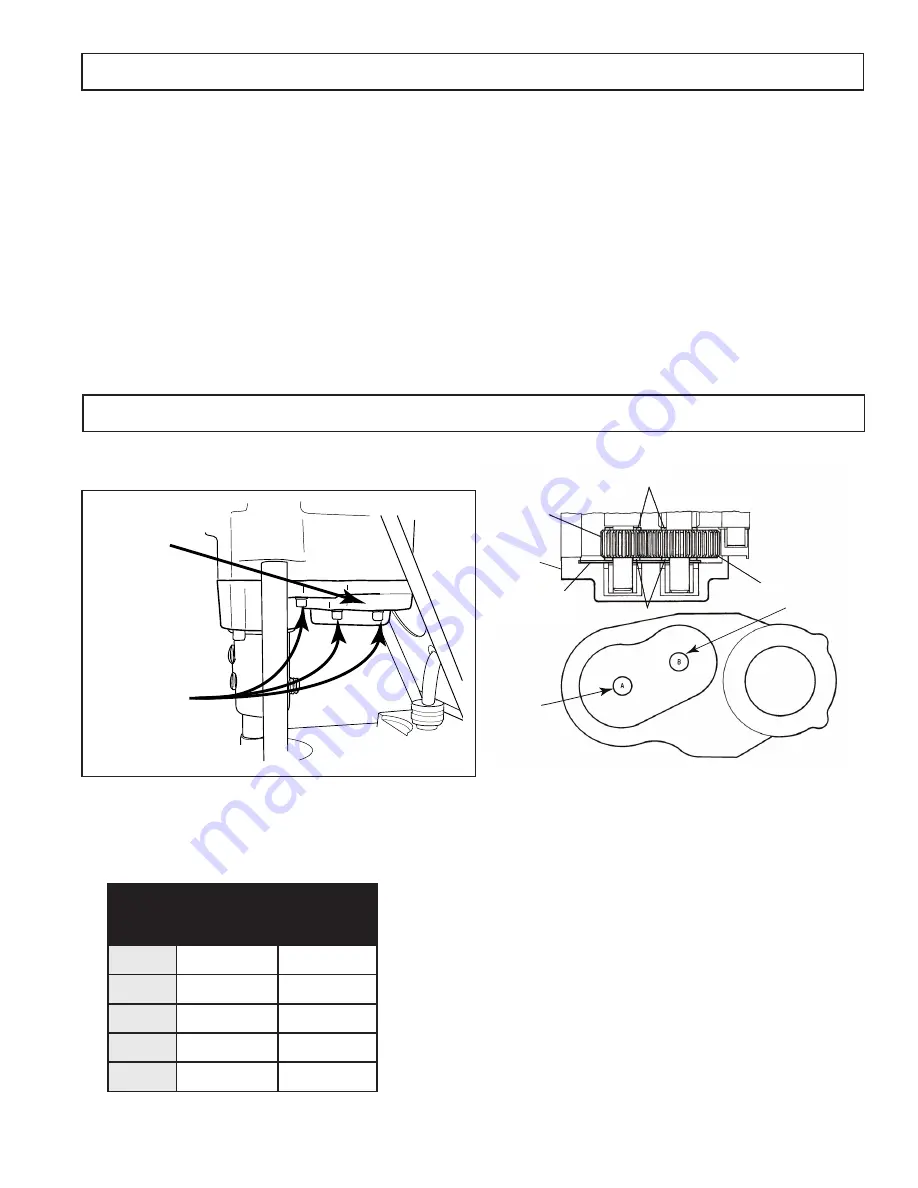
Drawings above show arrangement of gears. Be sure that upper and lower washers are replaced on
Shafts A and B when changing gears. If necessary, refer to exploded view when removing lower bearing
retainer cap.
Drill unit comes with 18-tooth gear (40012) on Shaft A and 30-tooth gear
(40016) on Shaft B to provide 120 RPM. For other RPM’s, use optional
gears with the following procedure.
1. Remove the Lower Bearing Retainer Cap by removing the four
Cap screws (Detail No. 122) and two Cap Screws (Detail No. 123)
2. Remove gears from Shafts A and B, being careful to save the two
Altered Torrington Thrust Washers (Detail No. 95) and two lower
Washers (Detail No. 98)
3. Be certain that the two Altered Torrington Thrust washers are
first mounted on Shaft A and B.
4. Slide proper gears on Shafts A and B (refer to table on left).
5. Mount lower washers on both shafts.
6. Pack gears with liberal supply of grease.
7. Replace Lower Bearing Retainer Cap. Replace and tighten all
six cap screws.
7
GEAR COMBINATIONS FOR VARIOUS RPMS
In addition to providing a positive method to insure that a slug is
not retracted with the cutter, the ejector rod serves as a conduit
for the cutting fluid and as a centering guide for positioning the
Mag Drill on the workpiece. Under normal conditions, the point
of the ejector rod should be kept at least 1/16" above the work
surface.
It is important that the point of the ejector rod not be
allowed to rest on the work surface for two reasons:
A)
The point will drag on the work surface when Mag Drill is
repositioned which may cause the ejector rod to become bent.
B)
The ejector rod may hold the front of the magnet off of the
work surface, deminishing its holding ability.
EJECTOR ROD ADJUSTMENT
Motor
Shaft
Detail No. 96
Spline Shaft
C
u
ttter Side of Drill
Gear
Altered Washer
(40002)
Gear
B
A
B
Lower Bearing
Retainer
(40005) Cap
Lower Bearing
Retainer
(40006)
Washer (40020)
To adjust the ejector rod:
1. Place the Mag Drill on a steel plate and turn the magnet
on.
2. Loosen the lock nut (Detail No. 14) and rotate the knurled
nut (Detail No 15) until the point of the ejector rod is in the
desired location.
3. When adjusted properly, the point should clear the work
surface (1/16" minimum) both when the magnet is on and
when it is off (Mag Drill riding on glide post).
4. When adjustment is complete, using a wrench, retighten
the lock nut against the underside of the tie bar
(Detail No. 11)
Gear
Case
Cover
Remove
Screws
Cutter
RPM
No. of Teeth per Gear
Shaft A
Shaft B
100
16
32
120
18
30
200
24
24
332
30
18
400
32
16