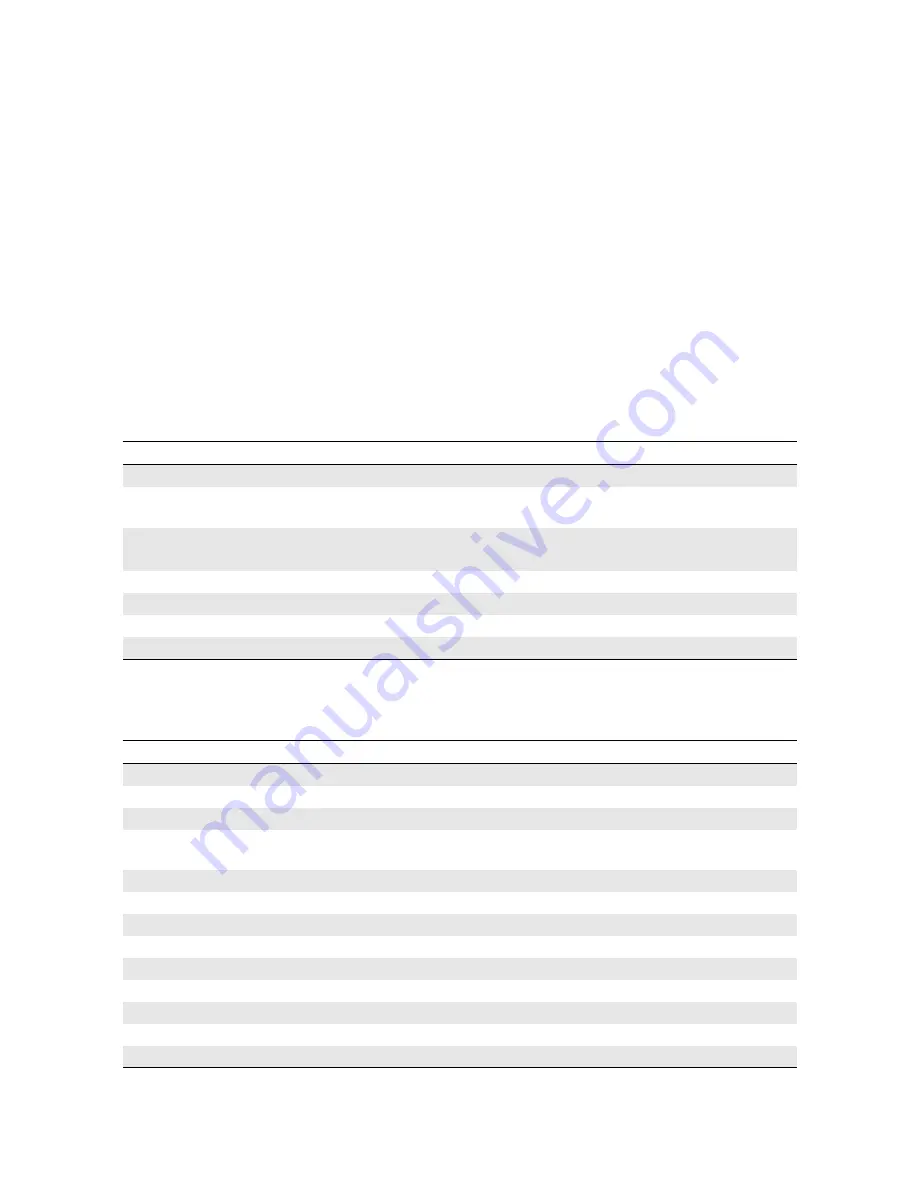
Appendix
B
Troubleshooting
B.1 Warning
Description
Troubleshooting
Warning 1 Calibration Overdue
Calibrate the unit
Warning 3 BLE failure (BLE version only)
Power-cycle the unit. If same warning occurs again, contact
manufacturer
Warning 4 Time/date not set (RTC not set) / RTC reset
abnormally
Configure unit time. If same warning occurs again, contact
manufacturer
Warning 5 Log memory corrupted (CRC not matched)
Power-cycle the unit. Event log might be lost.
Warning 6 Certificate is corrupted or missing certificate
Contact manufacturer
Warning 7 Over-range warning
Calibrate the unit.
Warning 8 Under-range warning
Calibrate the unit.
B.2 Fault
Description
Troubleshooting
Fault 1 Internal communication failure
Power-cycle the unit. If same fault occurs again, contact manufacturer
Fault 2 Cell failure
Check the sensor connection. If same fault occurs again, replace sensor
Fault 3 Cell is producing a negative reading
Calibrate the unit
Fault 4 EEPROM is corrupted
Reconfigure the unit by using mobile app. If same fault occurs again,
contact manufacturer
Fault 5 MCU operating voltage failure
Power-cycle the unit. If same fault occurs again, contact manufacturer
Fault 6 RAM read/write fault
Power-cycle the unit. If same fault occurs again, contact manufacturer
Fault 7 Flash memory corrupted
Reconfigure the unit by using mobile app
Fault 8 Code memory failure
Power-cycle the unit. If same fault occurs again, contact manufacturer
Fault 9 mA output failure (mA output version only)
Check whether loopback resistor is connected correctly
Fault 10 Supplied voltage failure
Power-cycle the unit. If same fault occurs again, contact manufacturer
Fault 11 Internal HW Fault
Power-cycle the unit. If same fault occurs again, contact manufacturer
Fault 12 Internal SW Fault
Power-cycle the unit. If same fault occurs again, contact manufacturer
Fault 13 Calibration Overdue
Calibrate the unit.
44