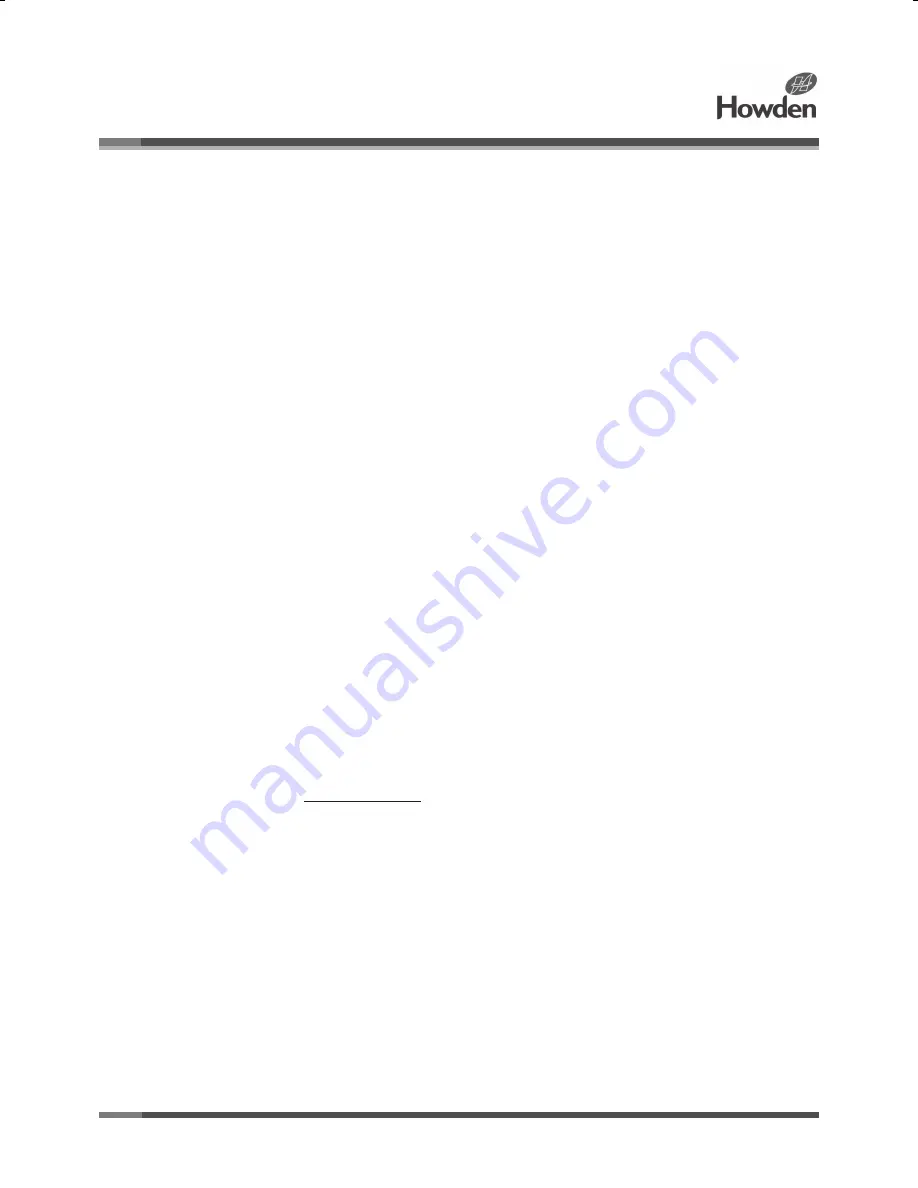
ISRB
2005 GEA 20260
Page 19 of 24
Coating General
Procedures for application are for one coat, but when
multiple coats are to be applied, EACH coat must be
completely cured per CURE procedure described
following, before applying the next coat.
Coating Application
See notes on can concerning ventilation and
inflammability.
Each layer of coating should be applied as evenly as
possible. Note directions on the curing of each
coating layer applied before applying subsequent
coats.
The best distance of spray can nozzle to surface
being coated is 8” to 12”. Try to maintain this distance
wherever space conditions allow it.
Coating Cure
This procedure is for EACH coat. When multiple
coats are to be applied, this curing procedure must
be used on EACH coat before the next coat is
applied. Keep coated parts clean during curing.
Note that coated parts may feel dry or “tack free”
after a few minutes, but the coat will not have the
CURE that is required.
Curing Procedures
Alternate #1
Let set for 1-1/2 hours, minimum, at normal room
temperature (not less than 70°F).
**Abradable coating applied to impellers is Slip Plate
#3 as manufactured by Superior Graphite Co. For a
material safety data sheet, go to www.slipplate.com.
Study material safety data sheet before working with
Slip Plate #3.
Alternate #2
Where ambient, and coated metal temperatures, are
not at least 70°F, allow each coat to cure at least
overnight in shop ambient (not warehouse or
outdoors).
Alternate #3
Cure in oven, or by other source of even heat (not
flame), for 10 minutes, minimum, at a temperature of
310°F ±10.
Alternate #4
Cure in oven, or by other source of even heat (not
flame), for one-half hour, minimum, at a temperature
of 200°F ±10°.
Check for Rotation
Finish blower build up if not completely assembled
when coated. In some instances, it is possible that
clearances will be closed by coating to the extent that
some surfaces touch. This is all right because the
coating will wear (abrade) off as required. However,
the blower may be hard to turn initially as a result.
Turn over by hand until the running is free. Do not try
to free up the blower by coupled or belted drive, and
do not try to spin the rotors with shop air. Do not
attempt to use any kind of solvent or cleaner to
partially remove, coating – as this could ruin all of the
coating. If necessary, coating can be scraped for
such partial removal.
Complete Removal of Coating
This is for complete removal (to bare metal) of
coating and may require some blower disassembly
(depending on blower size and accessibility) for
access to the coated parts and any overspray. Apply
removal fluid liberally with a clean, “soaked” rag.
Vigorously rubbing with this rag and scraping of the
softened coating is required to clean surfaces down
to bare metal, the amount of effort required will vary,
depending upon the solvent used. Some are more
effective than others. Protect surfaces, not coated,
from rust.
ISRB 2005 GEA 20260.indd 19
17/09/2015 12:53
Summary of Contents for Roots 2500 Series WHISPAIR MAX
Page 14: ...ISRB 2005 GEA 20260 Page 14 of 24 Troubleshooting Checklist...
Page 15: ...ISRB 2005 GEA 20260 Page 15 of 24 2500 Series WHISPAIR Max Blowers...
Page 20: ...ISRB 2005 GEA 20260 Page 20 of 24...
Page 21: ...ISRB 2005 GEA 20260 Page 21 of 24 Assembly of 2500 Series WHISPAIR Max Blower...
Page 22: ...ISRB 2005 GEA 20260 Page 22 of 24 Assembly of 2500 Series DVJ Blower...