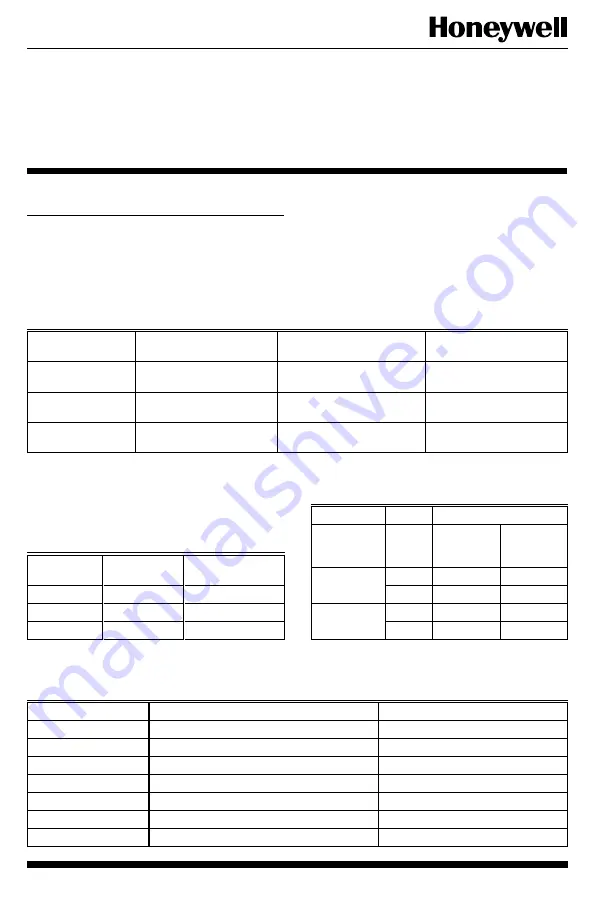
1
69-0624—2
J.H. • Rev. 9-94 • ©Honeywell Inc. 1994 • Form Number 69-0624—2
VR8300/VR8301
Continuous Pilot Combination
Gas Control
Application
These continuous pilot gas controls are used in gas-fired
appliances with capacities up to 200 cu ft/hour at 1 in. wc
pressure drop [5.7 cu m/hour at 0.25 kPa] on natural gas.
They include a manual valve, safety shutoff, single auto-
matic operators, and a pressure regulator. See Table 3 for
temperature ranges and regulator types.
BODY PATTERN: Straight-through body pattern.
INLET X OUTLET SIZES AVAILABLE: 1/2 x 1/2 in., 1/2 x
3/4 in., and 3/4 x 3/4 in. (factory-installed inlet flange).
ADAPTERS: Adapters available for 1/2 and 3/4 inch straight
and angle connections. Refer to Table 4.
ELECTRICAL RATINGS:
Voltage and Frequency: 24 Vac, 50/60 Hz.
Current Draw: 0.70A.
CAPACITY: See Table 1.
TABLE 1: CAPACITY OF VR8300/VR8301
Size
(Inlet x Outlet)
Capacity (at 1 in. wc
pressure drop)
a
Minimum
Regulated Capacity
Maximum
Regulated Capacity
1/2 x 1/2
180 cu ft/hr
[5.1 cu m/hr]
30 cu ft/hr
[0.8 cu m/hr]
225 cu ft/hr
[6.4 cu m/hr]
1/2 x 3/4
190 cu ft/hr
[5.4 cu m/hr]
30 cu ft/hr
[0.8 cu m/hr]
290 cu ft/hr
[8.2 cu m/hr]
3/4 x 3/4
200 cu ft/hr
[5.7 cu m/hr]
30 cu ft/hr
[0.8 cu m/hr]
300 cu ft/hr
[8.5 cu m/hr]
a
Capacity based on 1000 Btu/cu ft, 0.64 specific gravity natural gas at 1 in. wc pressure drop [37.3 MJ/cu m, 0.64 specific
gravity natural gas at 0.25 kPa pressure drop.
Model Number
Ambient Temperature Range
Regulator Type
VR8300A
0° F to 175° F [-18° C to +79° C]
Standard-opening
VR8300C
0° F to 175° F [-18° C to +79° C]
Step-opening
VR8300H
0° F to 175° F [-18° C to +79° C]
Slow-opening
VR8300K
-40° F to 175° F [-40° C to +79° C]
Slow-opening
VR8300M
-40° F to 175° F [-40° C to +79° C]
Standard-opening
VR8300P
-40° F to 175° F [-40° C to +79° C]
Step-opening
VR8301
0° F to 175° F [-18° C to 79° C]
Standard-opening
TABLE 3—TEMPERATURE RANGES AND REGULATOR TYPES.
Use conversion factors in Table 2 to convert capacities
for other gasses.
TABLE 2—GAS CAPACITY
CONVERSION FACTORS.
Gas
Specific
Gravity
Multiply Listed
Capacity By
Manufactured
0.60
0.516
Mixed
0.70
0.765
Propane
1.53
1.62
TABLE 4—FLANGE PART NUMBERS.
Part Number
Inlet/Outlet
Pipe Size
Flange
Type
Without
Hex
Wrench
With
Hex
Wrench
1/2 inch NPT
Straight
394599-6
393690-16
Elbow
394599-3
393690-13
3/4 inch NPT
Straight
394599-4
393690-14
Elbow
394599-5
393690-15
NOTE: Flange kits include one flange with attached O-ring
and fan mounting screw.