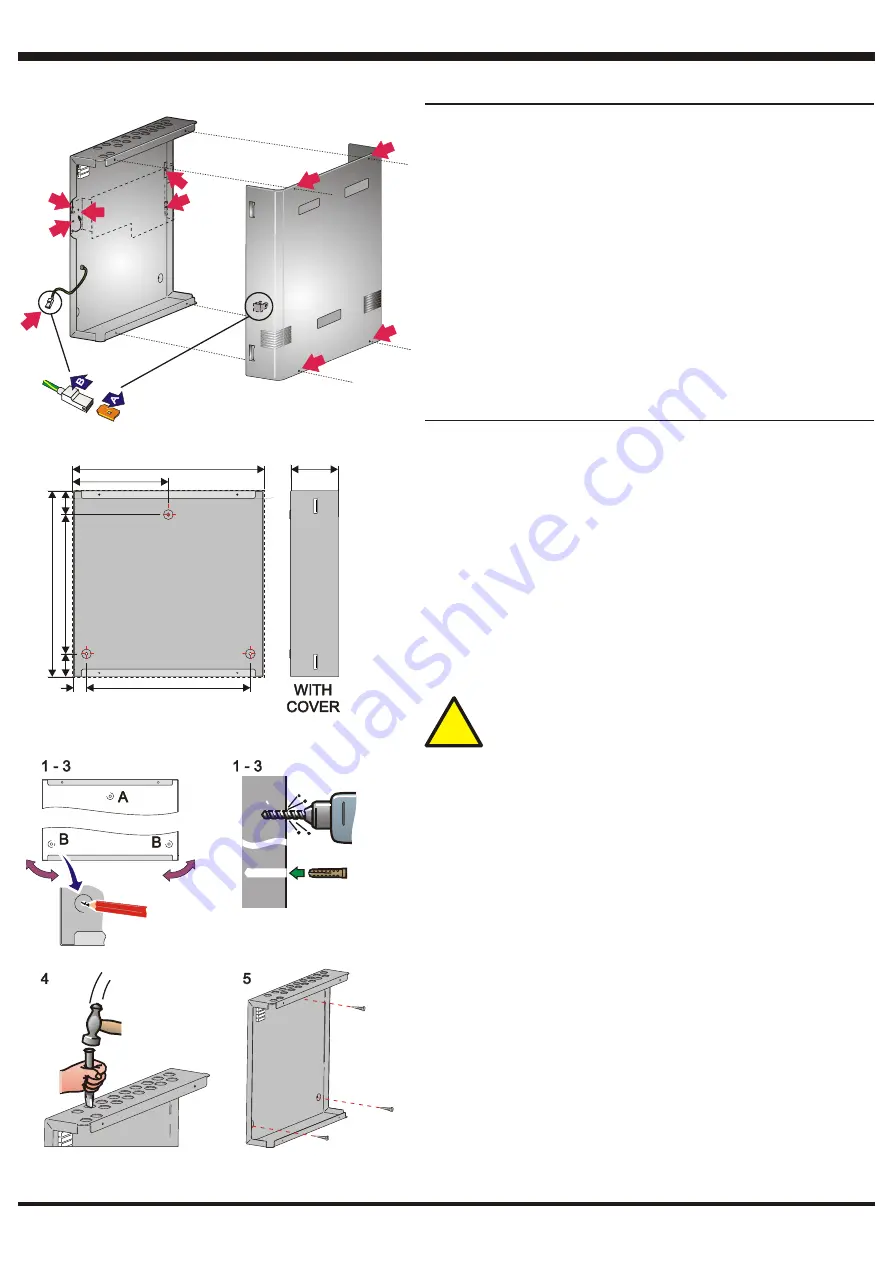
Installing the Network Gateway Unit
(Continued)
2
Preparing the Back Box
1
Remove and retain the four screws that secure the front cover. Disconnect
the cover earth lead from the blade on the cover. Place the cover in a
protective bag and store safely.
2
At the back box, disconnect the chassis earth lead from the blade terminal.
3
Remove and retain the 4 nuts and washers that secure the chassis to the
back box, and remove the chassis together with the electronics mounted
on it. Place in anti-static bag and store safely.
1
Remove and retain the four screws that secure the front cover. Disconnect
the cover earth lead from the blade on the cover. Place the cover in a
protective bag and store safely.
2
At the back box, disconnect the chassis earth lead from the blade terminal.
3
Remove and retain the 4 nuts and washers that secure the chassis to the
back box, and remove the chassis together with the electronics mounted
on it. Place in anti-static bag and store safely.
Note:
All blade connections to earth incorporate a locking barb. To make a
connection push the shrouded receptacle on to the earth blade (A). To
remove this connection, pull the shroud (B), NOT the earth wire.
Note:
All blade connections to earth incorporate a locking barb. To make a
connection push the shrouded receptacle on to the earth blade (A). To
remove this connection, pull the shroud (B), NOT the earth wire.
FOR CLARITY, INTERNAL EQUIPMENT IS NOT
SHOWN.
FOR CLARITY, INTERNAL EQUIPMENT IS NOT
SHOWN.
Fitting the Back Box to the Wall
1
Using a suitable-sized drilling bit - for holes to take up to 6mm (No. 12-
sized) wood screws - drill a hole at position A in the wall. Fit a suitable-
sized wall-plug, or equivalent.
2
Hold the back box in position at hole A (ensure the panel is level) and mark
the position of the remaining fixing holes (B). Remove the back box and
store safely.
3
Drill two holes at positions B in the wall, and fit suitable-sized wall-plugs, or
equivalent.
4
Prepare apertures (20mm knockouts) required for cable access. Make
sure paint is scraped from the area surrounding the knockouts, to ensure
good earthing for glands, or use earth termination kit 020-453 (see
previous page for mounting position). Use the 2 top front knockouts for
fibre-optic cables.
5
Secure the back box to the wall using all three fixing holes and
appropriate-sized screws (up to 6mm [No. 12-sized] round or pan-head
screws - do
not
use countersunk screws).
6
If a PSU3A is to be fitted, follow the procedure given on the next page.
7
Reverse the ‘Preparing the Back Box’ procedure to refit all items except
the cover.
Ensure chassis earth connections are made correctly.
8
If an RS232 or Fibre-optic PCB is to be fitted, follow the appropriate ‘Fitting
Optional PCBs’ procedure given on following pages.
9
Refit the cover (
ensure earth lead is connected
).
1
Using a suitable-sized drilling bit - for holes to take up to 6mm (No. 12-
sized) wood screws - drill a hole at position A in the wall. Fit a suitable-
sized wall-plug, or equivalent.
2
Hold the back box in position at hole A (ensure the panel is level) and mark
the position of the remaining fixing holes (B). Remove the back box and
store safely.
3
Drill two holes at positions B in the wall, and fit suitable-sized wall-plugs, or
equivalent.
4
Prepare apertures (20mm knockouts) required for cable access. Make
sure paint is scraped from the area surrounding the knockouts, to ensure
good earthing for glands, or use earth termination kit 020-453 (see
previous page for mounting position). Use the 2 top front knockouts for
fibre-optic cables.
5
Secure the back box to the wall using all three fixing holes and
appropriate-sized screws (up to 6mm [No. 12-sized] round or pan-head
screws - do
not
use countersunk screws).
6
If a PSU3A is to be fitted, follow the procedure given on the next page.
7
Reverse the ‘Preparing the Back Box’ procedure to refit all items except
the cover.
Ensure chassis earth connections are made correctly.
8
If an RS232 or Fibre-optic PCB is to be fitted, follow the appropriate ‘Fitting
Optional PCBs’ procedure given on following pages.
9
Refit the cover (
ensure earth lead is connected
).
Wall Flatness
To prevent distortion, the back box MUST be installed on the wall as flat as
possible, i.e. with a maximum flatness deviation between any two points of
3mm. Where the wall is out of tolerance, use appropriate packing pieces when
installing the back box to meet the above requirements.
Failure to comply with this requirement will result in the misalignment of
the cover’s securing screws, which may cause difficulties in fitting the
cover.
All dimensions are in millimeters. Fixing hole diameters are 6mm.
Procedure
When a suitable location has been found for installing the back box, and the
Network Gateway Module electronics have been removed, fix the back box to
the wall as follows:
Wall Flatness
Failure to comply with this requirement will result in the misalignment of
the cover’s securing screws, which may cause difficulties in fitting the
cover.
Procedure
To prevent distortion, the back box MUST be installed on the wall as flat as
possible, i.e. with a maximum flatness deviation between any two points of
3mm. Where the wall is out of tolerance, use appropriate packing pieces when
installing the back box to meet the above requirements.
All dimensions are in millimeters. Fixing hole diameters are 6mm.
When a suitable location has been found for installing the back box, and the
Network Gateway Module electronics have been removed, fix the back box to
the wall as follows:
105.00
DO NOT use the back box as a guide when drilling.
DO NOT use the back box as a guide when drilling.
!!
37.50
301.00
380.00
4
5
.0
0
3
6
5
.0
0
2
7
5
.0
0
190.00
4
5
.0
0
3
3
3
3
3
3
3
3
1
1
1
1
1
1
1
1
1
1
2
2
997-451, Issue 6 July 2006