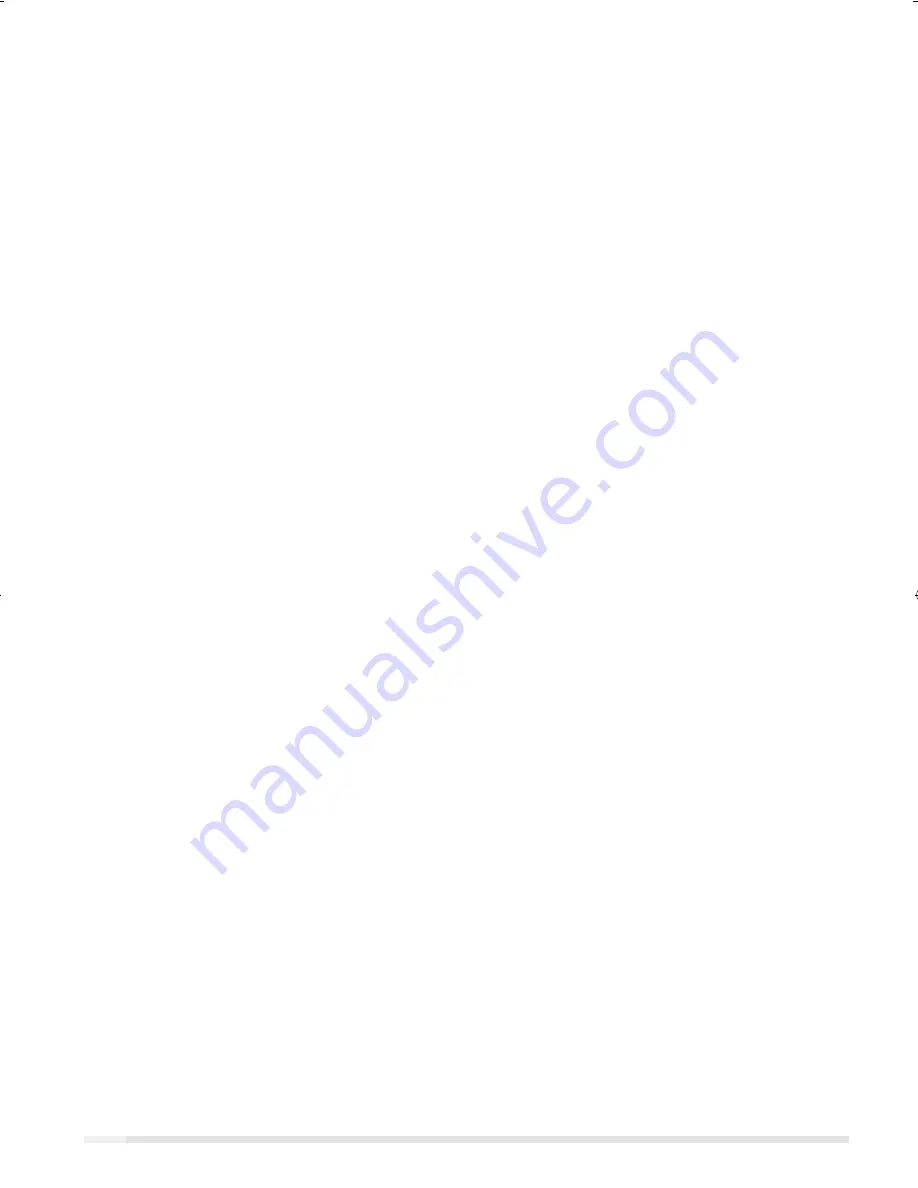
3
GEA19684 ISRB_2008 rev._11.15
Safety Precautions
It is important that all personnel observe safety precautions
to minimize the chances of injury. Among many consider-
ations, the following should be particularly noted:
•
Blower casing and associated piping or accessories
may become hot enough to cause major skin burns on
contact.
•
Internal and external rotating parts of the blower and
driving equipment can produce serious physical injuries.
Do not reach into any opening in the blower while it is
operating, or while subject to accidental starting. Pro-
tect external moving parts with adequate guards.
•
Disconnect power before doing any work, and avoid
bypassing or rendering inoperative any safety or protec-
tive devices.
•
If blower is operated with piping disconnected, place a
strong coarse screen over the inlet and avoid standing
in the discharge air stream.
CAUTION: Never cover the blower inlet with your hand
or other part of body.
•
Stay clear of inlet and discharge openings.
•
Stay clear of the blast from pressure relief valves and
the suction area of vacuum relief valves.
•
Use proper care and good procedures in handling, lift-
ing, installing, operating and maintaining the equipment.
•
Casing pressure must not exceed 25 PSI (1725 mbar)
gauge. Do not pressurize vented cavities from an exter-
nal source, nor restrict the vents without first consulting
Roots.
•
Do not use air blowers on explosive or hazardous
gases.
•
Other potential hazards to safety may also be associat-
ed with operation of this equipment. All personnel work-
ing in or passing through the area should be trained to
exercise adequate general safety precautions.
Operating Limitations
A Roots blower or exhauster must be operated within
certain approved limiting conditions to enable continued
satisfactory performance. Warranty is contingent on such
operation.
Maximum limits for pressure, temperature and speed are
specified in TABLE 1, page 13 for various models & sizes
of blowers & exhausters. These limits apply to all units
of normal construction, when operated under standard
atmospheric conditions. Be sure to arrange connections or
taps for instruments such as thermometers and pressure or
vacuum gauges at or near the inlet and discharge connec-
tions of the unit. These, along with a tachometer, will enable
periodic checks of operating conditions.
PRESSURE
– The pressure rise, between inlet and dis-
charge, must not exceed the figure listed for the specific unit
frame size concerned. Also, in any system where the unit
inlet is at a positive pressure above atmosphere a maximum
case rating of 25 PSI gauge (1725 mbar) should not be
exceeded without first consulting Roots. Never should the
maximum allowable differential pressure be exceeded.
On vacuum service, with the discharge to atmospheric pres-
sure, the inlet suction or vacuum must not be greater than
values listed for the specific frame size.
TEMPERATURE
– Blower & exhauster frame sizes are ap-
proved only for installations where the following temperature
limitations can be maintained in service:
•
Measured temperature rise must not exceed listed val-
ues when the inlet is at ambient temperature. Ambient
is considered as the general temperature of the space
around the unit. This is not outdoor temperature unless
the unit is installed outdoors.
•
If inlet temperature is higher than ambient, the listed
allowable temperature rise values must be reduced by
2/3 of the difference between the actual measured inlet
temperature and the ambient temperature.
•
The average of the inlet and discharge temperature
must not exceed 250°F. (121°C).
•
The ambient temperature of the space the blower/
motor is installed in should not be higher than 120°F
(48.8°C).
SPEED
– These blowers & exhausters may be operated
at speeds up to the maximum listed for the various frame
sizes. They may be direct coupled to suitable constant
speed drivers if pressure/temperature conditions are also
within limits. At low speeds, excessive temperature rise may
be a limiting factor.
Special Note: The listed maximum allowable temperature
rise for any particular blower & exhauster may occur well
before its maximum pressure or vacuum rating is reached.
This may occur at high altitude, low vacuum or at very low
speed. The units’ operating limit is always determined by the
maximum rating reached first. It can be any one of the three:
Pressure, Temperature or Speed.
GEA19684_ISRB-2008_Tri-RAM_rev02.16.indd 3
15/02/2016 11:17:05
Summary of Contents for Roots Tri-RAM 409
Page 1: ...www howden com RootsTM Tri RAMTM Tri lobe Blowers Installation Operation Maintenance Manual ...
Page 15: ...15 GEA19684 ISRB_2008 rev _11 15 Assembly of Tri RAM Tri Lobe Blowers Models 409 413 416 ...
Page 16: ...GEA19684 ISRB_2008 rev _11 15 16 Assembly of Tri RAM Tri Lobe Blowers Models 617 621 ...
Page 18: ...GEA19684 ISRB_2008 rev _11 15 18 Assembly of Tri RAM Tri Lobe Blowers Models 722 and 728 ...
Page 20: ...GEA19684 ISRB_2008 rev _11 15 20 Assembly of Tri RAM Tri Lobe Blowers Models 826 832 ...