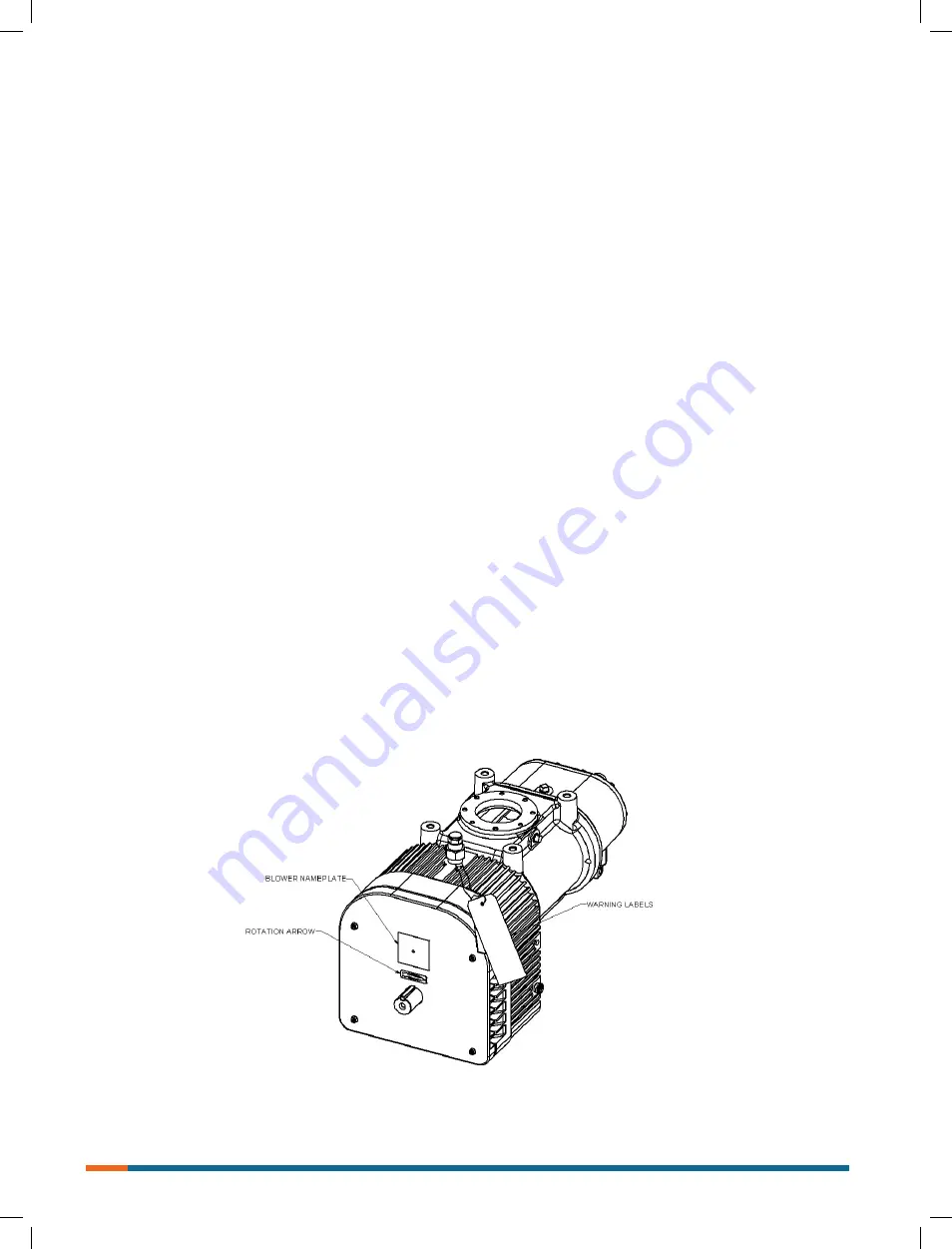
ISRB-2009, Rev. 02_17.
4
Installation
Howden Roots blowers arrive without lubrication in the sump,
see lubrication section for details.
Howden Roots blowers are treated after factory assembly to
protect against normal atmospheric corrosion. The maximum
period of protection is considered to be one year under
average conditions, if shipping plugs & seals or not removed.
Protection against chemical or salt water atmosphere is not
approved. Avoid opening unit until ready to start installation,
as corrosion protection will be quickly lost due to evaporation.
If there is to be an extended period between installation and
start-up, following steps should be taken to ensure corrosion
protection.
• Coat intervals of cylinder, gearbox and drive end bearing
reservoir with Nox-Rust VCI-10 or equivalent. Repeat
once a year or as conditions may require. Nox-Rust
VCI-10 is petroleum soluble and does not have to be
removed before lubricating. It may be obtained from
Daubert Chemical Co., 2000 Spring Rd., Oak Brook,
IL. 60521.
•
Paint shaft extension, inlet & discharge flanges and any
other exposed surfaces with Nox-Rust X-110 or
equivalent.
• Seal inlet, discharge and vent openings. It is not
recommended that blower be set in place, piped to the
system, and allowed to remain idle for extended periods.
If any part is left open to the atmosphere, the Nox-Rust
VCI-10 vapor will escape and lose its effectiveness.
• Protect blower from excessive vibration during storage.
• Rotate shaft three to four revolutions every two weeks.
•
Prior to start up, remove flange covers on both inlet &
discharge flanges and covers on vent opening and
inspect internal clearances. Also, at this time, inspect
gear box intervals thru breather location for rust.
Because of the completely enclosed blower design, location
of the installation is generally not a critical matter. A clean,
dry and protected indoor location is preferred; however, an
outdoor location will normally give satisfactory service. Impor-
tant requirements are that the correct grade lubricating oil be
provided for expected operating temperatures, and that the
blower be located so that routine checking and servicing can
be performed conveniently. Proper care in locating drive and
accessory equipment must also be considered.
Supervision of the installation by a Howden Roots Service
Engineer is not usually required for these units. Workmen with
experience installing light to medium weight machinery should
be able to produce satisfactory results. Handling of
equipment needs to be accomplished with care, and in
compliance with safe practices. Unit mounting must be solid,
without strain or twist, and air piping must be clean, accurately
aligned and properly connected.
Mounting
Two methods are used to handle a unit. One is to install lifting
lugs into the (4) 5/8-11 tapped holes in top of the unit. Test the
lifting lugs for tightness and potential fractures by tapping with
hammer. In lifting, keep the direction of cable pull on these
bolts as nearly vertical as possible. If unable to use the tapped
holes in top of unit for lifting, lifting slings or a special cradle
may be passed under the unit for vertical lift.
Summary of Contents for Roots 412 HPT
Page 1: ...www howden com Roots 412 HPT Blower Installation Operation Maintenance Manual...
Page 11: ...11 ISRB 2009 Rev 02_17...
Page 12: ...ISRB 2009 Rev 02_17 12...
Page 13: ...13 ISRB 2009 Rev 02_17...
Page 14: ...ISRB 2009 Rev 02_17 14...
Page 15: ...15 ISRB 2009 Rev 02_17...