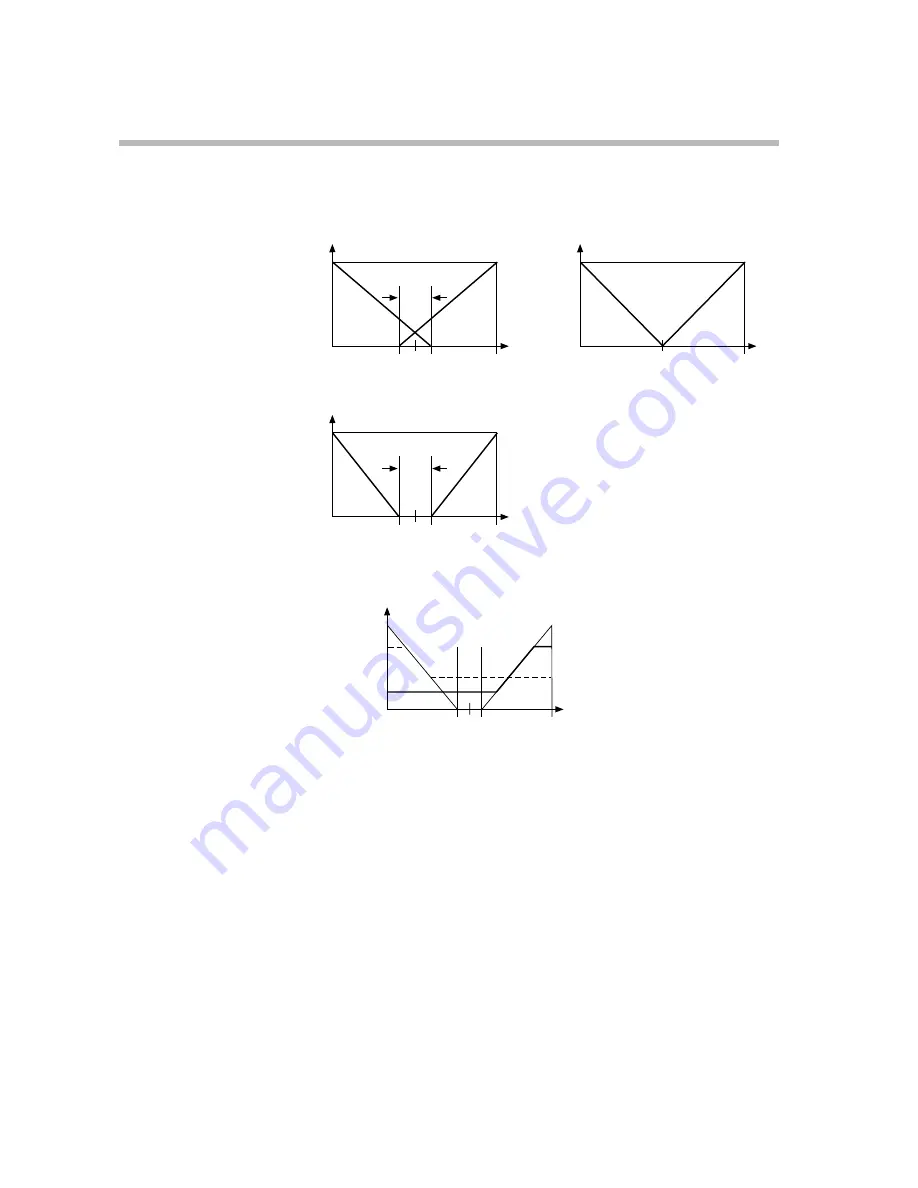
Chapter 7. PARAMETER SETUP
7-14
Dead
zone
Output
(heat)
Output
(cool)
MV
100%
50%
0%
100%
Control output
values
Dead zone<0
Dead
zone
Output
(heat)
Output
(cool)
MV
100%
50%
0%
100%
Dead zone>0
Output
(heat)
Output
(cool)
MV
100%
50%
0%
100%
Dead zone=0
Heat-side
output
Cool-side
output
MV
100%
50%
0%
100%
Cool-side
OH
Heat-side
OL
Heat-side
OH
Cool-side
OL
Note 1)
On heat/cool models, this sets how the relationship between heat-side output
and cool-side output should be processed with respect to the MV resulting from
PID operation.
Note 2)
Constants
OL
and
OH
function as follows:
Note 3)
When MV
≥
50%, the heat-side PID set is switched to.
When MV < 50%, the cool-side PID set is switched to.
Note 4)
PID set selection is carried out by setting value and external switch.