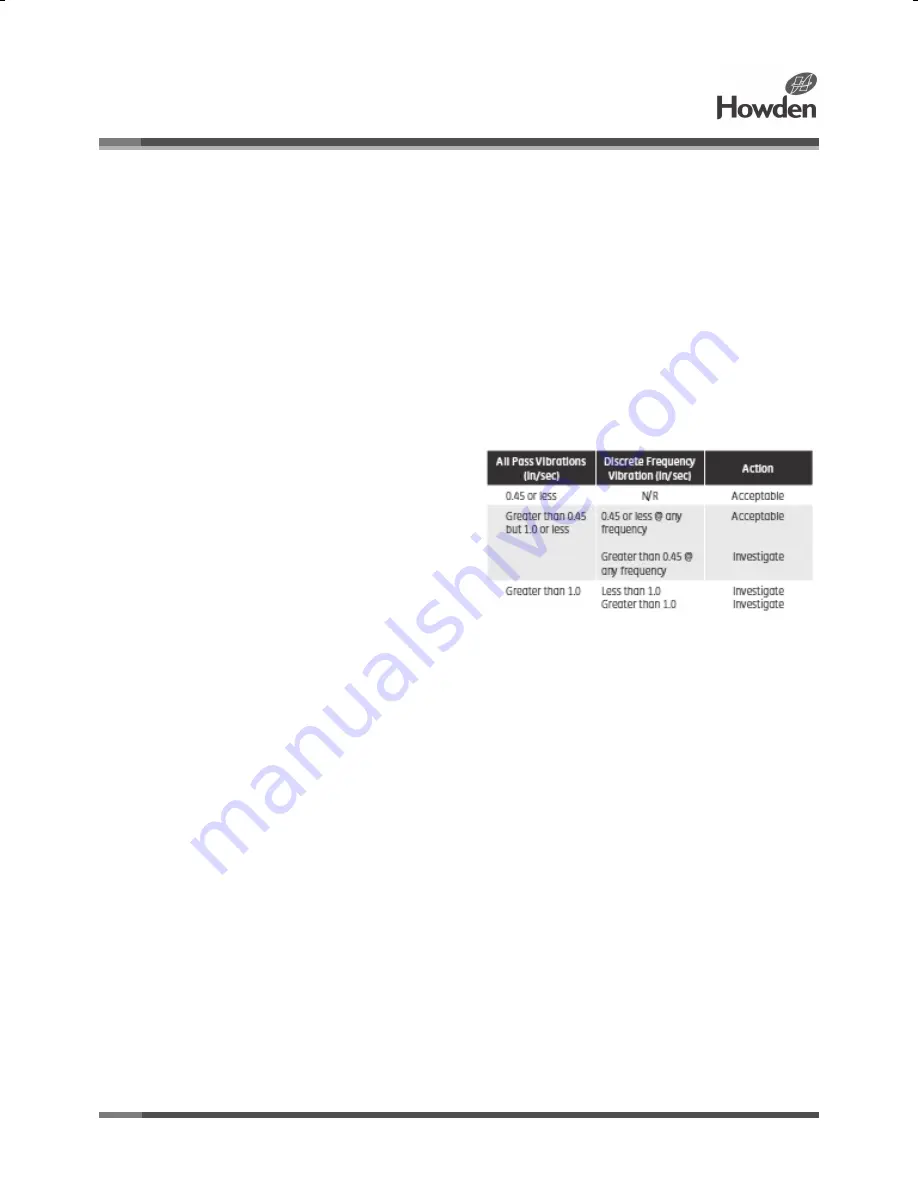
ISRB
2005 GEA 20260
Page 5 of 24
CHECKLIST for suggestions on various problems
that may appear.
The blower should now be ready for continuous duty
operation at full load. During the first few days make
periodic checks to determine whether all conditions
remain steady, or at least acceptable. This may be
particularly important if the blower is supplying air to
a process system where conditions can vary. At the
first opportunity, stop the blower and clean the
temporary inlet protective screen. If no appreciable
amount of debris has collected, the screen may be
removed. See comments under INSTALLATION. At
this same time, verify leveling, coupling alignment or
belt tension, and mounting bolt tightness.
Should operating experience prove that blower
capacity is a little too high for the actual air
requirements, a small excess may be blown off
continuously through the manual unloading or vent
valve. Never rely on the pressure relief valve as an
automatic vent. Such use may cause the discharge
pressure to become excessive, and can also result in
unsafe operation of the valve itself. If blower capacity
appears to be too low, refer to the
TROUBLESHOOTING CHECKLIST. See page 11 for
additional troubleshooting information regarding DVJ
units.
Vibration Assessment Criteria
With measurements taken at the bearing locations on
the housings, see chart below for an appropriate
assessment guide for rotary lobe blowers rigidly
mounted on stiff foundations.
In general, blower vibration levels should be
monitored on a regular basis and the vibration trend
observed for progressive or sudden change in level.
If such a change occurs, the cause should be
determined through spectral analysis.
As shown on the chart below, the level of all pass
vibration will determine the need to measure discrete
frequency vibration levels and the action required.
Installation
Howden Roots blowers & exhausters are treated
after factory assembly to protect against normal
atmospheric corrosion. The maximum period of
internal protection is considered to be one year under
average conditions, if shipping plugs & seals are not
removed. Protection against chemical or salt water
atmosphere is not provided. Avoid opening the unit
until ready to start installation, as corrosion protection
will be quickly lost due to evaporation.
If there is to be an extended period between
installation and start up, the following steps should be
taken to ensure corrosion protection. See “Cleaning
& Preservation” on page 14 for Whispair Max and
DVJ units.
Coat internals of cylinder, gearbox and drive end
bearing reservoir with Nox-Rust VCI-10 or
equivalent. Repeat once a year or as conditions
may require. Nox-Rust VCI-10 is petroleum
soluble and does not have to be removed before
lubricating. It may be obtained from Daubert
Chemical Co., 2000 Spring Rd., Oak Brook, Ill.
60521.
Paint shaft extension, inlet and discharge
flanges, and all other exposed surfaces with Nox-
Rust X-110 or equivalent.
Seal inlet, discharge, and vent openings. It is not
recommended that the unit be set in place, piped
to the system, and allowed to remain idle for
extended periods. If any part is left open to the
atmosphere, the Nox-Rust VCI-10 vapor will
escape and lose its effectiveness.
Protect units from excessive vibration during
storage.
Rotate shaft three or four revolutions every two
weeks.
Prior to start up, remove flange covers on both
inlet and discharge and inspect internals to
insure absence of rust. Check all internal
clearances. Also, at this time, remove gearbox
ISRB 2005 GEA 20260.indd 5
17/09/2015 12:53
Summary of Contents for Roots 2500 Series WHISPAIR MAX
Page 14: ...ISRB 2005 GEA 20260 Page 14 of 24 Troubleshooting Checklist...
Page 15: ...ISRB 2005 GEA 20260 Page 15 of 24 2500 Series WHISPAIR Max Blowers...
Page 20: ...ISRB 2005 GEA 20260 Page 20 of 24...
Page 21: ...ISRB 2005 GEA 20260 Page 21 of 24 Assembly of 2500 Series WHISPAIR Max Blower...
Page 22: ...ISRB 2005 GEA 20260 Page 22 of 24 Assembly of 2500 Series DVJ Blower...