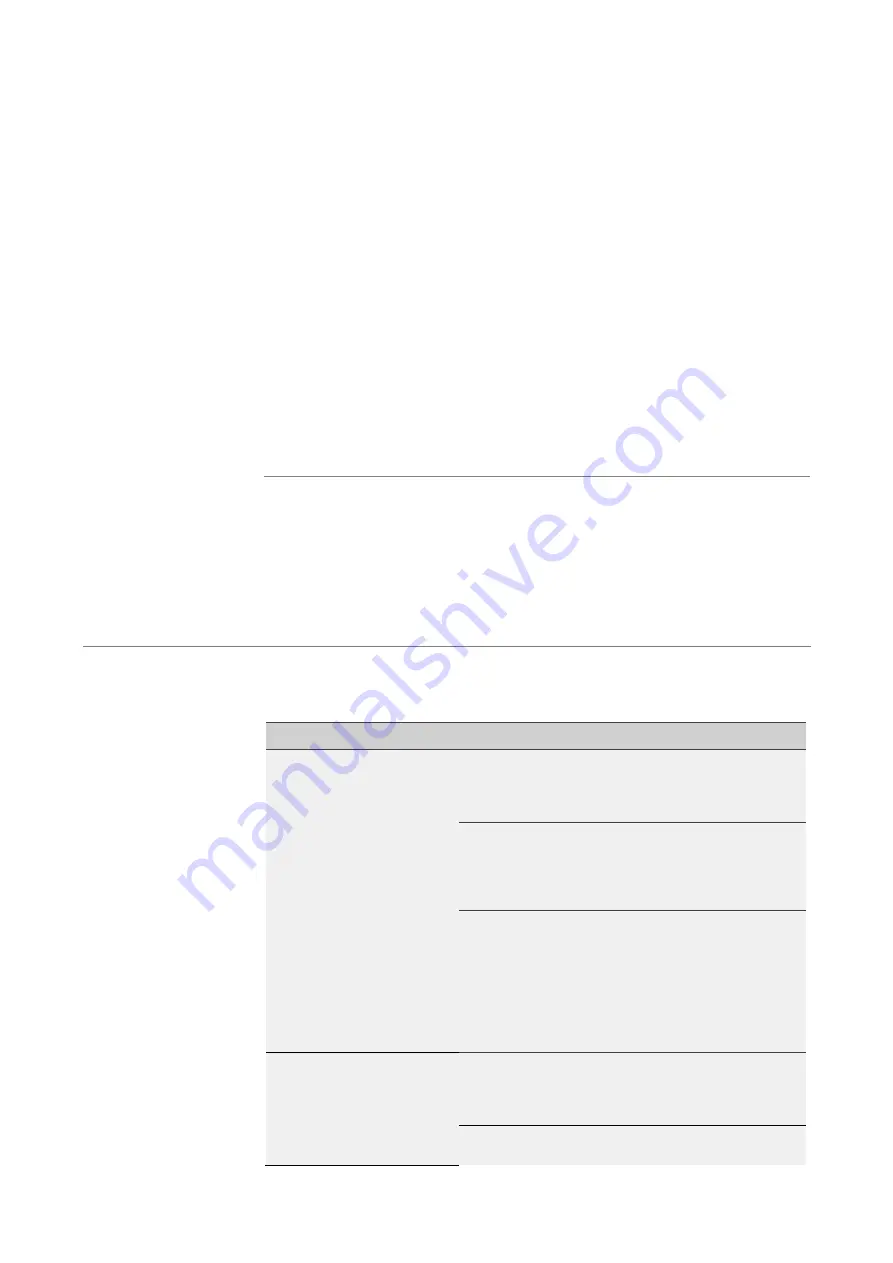
Maintenance
HON 670 / HON 671 Controllers Component Documentation
17
4
Maintenance
Topic
Page
Removing the pressure unit from the controller
Maintenance on the controller with diaphragm measuring unit
Maintenance on the controller with metal bellows measuring unit
Maintenance on the pressure unit
Mounting the pressure unit on the controller
4.1
Maintenance schedule
The maintenance schedule provides an overview of the periodically required maintenance.
Since the maintenance intervals are highly dependent on the operating conditions and the
gas quality, it is impossible to provide set maintenance intervals. It is recommended to use
maintenance intervals conforming to the specifications in DVGW Code of Practice G
495. In
addition, the need for maintenance must be determined and documented on the basis of
operational requirements and experience.
Maintenance must be carried out in compliance with all federal and state laws and regula-
tions, as well as with the local rules and regulations set forth by the relevant utilities and
authorities and any other applicable regulations.
4.2
Preparing for the maintenance
Proceed as follows:
Step
Description
Explanation
1
Have the maintenance
and servicing parts
ready
Refer to the topic
Explanation of spare parts
to find out which
spare parts drawings belong to your device model and have the
corresponding maintenance and service parts ready before
starting maintenance.
▪
The spare
parts that are always required for the controller’s
maintenance are listed in the spare parts kits for the control-
ler.
▪
Spare part drawings and spare parts lists are listed in the
appendix
(see page 41).
In addition to these maintenance parts, there are also servicing
parts that need to be checked during maintenance in order to
make sure that they are in working condition. Depending on
their condition, these must be replaced as needed.
Consequently, it is recommended that the required servicing
parts be kept on hand as per the section
Servicing parts for
controllers
in the topic
Maintenance and servicing parts for HON
670_671
to prevent downtimes.
2
Preparing special tools
In addition to standard tools, have the special tools required for
your specific controller model ready to go before maintenance.
Please refer to the
Special tools
section in
Lubricants, thread-
lockers, and special tools
(see page 65).
You will also need a magnetic bowl for the maintenance of your
controller to enable removal of the balls of the guide sleeve.
Contents
Meaning
Maintenance schedule
Preparation work for
controller maintenance