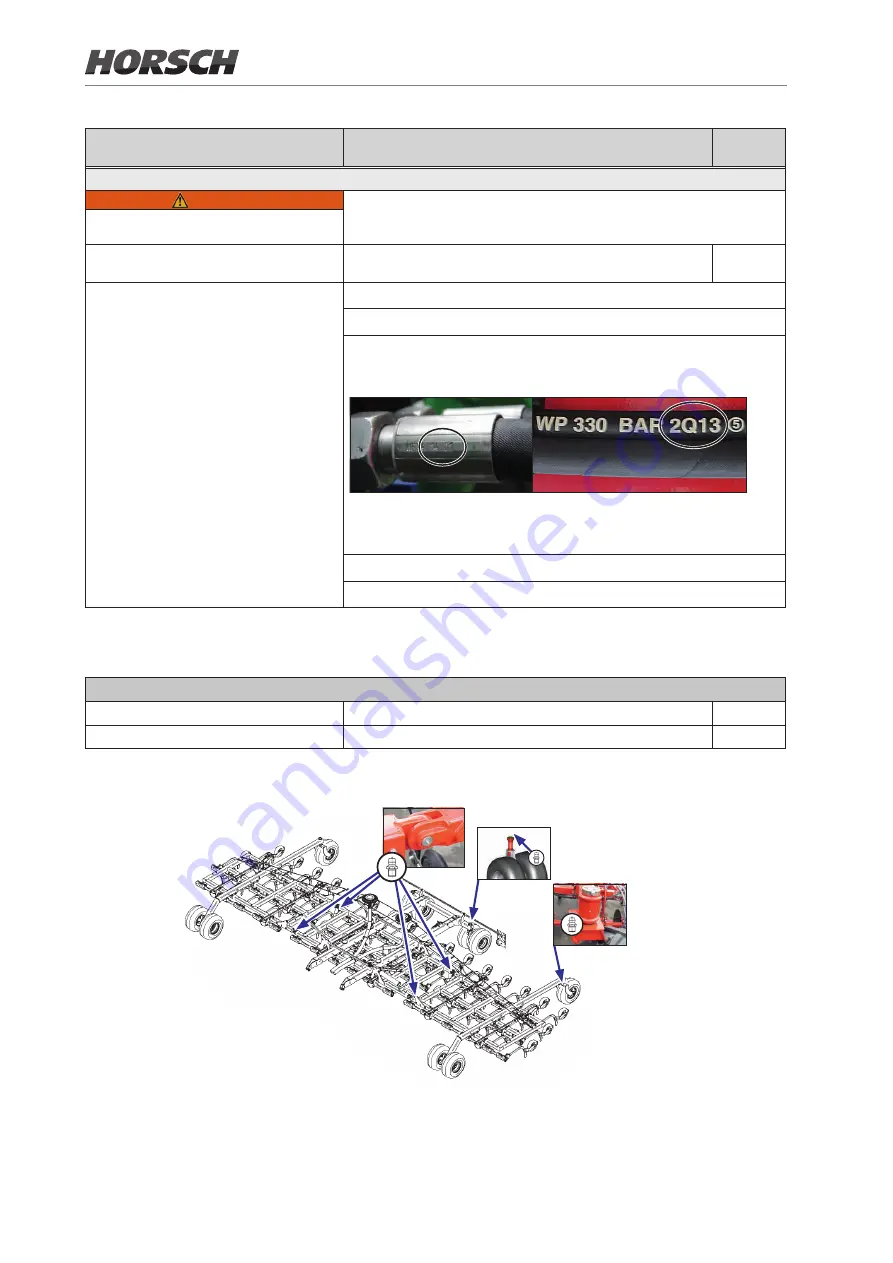
Maintenance location
Work instructions
Interval
Hydraulics
WARNING
Lower all hydraulically lifted parts (e.g. wings, packer, undercarriage,
etc.) to the ground before performing any work on the hydraulic system.
Depressurise the hydraulics on the tractor and implement side!
Hydraulic system and components
Check all hydraulic components and hoses for function,
leak tightness, fastening and chafing
40 h
hydraulic hoses
Check the hydraulic hoses regularly for damage (cracks, chafing, etc.).
Replace damaged and faulty hoses immediately.
Hydraulic hoses must be replaced after 6 years. For this purpose pay
attention to the manufacturing date on the crimp sleeve (year/month)
and the hose (quarter/year):
Crimp sleeve
Hose
Depending on the conditions of use (e.g. weather influences) or in case of
higher strains on the machine the hoses may need to be replaced earlier.
Have the hydraulic system checked by an expert at least once every year.
In addition follow the country specific regulations and directives.
NOTES:
•
The maintenance interval designates maintenance on each working day before working with the machine.
•
Follow additional maintenance notes in the respective chapters.
Lubrication points
(Lubrication grease: DIN 51825 KP/2K-40) - Number of lubrication points in brackets
Fig.1 Locking bolt
lubricate (4)
40 h
Fig. 2/3 Undercarriage pivot bearing
lubricate (4)
Daily
Fig. 2 (2x)
Fig. 3 (2x)
Fig.1
Lubrication points with the addition "2x" can be found on either side of the machine.
44