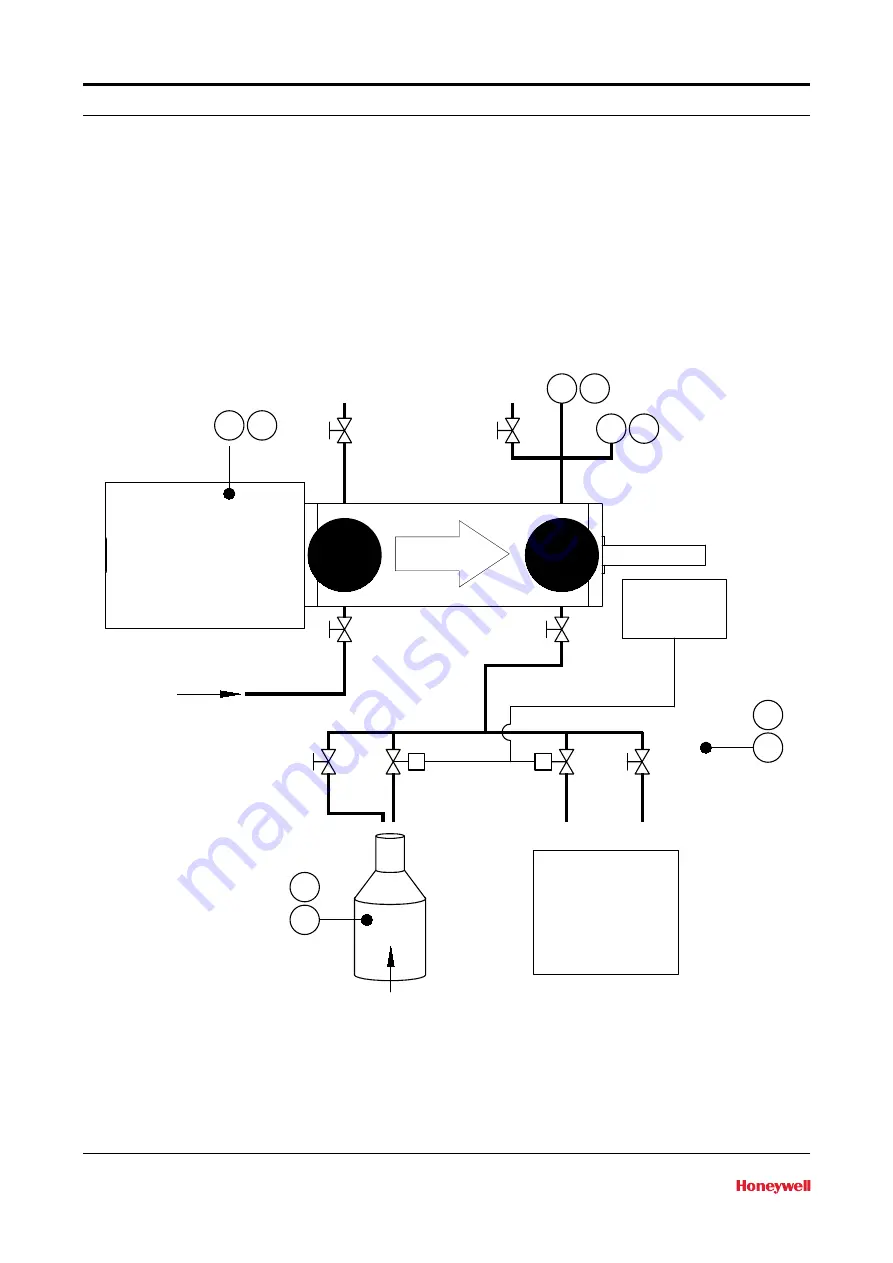
Calibration
4-10
SVP Controller Operation Manual
Part No.: 44200004 - Revision 2
In calibration mode alarms will be generated as per the configuration, and
the run permissive signal from the flow computer or the run prover test
signal will be ignored. The operating mode of the prover will be saved in
NVM so that the mode will be restored if power is turned off while in Prover
Calibration mode.
To exit calibration mode navigate to the Exit Calibration Mode menu and
press OK.
A copy of Table 1 can be used to enter water draw data.
V2
V3
T1
P1
VENT
VENT
V6
SV1
SV2
V5
WATER
SUPPLY
S
S
Tp
Pp
T2
WASTEWATER
CATCH
CONTAINER
FLOW
TEST MEASURE
SVP
CONTROLLER
Td
V4
V1
T3
Ttm
T4
Ta
Figure 4-7:
Water Draw Plumbing Diagram