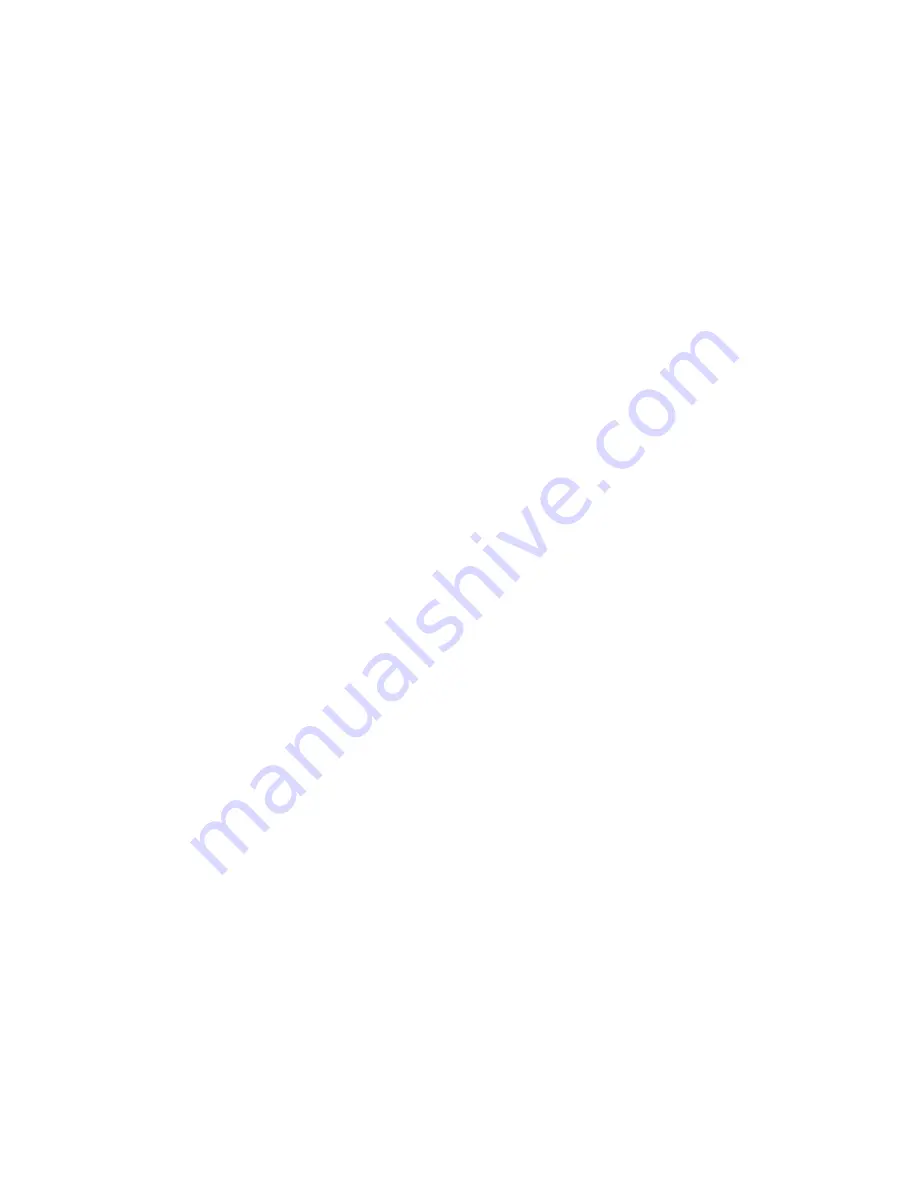
U2 COMBINATION VIEWING HEAD AND SIGNAL PROCESSORS
5
66-2071—02
connection. Use a flexible air supply line, to allow for
repositioning of the U2 and sight pipe until a final and
permanent position has been decided. A continuous flow of air
must be maintained in order to reduce conducted heat and to
keep the sight pipe and U2 lens free of dirt and debris. The air
supply must be clean, free of oils and water, and preferably
cool. In order to electrically isolate the U2, the purge air line
should be installed using an insulating material, such as a
rubber hose, in between the purge air line and the U2.
Clearance
Make sure there will be sufficient room to remove the U2 for
servicing.
Mounting
Honeywell offers a range of swivel mounts, both pipe thread or
flange mounting for use with sight pipes or direct windbox
mounting. Refer to the section “Accessories” on page 5.
Viewing Head Sighting
The sighting of the U2 should be parallel to the center line of
the burner in the direction of the flame. If used, the sight pipe
should be mounted as close to the center line as possible so
as to sight along the flame rather than across the flame. Doing
so will ensure continuing flame detection under changing load
conditions. Refer to Fig. 4, 5 and 6.
Utilizing a sighting or the sight pipe aimed at the root of the
flame (where the turbulent combustion air mixes with the
flame) is a good starting point for optimizing the sighting.
Where practical, using a swivel mount to “zero-in” on the
highest signal will assure the maximum performance. The
optimum scanner location is parallel to the burner center line.
The use of a swivel mount allows for line of sight adjustment,
where practical to use.
Examples of U2 installation with and without a swivel mount
are shown in Fig. 9 and Fig. 10. If using a sight pipe, the
diameter should be large enough to allow a reasonable field of
view and to allow for adjustment of the swivel mount angle.
Pulverized coal, unburned fuel, smoke, oil mist, dirt, dust and
other impurities in the fuel can act as masking agents that
attenuate the ultraviolet radiation that the flame emits. As well,
sour gas (H
2
S) can readily absorb 200nm UV wavelengths,
reducing the amount of ultraviolet radiation reaching the
detector. Care should be taken to select the proper viewing
head for the fuel used. Additionally, the contaminants that mask
UV can be diluted by providing a strong flow of air through the
sight pipe to clear a viewing path through the attenuating
material. Refer to the Purge Air section of this manual.
It may also be desirable to sight the detector at an area
containing fewer masking agents such as near the burner
nozzle or near the entrance of the combustion air. Increasing
the viewing area of the detector by shortening the sight pipe or
by increasing the diameter of the sight pipe can also reduce
the attenuating effect of masking agents.
With low NOx gas burners, the UV radiation is usually much
less in intensity and spread out. Relatively high readings can
be obtained from all over the furnace when many burners are
on. This is particularly true when flue gas recirculation is used.
There will however, be a relatively stronger signal near the
“root” of the flame and the more intense spot should be
located during the aiming or sighting process. The “root” or
intense spot may be further out than with the standard gas
burner so it is imperative that a swivel mount be used when
making sighting adjustments.
As an example of proper sighting challenges, detecting flame
in a sulfur recovery unit can present a challenge for IR flame
monitors. The IR detector will detect natural gas used for the
warm-up of the reactor. Usually the combustion air is turbulent
enough to cause a good flicker signal.
When sour gas is introduced and the natural gas is shut down,
the flame signal could potentially drop off or drop out entirely
due to a complete change in the flicker content for the existing
U2 sighting. In this case, optimizing the flame signal for the
sour gas by “zeroing-in” on this flame, and not the warm-up
burner, may be beneficial.
Once optimizing the sighting for the sour gas has been
completed, the signal level could potentially be too low on the
natural gas. In this case, using the UV detector for this
application may be beneficial. It may be beneficial to use two
sets of set points for Flame On and Flame Off, one set for
proving and detecting the natural gas flame and the other for
proving and detecting the sour gas flame. The switch-over
from the two different files should be done when removing the
natural gas burner. This can be implemented from the burner
management system. The switch-over and the use of different
files with independent settings is explained in the sections
“File” on page 8 and “Manual Setup” on page 13.
Another factor that needs to be considered when aiming the
viewing head is the load condition of the boiler. The flames
from a burner can be radically different at different loads. This
is one of the reasons for choosing an optimum sighting initially
that will maximize signal swing due to changing loads.
ACCESSORIES
The following accessories are available for use with the U2.
Orifice Disks (kit M-702-6)
– Used to reduce the signal
brightness in cases where the signal brightness is too strong.
Located immediately in front of the lens, it will reduce the
amount of signal to the sensors. Bag assembly contains
orifice disks and retaining rings. Orifice disks come with 3/8,
1/4, 3/16 and 1/8 inch diameter holes. Contact your distributor
or Honeywell for guidance in using orifice disks.
Locking coupler with purge port
(R-518-CL12-PG)
–
Adapter is a 1 in. NPTM locking quick disconnect/cam and
groove coupler with 1/2 in. NPT purge port. Used with R-518-
PT12 and R-518-PT12L insulating locking coupler adapters.
Insulating locking coupler adapters (R-518-PT12 and R-
518-PT12L)
– 1 in. NPTM Ultem adapters insulate the viewing
head from heat and are used with the R-518-CL12-PG purge
air adapter or the R-518-CL12-HTG locking coupler. The R-
518-PT12L has a quartz lens.
Swivel mounts (M-701-1, M-701-2, M-701-2-FLG, M-701-2-
SS, M-701-3, M-701-3P, M-701-4)
– All have 1 in. NPTF
viewing head connections on one end with varying process
connections including 2 in. pipe slip-on, 2 in. NPTF, 2 in.
flanged, 2 in. NPT in stainless steel construction, 4.5 in.
flanged with 3 bolts, 3 in. NPTF and 2-bolt flanged.