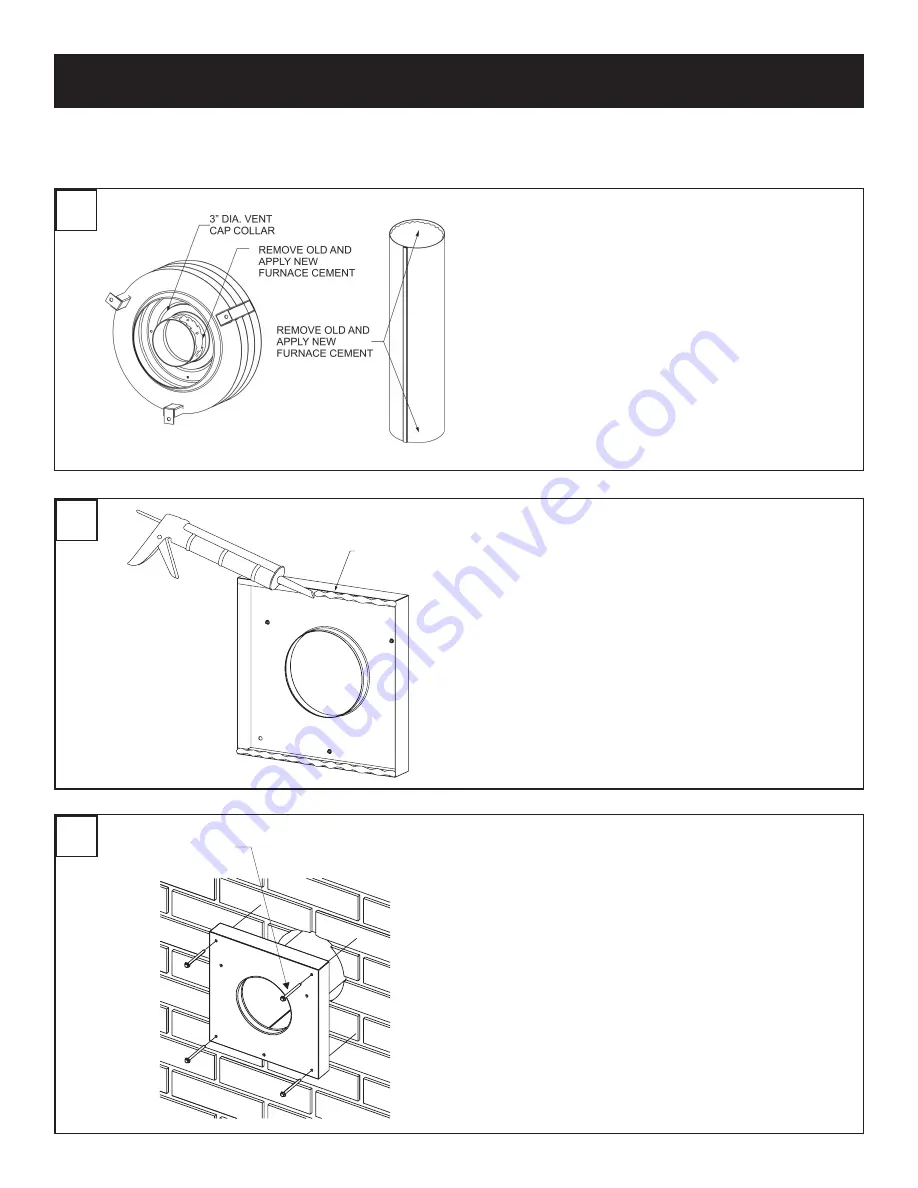
27536-0-0610
Page 26
1
2
3
reaSSeMBlY anD reSealinG Vent-air intaKe SYSteM
When vent-air intake system is removed for servicing the furnace, the following steps will assure proper reassembly and resealing of
the vent-air intake assembly.
Remove old furnace cement from flue outlet collar on combustion
chamber and collar of vent cap. Remove old furnace cement from
both ends of 3" (76 mm) diameter flue outlet tube.
Remove old caulking beneath the edge of the outside wall
mounting plate. Apply new caulking beneath the edge of the
outside wall mounting plate. Use additional caulking to correct
uneven wall surface, such as clapboard.
Attach 5" (127 mm) diameter air inlet tube onto the collar of air
drop assembly. Attach caulked, outside wall mounting plate into
the 5" (127 mm) diameter air inlet tube. Position the outside wall
mounting plate so that 5" (127 mm) diameter air inlet tube has
a slight downward slope to the outside. The downward slope
is necessary to prevent the entry of rainwater. Attach outside
wall mounting plate to exterior wall with (4) #10 x 1" (25 mm)
screws provided.
REMOVE OLD
APPLY
CAULKING
AND
NEW
(4) #10 x 2 ½”
SCREWS