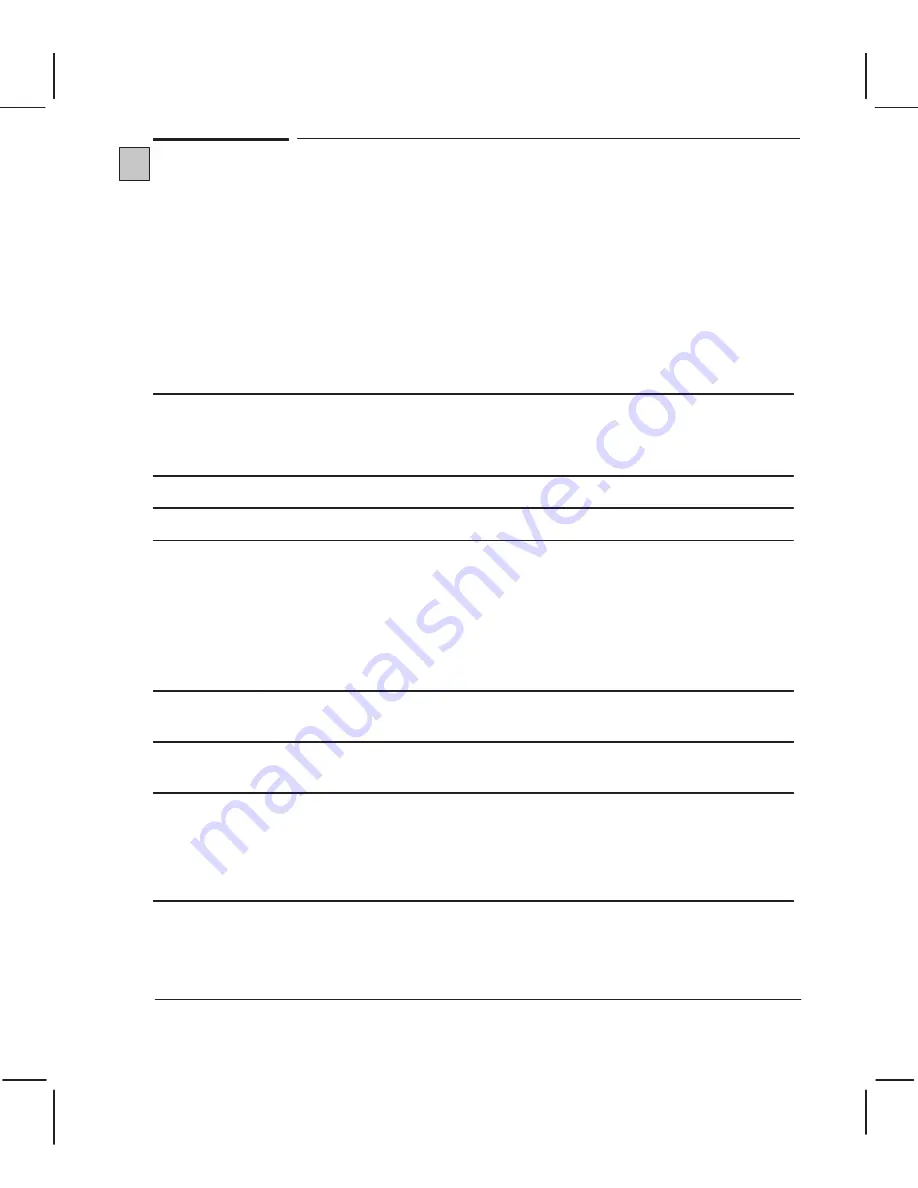
8Ć19
Troubleshooting
C4699Ć90000
System Errors for the DesignJet 230 and 250C Plotters
The DesignJet 230 and 250C plotters have many failure modes that cause system errors.
Many are due to electrical problems, others electronic, and some mechanical.
To more precisely troubleshoot the system error, you may be able to find out what line of the
firmware code the error appeared, and interpret this line;
If possible, print the service configuration plot (see
'
page 8Ć49). The last system error,
and the line number of the system error are printed on this plot.
See if the line number also appears in the following table. (Make sure that you also know
which firmware revision the plotter is using, since a given line number corresponds to
different lines in different revisions.)
Firmware
A.01.03
Firmware
A.01.04
Firmware
A.01.05
(and most frequent causes)
testmode.c
-
1735
1739
YĆaxis servo error during bench run.
testmode.c
-
1907
1973
X/YĆaxis servo error during bench run.
testmode.c
3014
3013
3079
Cartridge continuity:
D
Cartridges badly seated.
D
Faulty or badly connected trailing
cable.
D
Dirty carriage flex circuit.
D
Faulty carriage.
D
Faulty electronics module.
testmode.c
2950
or 2959
2949
or 2958
3015
or 3024
Secondary
Fibis
test failed:
D
Faulty electronics module.
testmode.c
2974
2973
3039
Error in swathĆRAM test:
D
Faulty electronics module.
testmode.c
2992
2991
3057
Error in cartridgeĆvoltage regulation:
D
Faulty or badly connected trailing
cable.
D
Faulty carriage.
D
Faulty electronics module.
Summary of Contents for Designjet 230
Page 1: ... ...
Page 3: ... ...
Page 13: ... ...
Page 18: ... ...
Page 19: ... ...
Page 22: ... ...
Page 23: ... ...
Page 25: ... ...
Page 28: ... ...
Page 29: ...3Ć7 Installation and Configuration C4699Ć90000 E A0Ćsize plotters only 32Kg 71 lb ...
Page 31: ... 2 1 ...
Page 32: ... ...
Page 33: ... ...
Page 39: ... ...
Page 43: ... ...
Page 59: ... ...
Page 63: ... ...
Page 64: ... Ensure that the cartridge caps are clean the wipers straight and the openings clear ...
Page 66: ... 2 1 ...
Page 69: ... ...
Page 73: ... Clip ...
Page 76: ... 5 5 mm Torx 15 ...
Page 78: ... Torx 15 Leave loose 5 5 mm Tighten slightly Torx 15 Tighten slightly ...
Page 81: ... Torx 20 ...
Page 93: ... Trailing cable under tabs ...
Page 96: ... ...
Page 103: ... the left and right sideĆplates or the lift mechanism will not work ...
Page 109: ... ...
Page 121: ... GO NO GO ...
Page 135: ... ...
Page 137: ... Flashing Can be On or Off Off On ...
Page 168: ... ...
Page 196: ... ...
Page 197: ... ...
Page 202: ... ...
Page 203: ... ...
Page 207: ... ...
Page 209: ...10Ć7 Parts and Diagrams C4699Ć90000 Top and Back Covers Electronics Trailing Cable ...
Page 211: ... ...
Page 213: ... ...
Page 215: ...10Ć13 Parts and Diagrams C4699Ć90000 CarriageĆAxis Right End ...
Page 217: ... ...
Page 219: ... ...
Page 221: ... ...
Page 223: ... ...
Page 225: ... ...
Page 227: ... ...
Page 233: ... ...
Page 242: ......
Page 243: ... ...
Page 249: ... ...