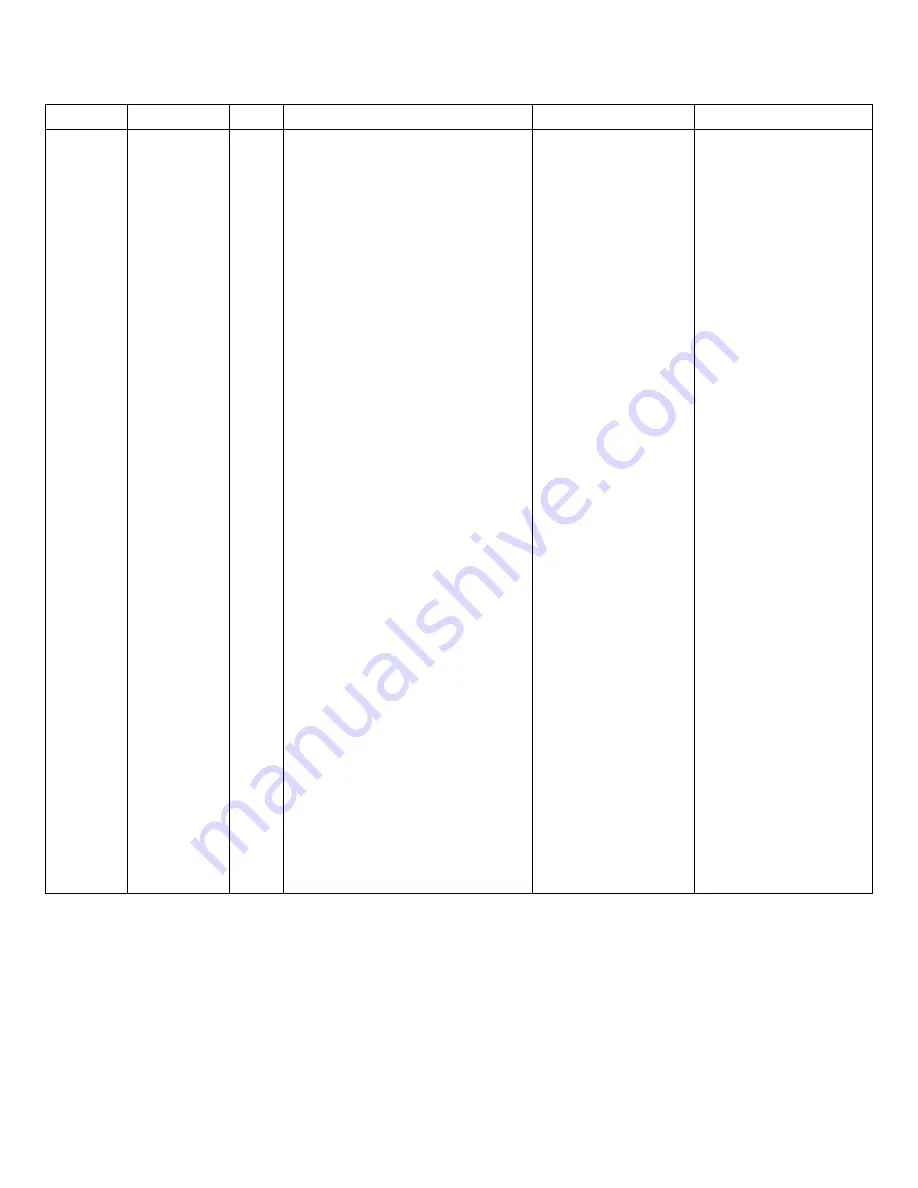
TABLE 6-1. PARTS LIST (Continued)
Reference
Mfr
Designation
HP Part Number
Qty
Description
Code
Mfr Part Number
R222
0684-1041
R:FXD COMP 100K OHM 10% 1/4W
01121
CB 1041
R223
2100-2682
R:VAR WW 10K OHM 10% LIN 2W
28480
2100-2682
R224
07035-80730
1
SLIDEWIRE ASSY:5K OHM
28480
07035-80730
R224
5060-4570
1
WIPER X-AXIS
28480
5060-4570
R225
0757-0427
1
R:FXD MET FLM 1.5K OHM 1% 1/8W
28480
0757-0427
R226
2100-2289
R:VAR 1K ± 20% 2W
28480
2100-2289
R227
0683-1055
R:FXD COMP 1 MEGOHM 5% 1/4W
01121
CB 1055
R228
0683-4731
R:FXD COMP 47K OHM 10% 1/4W
01121
CB 4731
R229
0683-2025
R:FXD COMP 2000 OHM 5% 1/4W
01121
CB 2025
R230
0683-2025
R:FXD COMP 2000 OHM 5% 1/4W
01121
CB 2025
R231
0684-2731
R:FXD COMP 27K OHM 10% 1/4W
01121
CB 2731
R232
0684-4731
R:FXD COMP 47K OHM 10% 1/4W
01121
CB 4731
R233
0683-1055
R:FXD COMP 1 MEGOHM 5% 1/4W
01121
CB 1055
R234
0684-1541
R:FXD COMP 150K OHM 10% 1/4W
01121
CB 1541
R235
0684-1541
R:FXD COMP 150K OHM 10% 1/4W
01121
CB 1541
R236
0699-0001
R:FXD COMP 2.7 OHM 10% 1/2W
01121
EB 27G1
R237
2100-1729
R:VAR WW 10 OHM 20% LIN 2W
28480
2100-1729
R238
0684-4741
R:FXD COMP 470K OHM 10% 1/4W
01121
CB 4741
R239
0684-1031
R:FXD COMP 10K OHM 10% 1/4W
01121
CB 1031
R240
0684-4741
R:FXD COMP 470K OHM 10% 1/4W
01121
CB 4741
R241
0684-1831
R:FXD COMP 18K OHM10% 1/8W
01121
CB 1831
R242
0684-3331
R:FXD COMP 33K OHM 10% 1/4W
01121
CB 3331
R243
0683-3945
R:FXD COMP 390K OHM 5% 1/4W
01121
CB 3945
R244
0684-4731
R:FXD COMP 47K OHM 10% 1/4W
01121
CB 4731
R245
0683-2225
R:FXD COMP 2.2K OHM 5% 1/4W
01121
CB 2225
R246
0684-6811
R:FXD COMP 680 OHM 10% 1/4W
01121
CB 6811
R247
0684-1841
R:FXD COMP 180K OHM 10% 1/4W
01121
CB 1841
R248
0684-1041
R:FXD COMP 100K OHM 10% 1/4W
01121
CB 1041
R249
0684-1021
R:FXD COMP 1000 OHM 10% 1/4W
01121
CB 1021
R250
0684-3331
R:FXD COMP 33K OHM 10% 1/4W
01121
CB 3331
R251
0684-1021
R:FXD COMP 1000 OHM10%1/4W
01121
CB 1021
R252
0684-4711
R:FXD COMP 470 OHM 10% 1/4W
01121
CB 4711
R253
0684-1521
R:FXD COMP 1500 OHM 10% 1/4W
01121
CB 1521
R254
0683-4725
R:FXD COMP 4700 OHM 5% 1/4W
01121
CB 4725
R255
0813-0046
R:FXD WW 1 OHM 10% 3W
28480
0813-0046
R256
0683-6215
R:FXD COMP 620 OHM 5% 1/4W
01121
CB 6215
R257
0761-0049
R:FXD MET OX 200 OHM 5% 1W
28480
0761-0049
R258
0683-6215
R:FXD COMP 620 OHM 5% 1/4W
01121
CB 6215
R259
0761-0049
R:FXD MET OX 200 OHM 5% 1W
28480
0761-0049
R301
0684-6831
4
R:FXD COMP 68K OHM 10% 1/4W
01121
CB 6831
R302
0684-6831
R:FXD COMP 68K OHM 10% 1/4W
01121
CB 6831
R303
0684-6831
R:FXD COMP 68K OHM 10% 1/4W
01121
CB 6831
R304
0684-6831
R:FXD COMP 68K OHM10% 1/4W
01121
CB 6831
R401
0811-1202
1
R:FXD WW 50 OHM 5% 3W
28480
0811-1202
R501
0683-6845
I
R:FXD 680K
±
5% 1/4W
28480
0683-6845
R502
0698-8754
2
R:FXD 10 MEG
±
1% 1/4W
28480
0698-8754
R503
0698-8754
2
R:FXD 10 MEG
±
1% 1/4W
28480
0698-8754
R601
NOT USED
R602
2100-1621
1
R:VAR 5K WW 4W
28480
2100-1621
S101
3130-0166
2
SECTION:ROTARY SWITCH
28480
3130-0166
S201
3130-0166
SECTION:ROTARY SWITCH
28480
3130-0166
S401
3101-1702
2
SWITCH:TOGGLE SPDT
18911
8926K124
S501
3101-1702
SWITCH:TOGGLE SPDT
18911
8926K124
S601
3101-2404
1
SWITCH:TOGGLE SPDT
82389
11A-1242
S602
3101-1174
1
SWITCH:TOGGLE SPDT
18911
7511K4
T601
5060-6857
TRANSFORMER ASSEMBLY
V101
1990-0072
4
PHOTOCONDUCTOR:2-LEAD, T0-5 PACKAGE
28480
1990-0072
V102
1990-0072
PHOTOCONDUCTOR:2-LEAD, T0-5 PACKAGE
28480
1990-0072
V201
1990-0072
PHOTOCONDUCTOR:2-LEAD, T0-5 PACKAGE
28480
1990-0072
V202
1990-0072
PHOTOCONDUCTOR:2-LEAD, T0-5 PACKAGE
28480
1990-0072
R504
0698-3453
2
R:FXD 196K ±1% 1/8W
28480
0698-3453
R505
0698-3453
2
R:FXD 196K ±1% 1/8W
28480
0698-3453
See introduction to this section for ordering information
6-5
Summary of Contents for HP-7035B
Page 1: ...TECHNICAL MANUAL HEWLETT PACKARD MODEL HP 7035B ...
Page 9: ...FIGURE 1 4 DIMENSION DRAWING FIGURE 1 5 ACCESSORIES 1 3 ...
Page 12: ...FIGURE 1 7 TYPICAL FREQUENCY RESPONSE INPUT FILTER FIGURE 1 8 TYPICAL DYNAMIC RESPONSE 1 6 ...
Page 14: ...FIGURE 2 1 WING BRACKET INSTALLATION FIGURE 2 2 STACKED CONFIGURATION 2 2 ...
Page 16: ...FIGURE 3 1 FRONT PANEL CONTROLS 7035B AND 7035B 001 MODELS 3 2 ...
Page 20: ...FIGURE 4 1 BLOCK DIAGRAM FIGURE 4 2 DETAILED BLOCK DIAGRAM 4 2 ...
Page 48: ...TM 11 6625 2850 14 P FIGURE 6 1 EXPLODED VIEW CABINET 6 9 ...
Page 49: ...TM 11 6625 2850 14 P FIGURE 6 2 EXPLODED VIEW CARRIAGE ARM SHEET 1 OF 2 6 10 ...
Page 58: ...FIGURE 7 1 COMPONENT IDENTIFICATION FRAME 7 8 ...
Page 59: ...TM 11 6625 2850 14 P Figure 7 2 Component Identification Circuit Board 7 9 ...
Page 60: ...TM 11 6625 2850 14 P Figure 7 3 Schematic Model 7035B D 07035 92550 7 10 ...
Page 62: ...TM 11 6625 2850 14 P FIGURE 8 1 COMPONENT IDENTIFICATION CIRCUIT BOARD 8 2 ...
Page 66: ...TM 11 6625 2850 14 P FIGURE 8 5 EXPLODED VIEW CARRIAGE ARM 8 6 ...