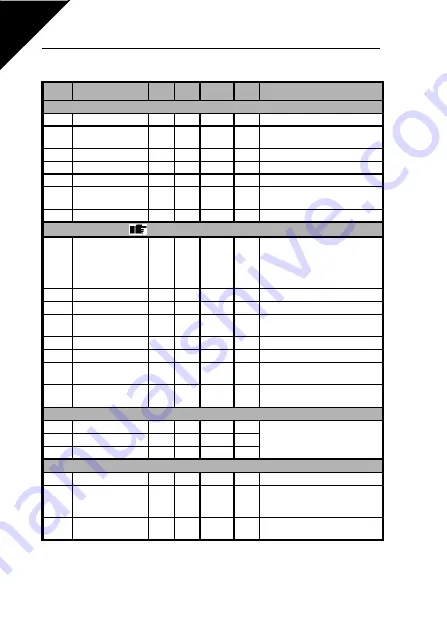
54
Parameters
Honeywell
9
9.13 SYSTEM PARAMETERS
NOTE!
These parameters are shown, when
P13.1 = 0.
Code
Parameter
Min
Max Default
ID
Note
Software information (MENU PAR -> S1)
S1.1
API system SW
2314
S1.2
API system SW
version
835
S1.3
Power SW ID
2315
S1.4
Power SW version
834
S1.5
Application SW ID
837
S1.6
Application SW
revision
838
S1.7
System load
839
(MENU PAR -> S2)
S2.1
Communication
status
808
Format:
xx.yyy
xx
= 0-64 (Number of error mes-
sages)
yyy
= 0 - 999 (Number of correct
messages)
S2.2
Fieldbus protocol
0
1
0
809
0 =
FB disabled
1
= Modbus
S2.3
Slave address
1
255
1
810
S2.4
Baud rate
0
5
5
811
0
=300,
1
=600,
2
=1200,
3
=2400,
4
=4800,
5
=9600,
S2.5 Number of stop bits
0
1
1
812
0
=1,
1
=2
S2.6
Parity type
0
0
0
813
0
= None (locked)
S2.7
Communication
time-out
0
255
0
814
0
= Not used,
1
= 1 second,
2
= 2 seconds, etc.
S2.8
Reset communica-
tion status
0
1
0
815
1
= Resets par. S2.1
Total counters
(MENU PAR -> S3)
S3.1
MWh counter
827
S3.2
Power on days
828
S3.3
Power on hours
829
User settings
(MENU PAR -> S4)
S4.1
Display contrast
0
15
15
830 Adjusts the display contrast
S4.2
Default page
0
20
0
2318
Defines which monitoring page
(1.1.-1.20) is shown after
startup.
0
= Not used
S4.3
Restore factory
defaults
0
1
0
831
1
= Restores factory defaults for
all parameters
Table 9.13: System parameters