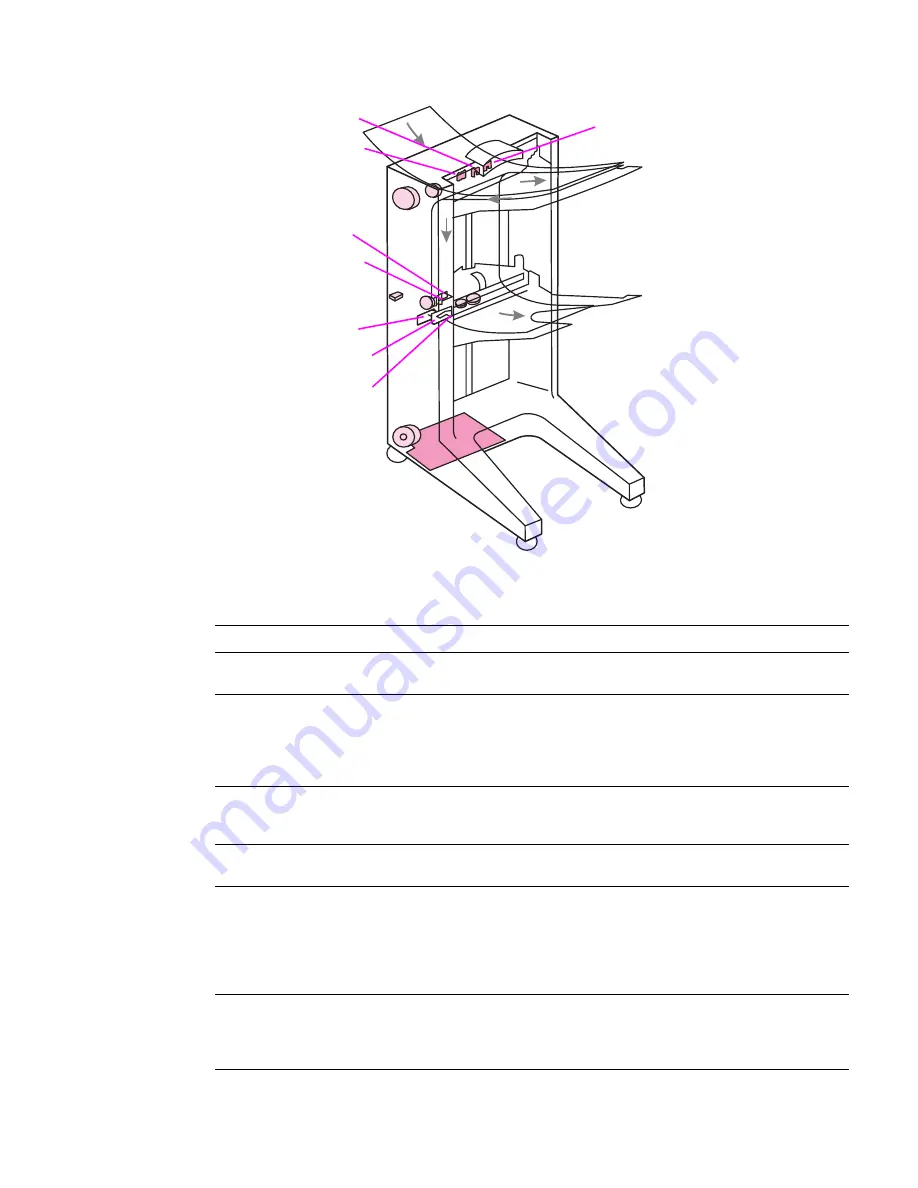
ENWW
Chapter 5 Theory of operation 85
8-bin mailbox
Figure 46.
Sensors—8-bin mailbox
FACE_UP
EXIT1
SLIDER
HEAD_POS
ENTRY
FACE_UP_FULL
PAPER_PRESENCE
EXIT2
Name
Description
Function
Location
FACE_UP_FULL
Left-output-bin-full sensor Detects a bin-full condition in the
face-up bin
Face-up bin
ENTRY
Paper-entry sensor
Detects media that is entering
the 8-bin mailbox and triggers
the start of the flipper motor to
transport media into the 8-bin
mailbox
Flipper
EXIT1
Paper-delivered-to-head
sensor
Detects media that arrives to the
elevator head and is exiting to a
face-down bin
Head assembly
SLIDER
Delivery-rollers-extended
sensor
Detects the position of the slider
rollers
Head assembly
HEAD_POS
Paper-bin-full sensor
“Reads” the slots on the back of
the bins to detect if the elevator
is moving and to perform
configuration during initialization,
and to detect if a bin is full when
the head is stopped in a bin
Head assembly
PAPER_PRESENCE Paper-bin-empty sensor
Is active if at least one sheet of
media is correctly placed in the
bin where the elevator head is
positioned
Head assembly
Summary of Contents for C8088B
Page 1: ...service ...
Page 2: ......
Page 10: ...8 Contents ENWW ...
Page 44: ...42 Installation ENWW ...
Page 153: ...ENWW Chapter 6 Removal and replacement 151 Figure 118 Stacker controller PCA 2 2 2 2 1 3 2 3 ...
Page 299: ......
Page 300: ... 2004 Copyright Hewlett Packard Development Company L P Q5693 Q5693 90002 90002 Q5693 90002 ...