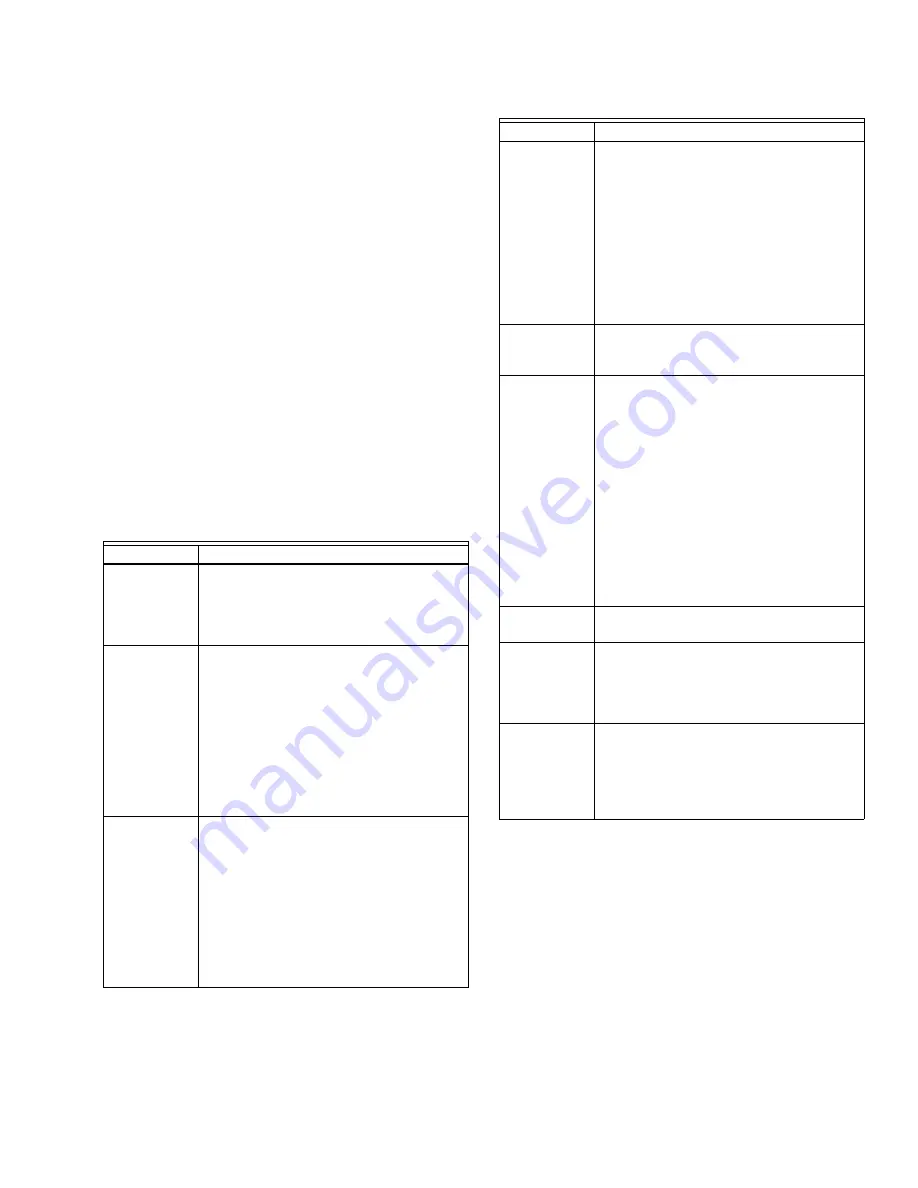
WEBVISION™
75
95-7769—01
UV Outputs
Use Table 53 to configure the Unit Ventilator Outputs for
heating and cooling stages. The outputs could be of stages,
PWM, or floating types. In addition, the number of fan speeds
and Economizer types must be set. You can also select
optional points.
Purpose
Select all outputs, including optional outputs, to be controlled
by the Unit Ventilator Controller.
Mode
Configuration can be performed with the wizard Off-line or
On-line.
Procedure
1.
Click the
UVOutputPane
button on the left pane to
open the
Output Configuration
page.
2.
Enter information into available fields.
3.
Click
Commit
to save the settings or
Reset
to revert to
the last saved settings.
4.
Click
Next
to open the
Input Configuration
page.
UV Outputs fields
UV Inputs
Use Table 54 to configure the Unit Ventilator Inputs for the
space temperature sensor type, wall module type, and the
voltage and digital inputs for a Unit Ventilator application.
Purpose
To select all sensors to be wired to the Unit Ventilator
Controller.
Mode
Configuration can be performed with the wizard Off-line or
On-line.
Table 53. Unit Ventilator Outputs.
Name
Definition
Fan Speeds
Select one of the following fan speeds:
•
No_Fan
•
One_Speed
•
Two_Speed
•
Three_Speed
Heating
Select one of the following Heating types:
•
Heating_Stage_1
•
Heating_Stage_2
•
Heating_PWM
•
Heating_Floating
•
No_Heating
If you select Floating, the Motor Speed field
displays actuator speed in seconds.
If you select PWM, the PWM Settings
become editable.
Cooling
Select one of the following Cooling types:
•
Cooling_Stage_1
•
Cooling_Stage_2
•
Cooling_PWM
•
Cooling_Floating
•
No_Cooling
If you select Floating, the Motor Speed field
displays actuator speed in seconds.
If you select PWM, the PWM Settings fields
become editable.
Economizer
Selection of Economizer mixed air damper
actuator type: None (or packaged external
economizer), PWM, or Floating.
•
Econo_None_Pkgd
•
Econo_PWM
•
Econo_Floating
NOTE: If you configure a floating or PWM
economizer, you MUST select a
Discharge Air sensor (see Unit
Ventilator Inputs) to enable
automatic damper control.
Motor Speed
Actuator motor speeds (in seconds).
Enabled with a selection of floating heating,
floating cooling or floating economizer.
Optional
Points
The first optional point is enabled if there is
sufficient room on the controller. After you
select the first point, the second one is
enabled if there is sufficient space, and so
on.
The following options are available:
•
Status_Occupied - (output energized
when controller is in Occupied mode)
AND/OR
•
Aux_Econ1 - (Emulates a T7300 – for
controlling an external economizer) AND/
OR
•
Free1 - (Network-controlled output) AND/
OR
•
Unused - (Point is unused)
Controller
Type
The Model type.
Power
Frequency
This field defines the line voltage that Excel
10 Controllers use and also tells LonSpec
the calculation required for noise immunity.
The calculation differs for 50 and 60 Hz
applications
PWM Settings PWM Period time (in seconds).
•
Zero Pulse time for a 0 percent output
signal (in seconds).
•
Full Pulse time for a 100percent output
signal (in seconds). This value must be
less than or equal to the PWM Period.
Table 53. Unit Ventilator Outputs. (Continued)
Name
Definition