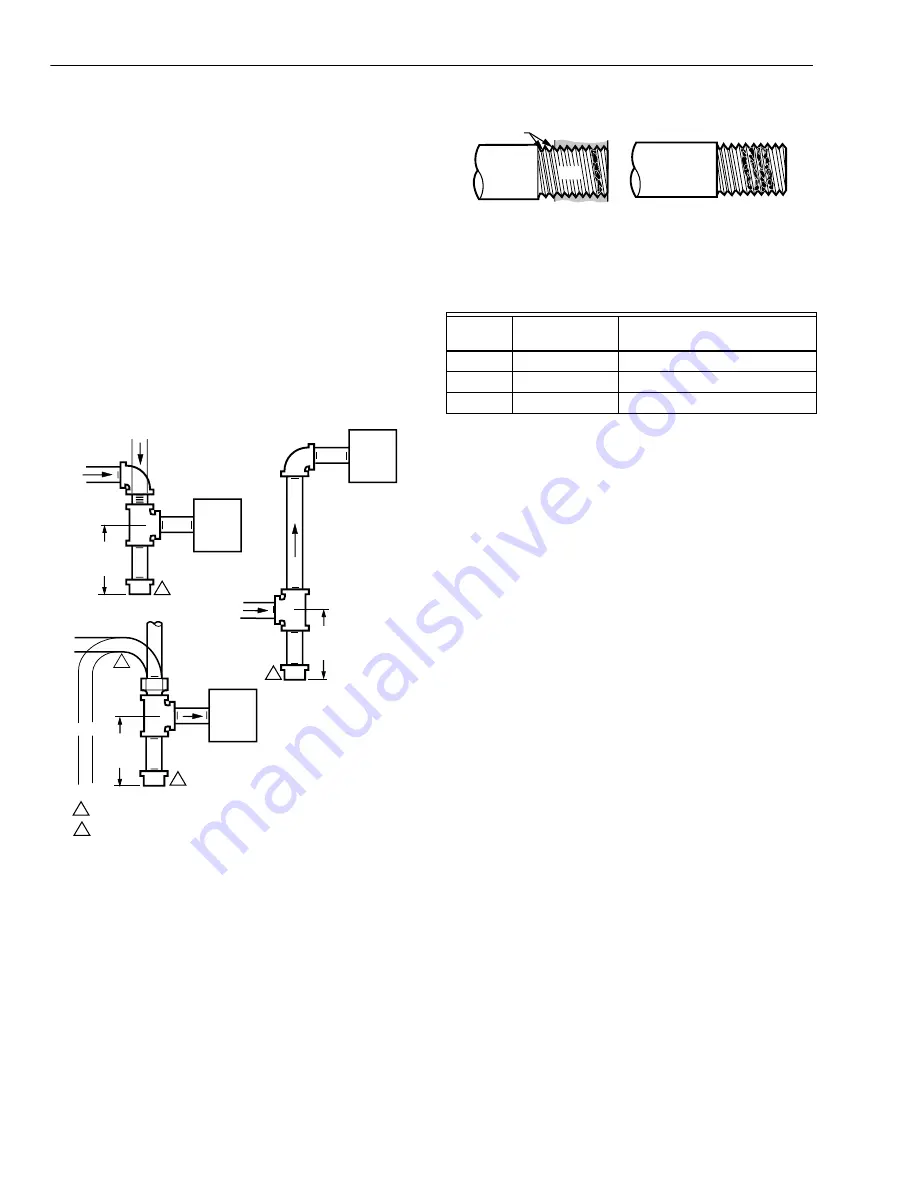
V8200 COMBINATION GAS CONTROLS
68-0045—3
6
Install Gas Control
1.
Mount the gas control 0-90 degrees, in any direction,
from the upright position of the gas control knob,
including vertically.
2.
Mount the control so gas flow is in the direction of the
arrow on the bottom of the gas control.
3.
Thread pipe the amount shown in Table 4 for insertion
into the gas control. Do not thread pipe too far. Valve
distortion or malfunction may result if the pipe is
inserted too deeply into the gas control.
4.
Apply a moderate amount of good quality pipe
compound (DO NOT use Teflon tape) to pipe only,
leaving two end threads bare. On LP installations, use
compound resistant to LP gas.
5.
Remove seals over gas control inlet and outlet if
necessary.
6.
Connect pipe to gas control inlet and outlet. Use wrench
on the square ends of the gas control. If an adapter is
used, place wrench on adapter rather than gas control.
Refer to Figs. 2 and 7.
Fig. 5. Install sediment trap.
Fig. 6. Use moderate amounts of pipe compound.
Table 4. NPT Pipe Thread Length in inches.
Connect Pilot Gas Tubing
1.
Cut tubing to desired length and bend as necessary
for routing to pilot burner. Do not make sharp bends or
deform the tubing. Do not bend tubing at gas control or
pilot burner after compression fitting has been
tightened, as this may result in gas leakage at the
connection.
2.
Square off and remove burrs from end of tubing.
3.
Unscrew compression fitting from the pilot outlet
(Fig. 2). Slip the compression fitting over the tubing
and slide out of the way.
NOTE: When replacing a gas control, cut off old
compression fitting and replace with the new
compression fitting provided on the gas control.
Never use the old compression fitting as it may
not provide a gas-tight seal.
4.
Push tubing into the pilot gas tapping on the outlet
end of the control until it bottoms. While holding
tubing all the way in, slide compression fitting into
place and engage threads—turn until finger tight. Then
tighten one more turn with wrench. Do not overtighten.
Refer to Fig. 8.
5.
Connect other end of tubing to pilot burner according to
pilot burner manufacturer’s instructions.
GAS
CONTROL
GAS
CONTROL
HORIZONTAL
DROP
PIPED
GAS
SUPPLY
PIPED
GAS
SUPPLY
3 IN.
(76 MM)
MINIMUM
3 IN.
(76 MM)
MINIMUM
RISER
GAS
CONTROL
TUBING
GAS
SUPPLY
HORIZONTAL
DROP
3 IN.
(76 MM)
MINIMUM
RISER
M3077
2
1
2
2
1
2
ALL BENDS IN METALLIC TUBING SHOULD BE SMOOTH.
CAUTION: SHUT OFF THE MAIN GAS SUPPLY BEFORE REMOVING
END CAP TO PREVENT GAS FROM FILLING THE WORK AREA. TEST
FOR GAS LEAKAGE WHEN INSTALLATION IS COMPLETE.
Pipe Size
Thread Pipe
This Amount
Maximum Depth Pipe Can Be
Inserted Into Control
3/8
9/16
3/8
1/2
3/4
1/2
3/4
13/16
3/4
TWO IMPERFECT
THREADS
GAS CONTROL
THREAD PIPE THE AMOUNT
SHOWN IN TABLE FOR
INSERTION INTO GAS CONTROL
APPLY A MODERATE AMOUNT OF
PIPE COMPOUND TO PIPE ONLY
(LEAVE TWO END THREADS BARE).
M3075B
PIPE