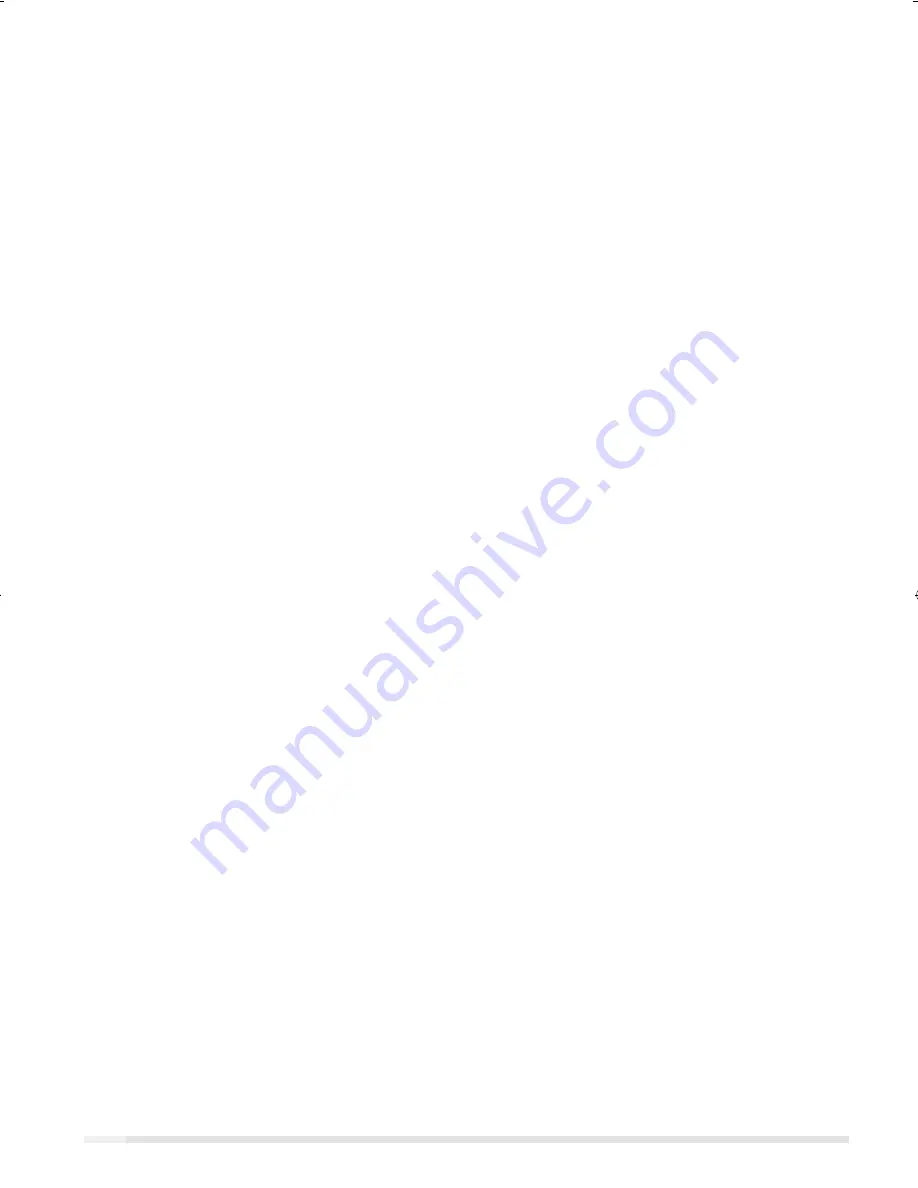
7
GEA19684 ISRB_2008 rev._11.15
Lubrication
Due to sludge build-up and seal leakage problems,
Roots recommendation is DO NOT USE Mobil SHC
synthetic oils in Roots blowers.
LUBRICATION: For Units with Splash Lubrication on
Both Ends.
•
The specified and recommended oil is Roots Synthetic
oil of correct viscosity per Table 2, page 13.
•
The proper oil level should be half way or middle of the
sight gauge when the blower is not operating. DO NOT
OVERFILL OIL SUMP/S as damage to the blower may
occur.
•
Oil level may rise or fall in the gauge during operation to
an extent depending somewhat on oil temperature and
blower speed.
•
It is recommended that the oil be changed after initial
100 hours of operation.
•
Proper service intervals of the oil thereafter are based
on the discharge air temperature of the blower. Please
refer to the information below to properly determine the
oil service intervals.
•
If you choose to use another oil other than the specified
and recommended Roots Synthetic, use a good grade
of industrial type non-detergent, rust inhibiting, anti-
foaming oil and of correct viscosity per Table 2, page
13.
•
Roots does NOT recommend the use of automotive
type lubricants, as they are not formulated with the
properties mentioned above.
Normal life expectancy of the specified and recommended
Roots Synthetic oil is approximately 6000 hours with an oil
temperature of 180°F (82°C) or less. As the oil temperature
increases by increments of 15°F (8°C), the oil life is reduced
by half for each 15°F (8°C) increase. Example: Oil tem-
peratures of 195°F (90.5°C) will produce a life expectancy
reduced by half or 3000 hours oil service life.
Normal life expectancy of petroleum based oils is about
2000 hours with an oil temperature of about 180°F (82°C).
As the oil temperature increases by increments of 15°F
(8°C), the life is reduced by half for each 15°F (8°C) increase.
Example: Oil temperatures of 195°F (90.5°C) will produce life
expectancy reduced by half or 1000 hours oil service life.
NOTE:
To estimate oil temperature, multiply the discharge
temperature of the blower by 0.88. Example: if the discharge
air temperature of the blower is 200° F, it is estimated that
the oil temperature is 176° F.
High ambient temperatures contribute to increased lubrication
sump temperatures. In situations such as blowers in a enclo-
sure, blowers exposed to radiant heat from other sources,
blowers installed in areas with poor air circulation or ambient
temperatures above 80°F the lubrication sump temperature
should be measured rather than fully rely on the calculation.
Bearings and oil seals are lubricated by the action of the
timing gears or oil slingers which dip into the main oil sumps
causing oil to splash directly on gears and into bearings
and seals. A drain port is provided below each bearing to
prevent an excessive amount of oil in the bearings. Seals
located inboard of the bearings in each headplate effectively
retain oilwithin the sumps. Any small leakage that may occur
should the seals wear passes into a cavity in each vented
headplate and is drained downward. Oil sumps on each end
of the blower are filled by removing top vent plugs, Item (21),
and filling until oil reaches the middle of the oil level sight
gauge, Item (37).
Initial filling of the sumps should be accomplished with the
blower not operating, in order to obtain the correct oil level.
Approximate oil quantities required for blowers of the various
models and configurations are listed in Table 3, page 13.
The oil level should not fall below the middle of the site
gauge when the blower is idle.
Proper lubrication is usually the most important single
consideration in obtaining maximum service life and satisfac-
tory operation from the unit. Unless operating conditions are
severe, a weekly check of oil level and necessary addition of
lubricant should be sufficient. During the first week of opera-
tion, check the oil levels in the oil sumps about once a day,
and watch for leaks. Replenish as necessary. Thereafter, an
occasional check should be sufficient.
More frequent oil service may be necessary if the blower is
operated in a very dusty location.
*Roots Synthetic oil is superior in performance to petroleum
based products. It has high oxidation stability, excellent cor-
rosion protection, extremely high film strength and low coef-
ficient of friction. Typical oil change intervals are increased
2-3 times over petroleum based lubricants. Also, Roots
Synthetic oil is 100% compatible with petroleum based oils.
Simply drain the oil in the blower and refill the reservoirs with
Roots Synthetic oil to maintain optimum performance of
your Roots blower.
GEA19684_ISRB-2008_Tri-RAM_rev02.16.indd 7
15/02/2016 11:17:05
Summary of Contents for Roots Tri-RAM 409
Page 1: ...www howden com RootsTM Tri RAMTM Tri lobe Blowers Installation Operation Maintenance Manual ...
Page 15: ...15 GEA19684 ISRB_2008 rev _11 15 Assembly of Tri RAM Tri Lobe Blowers Models 409 413 416 ...
Page 16: ...GEA19684 ISRB_2008 rev _11 15 16 Assembly of Tri RAM Tri Lobe Blowers Models 617 621 ...
Page 18: ...GEA19684 ISRB_2008 rev _11 15 18 Assembly of Tri RAM Tri Lobe Blowers Models 722 and 728 ...
Page 20: ...GEA19684 ISRB_2008 rev _11 15 20 Assembly of Tri RAM Tri Lobe Blowers Models 826 832 ...