbutton on the controller (see Fig.
22). When pressed, this button sends out the Service
Message, regardless of the controller's current mode of
operation.
CAUTION
Electrical Damage Hazard.
Can cause controller damage or failure.
Do not use any metal object to press the N
EURON
®
Service Pin. Use, instead, a plastic rod or wooden
implement (such as a pencil with the lead broken off)
to press the pin. Using a metal object can damage the
controller's circuitry.
Controller Status LED