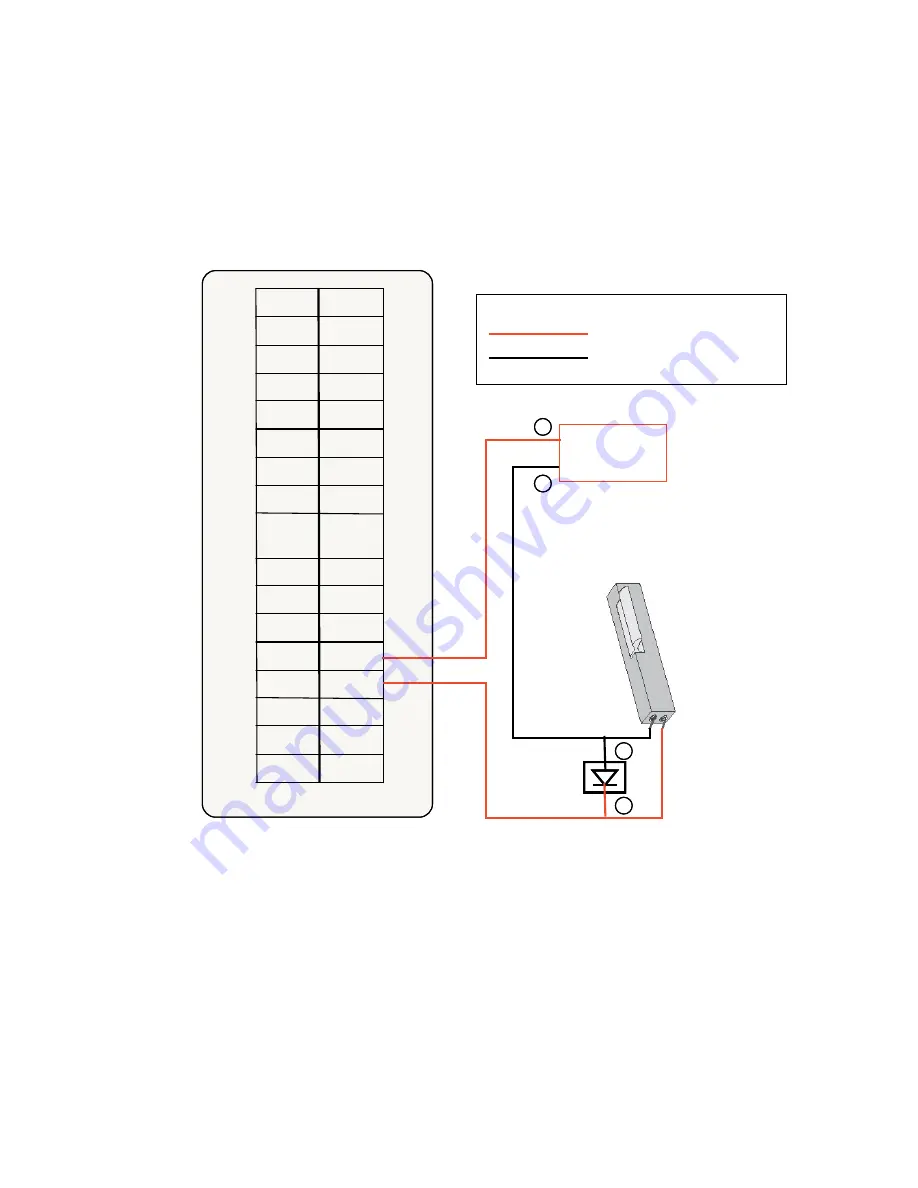
HONEYWELL IDENTIPOINT™ INTELLIGENT SMARTCARD SYSTEM
33
95-7767
1.
Connect 12VDC+ of the power supply to pin 5 (Relay-
NO) or pin 3 (Relay-C) of the reader and 12VDC- to the
-ve pin of the strike latch.
2.
Connect either pin 5 (Relay-NO) pin 3 (Relay-C), which-
ever is left free, of the reader to the +ve pin of the strike
latch.
In this setup, the door will remain locked in the absence of
power and will be unlocked when power is provided. If the
reader is powered off in this situation, the door will remain
locked.
NOTE:
The above describes one way of wiring the strike
latch. Wiring must be done strictly as per the
stipulated safety codes that the building must
follow. Accordingly, the wiring would be either
done in a fail-safe or fail-secure configuration.
For description of reader pins refer to Table.5 and Table.6.
Strike latch connected to the IOM:
Fig. 26. Connections between IOM and strike latch
1.
Connect 12VDC+ of the power supply to either the NO
or Common pin of Relay 0 or 1 (J12 or J13) of the IOM,
and the 12VDC- to the -ve pin of the strike latch.
2.
In the same port (J12 or J13), connect the NO or Com-
mon, whichever is left free, to the +ve pin of the strike
latch.
In this setup, the door will remain locked in the absence of
power and will be unlocked when power is provided. If the
reader is powered off in this situation, the door will remain
locked.
NOTE:
The above describes one way of wiring the strike
latch. Wiring must be done strictly as per the
stipulated safety codes that the building must
follow. Accordingly, the wiring would be either
done in a fail-safe or fail-secure configuration.
For description of IOM pins refer to Table.8.
Power – Min. 18 AWG
Power Gnd – Min. 18 AWG
LEGEND
RL1-C
N.O
GND
N.C
12V
RLO-C
GND
N.O
SAO
N.C
GND
485-A
SAI-3
485-B
GND
485-
GND
SAI-2
ILK-1
GND
GND
SAI-1
ILK-0
GND
GND
SAI-0
DO-1
GND
GND
DI-1
DO-0
GND
GND
DI-0
IO module
Strike Latch
DC – Power
12VDC/24VDC
FGND
+
+
_
_
RED
BLK
_
_
+
+
1457020-001
Diode Suppression
Network