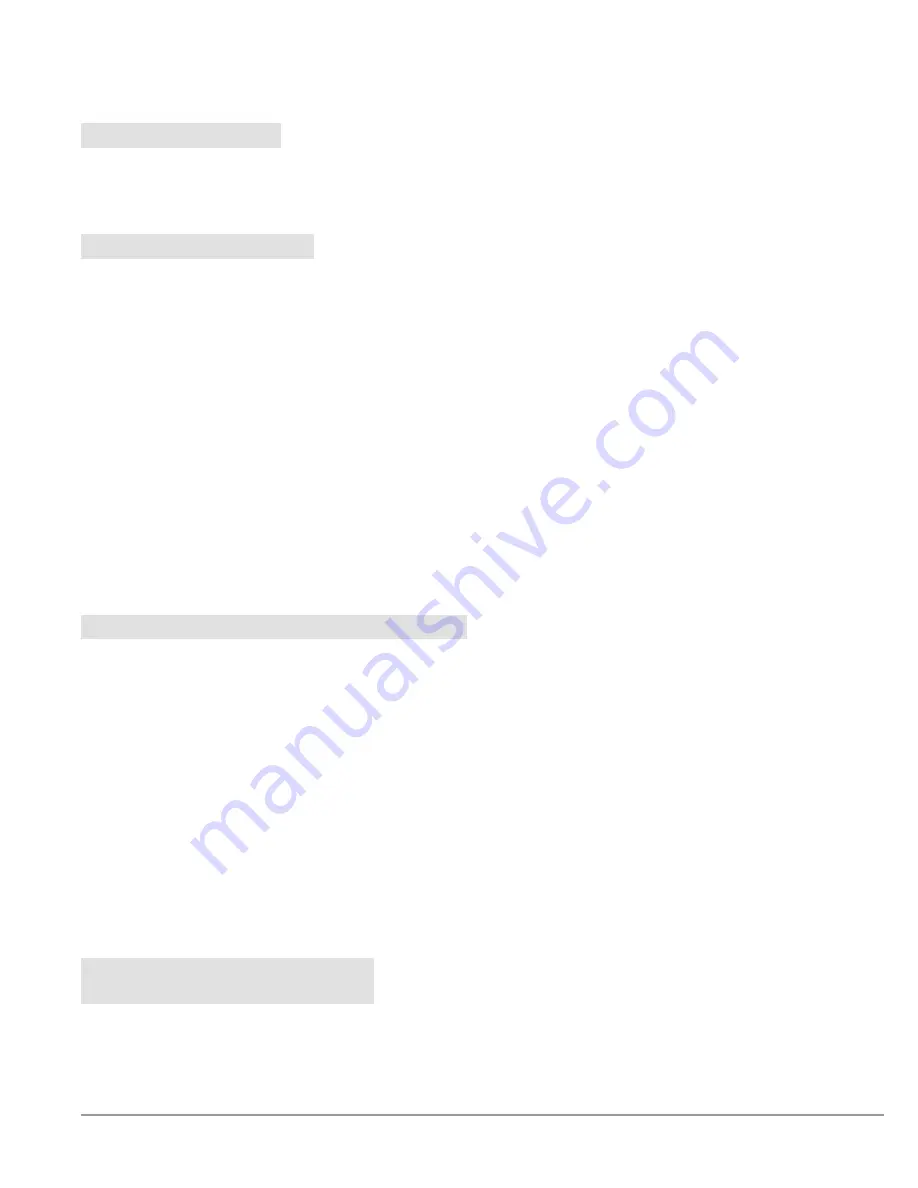
iii
installation
&
operation
manual
|
ola
heating
system
TABLE OF CONTENTS
Customer Interface Connections |
Control TCR (Temperature Control Relay) |
High-Limit TCR (Temperature Control Relay) |
iii
installation
&
operation
manual
|
ola
heating
system
TABLE OF CONTENTS
Customer Interface Connections |
Control TCR (Temperature Control Relay) |
High-Limit TCR (Temperature Control Relay) |