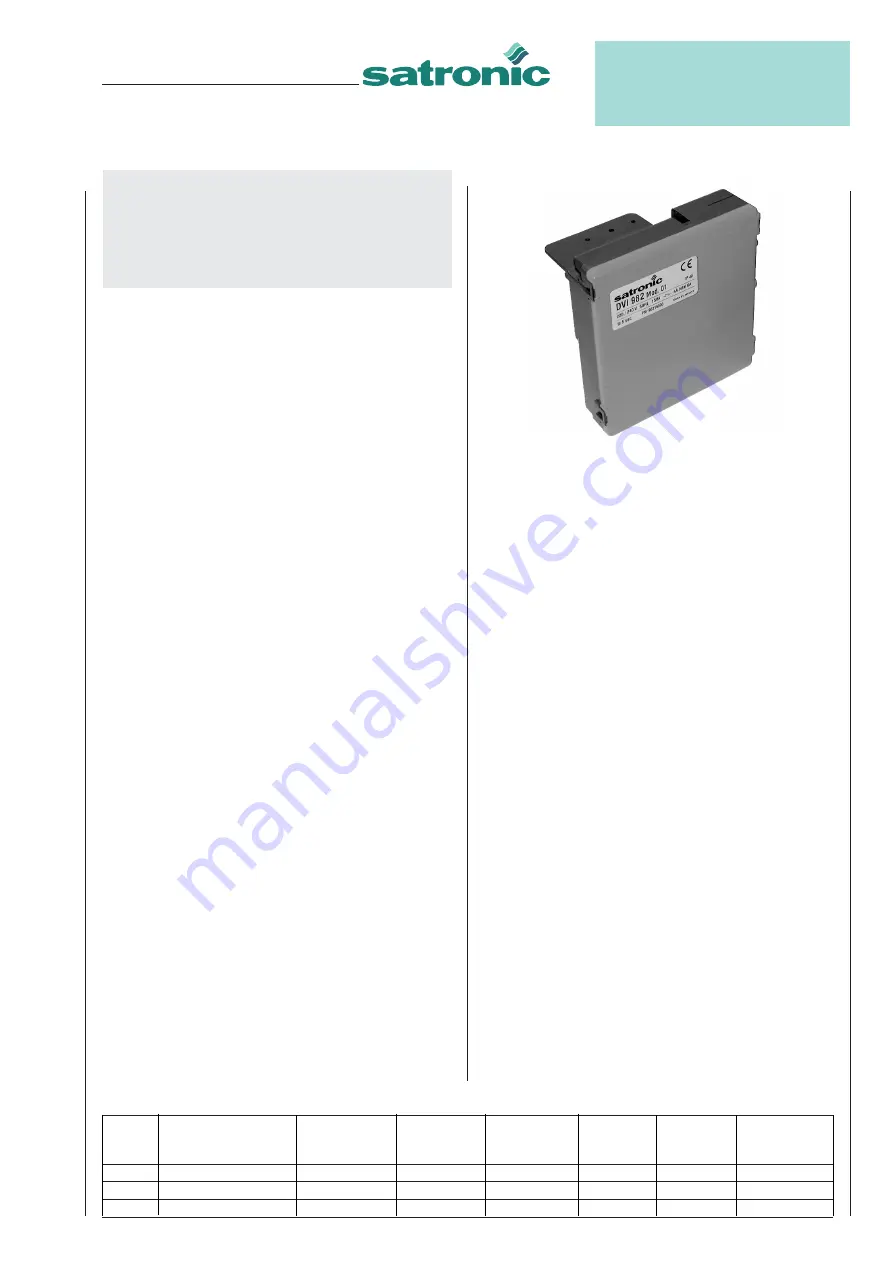
1
A Honeywell Company
INTRODUCTION
The burner control boxes DVI980/982 controls and
supervises forced draught and atmospheric gasburners.
They are approved and certified according to the applicable
European standards and regulations. The use on direct air
heaters according DIN 4794 is also possible.
The microprocessor-based programming sequence ensures
extremely stable timings independent of voltage variations,
ambient temperature and/or switch-on cycles. The built-in
information system not only provides a continuous
monitoring of the actual state of the box (very helpful
especially for monitoring the start-up phase) but also informs
about the cause of a possible lock out. The lock out cause
is stored in such a way that it can be retrieved even after a
power failure. The control box is designed for maximum
safety in case of fluctuations in the voltage supply. If the
mains voltage drops below the permitted level, operation is
interrupted and the control box automatically prevents the
start sequence from being repeated. In this way, the safety
of the system is not put at risk by a drop in the mains voltage.
This low-voltage protection works not only during start-up
but also permanently during operation.
CONSTRUCTION FEATURES
Microprocessor, electronic components, output relais,
ignition spark generator and flame amplifier are placed on
the printed circuit board.
These plus the optional lockout- and reset circuit are well
protected inside a flame resistant plastic housing.
The LED for displaying the information system are placed
on top of the housing.
TYPES AVAILABLE
DVI 980
1-stage
DVI 982
2-stage
MODELS
The following functions can be configured by factory:
•
with or without air proving switch
•
IR-data transmission over Palm Pilot, PC or hand-held
•
volatile or non volatile lock out
•
recycling (numbers eligible) or lock out / blocked after
loss-of-flame during operation
•
recycling (numbers eligible) or lock out / blocked without
flame establishment after safety time
•
with or without internal reset button
•
potential free output for flame signal
•
with or without lock out lamp (LED)
DVI 980/982
(Honeywell Nr. S4865)
Gas Burner Safety Control
For 1- or 2-stage forced draught and
atmospheric gas burners, with DC valves
Possible flame detectors:
- Ionisation probe
- Infrared flicker detector 1020.1
- UV flame sensor UVD 971
TECHNICAL DATA
Operating voltage
220 / 240 V (-15... +10%)
50/60 Hz (±5%)
Fuse rating
10 A fast, 6 A slow
Power consumption
ca. 12 VA
Max. load per output
- term. X2/6 motor
2.0 A, cos
ϕ
0.4
Variation A
- term. X3 ,X5, X6 solenoid valves
90mA, DC
Variation B
- term. X3, X9, X5, X6 solenoid valves 90mA, DC
only DC-valves can be connected!
- term. X2/8 lock out
1.0 A, cos
ϕ
0.4
total load
max. 6 A during 0,5 sec
Air proving switch
1 working contact
STB Safety temperature delimiter
1 working contact
Ignition spark generator
Ignition frequency
up to 40 Hz
Energy ignition spark
10 µAs
Ignition voltage
20 kV
Sensitivity (operation)
1
µ
A
Min. required ion. current
1.5
µ
A
Sensitivity for stray light
0.4
µ
A
Flame signal output
Optocoupler
max 70V DC/100mA
Ionisation probe insulation
Probe - earth
greater than 50 M
Ω
Stray capacity
Probe - earth
less than 1000 pF
Cable length
< 3 m
Flame detectors
IRD 1020.1
end-on viewing
UVD 971
end-on viewing
Weight incl. Wiring base
190 g
Mounting position
any
Protection class
IP 40
Approved ambient parameter
- for operation
-20° C... +60° C
- for storage
-20° C... +80° C
Build-up of ice, penetration of water and condensing water
are inadmissible
Approvals according
to European standard
EN 298, as well as all other
relevant Directives and
standards
Model
max. reaction time or
supervised
pre-ignition
ignition time
stray light
safety time
delay 2nd stage
air proving switch
pre-purge time
time
total
monitoring
(DVI 982)
tlw
tv1
tvz
tz
tf
ts
tv2
01
60
24
0
4
5
5
10
02
60
10
0
4
5
5
–
05
60
30
0
4
5
5
–
Table of timings (sec.)
EN1C-0121SZ20 R0305