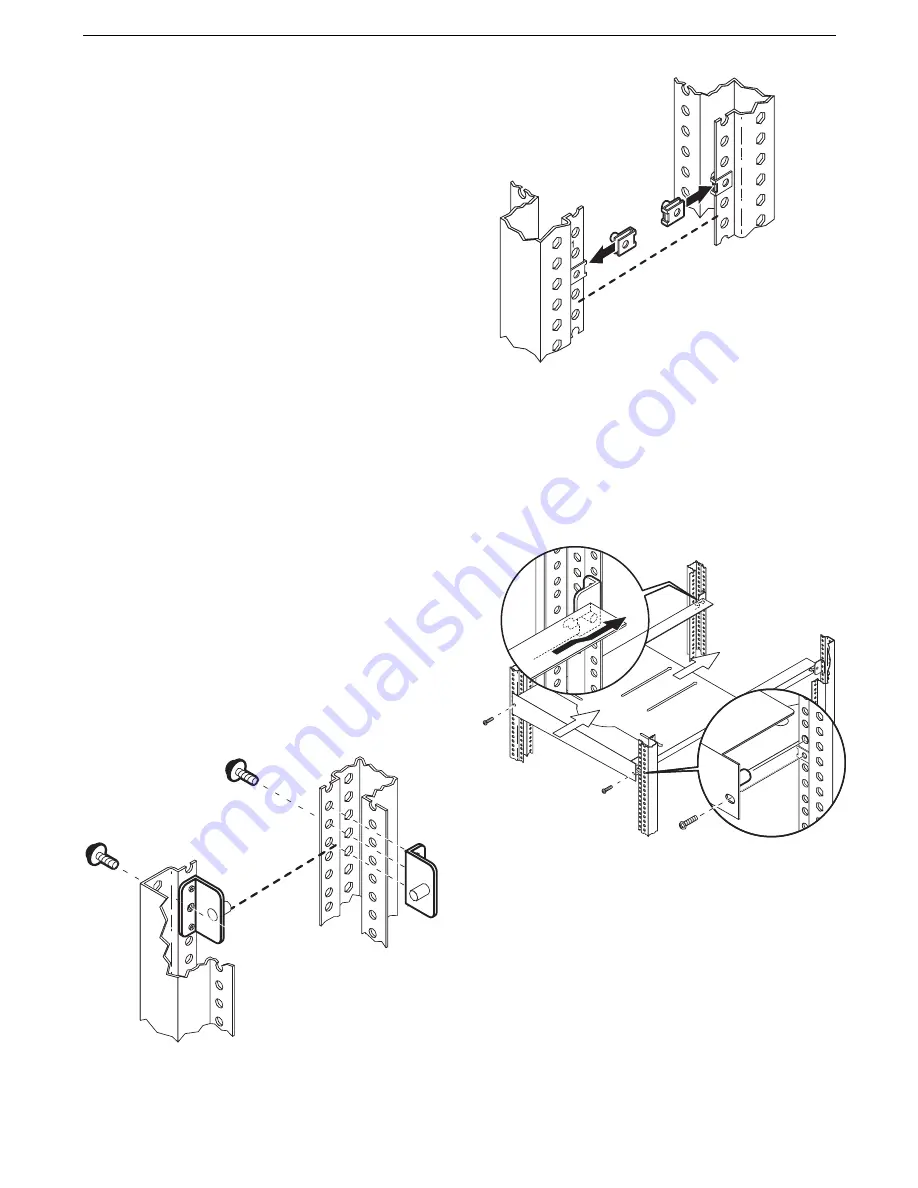
STEP 4
Install Keyboard Tray.
Standing in front of the rack and holding the front of
the Keyboard Tray, move it to the rear. The pins
pointing in on the Rear Brackets fit into the channels
cut into the back of the Keyboard Tray. Align the front
of the kit at the EIA location.
STEP 5
Install Decorative Screws in front column.
Front holes in the Keyboard Tray should align with
Sheet Metal Nuts attached in Step 3.
Installing Keyboard Shelf
This kit requires 2 EIA units in your HP rack.
Contents
2
Rear Brackets
2
Sheet Metal Nuts
1
Keyboard Kit Assembly
2
Decorative Screws
2
Torx 25 Screws with Lock Washers
2
Spare Mouse Cable Clips
Tools Needed:
Torx 25 Driver
NOTE: Extend the rack’s four leveling feet
before installing components in the rack.
STEP 1
Choose EIA location for the keyboard.
Determine whether the operator will sit or stand while
using the keyboard, and locate the EIA unit that places
the bottom of the Keyboard Tray at the correct height.
STEP 2
Position and attach Rear Brackets.
Position the bottoms of the Rear Brackets at the
desired EIA location. Install with two non decorative
Torx 25 bolts.
STEP 3
Install Sheet Metal Nuts in front columns.
On the middle hole of the EIA unit located in Step 1,
place sheet metal nuts on the front columns as shown.
(The shown EIA location is an example location.)
24
Chapter 4
Procedures
29
28
27
26
30
31
32
29
30
31
3
30
31
EIA location of
Monitor Base bottom
EIA location of
MonitorBase bottom
0
31
30