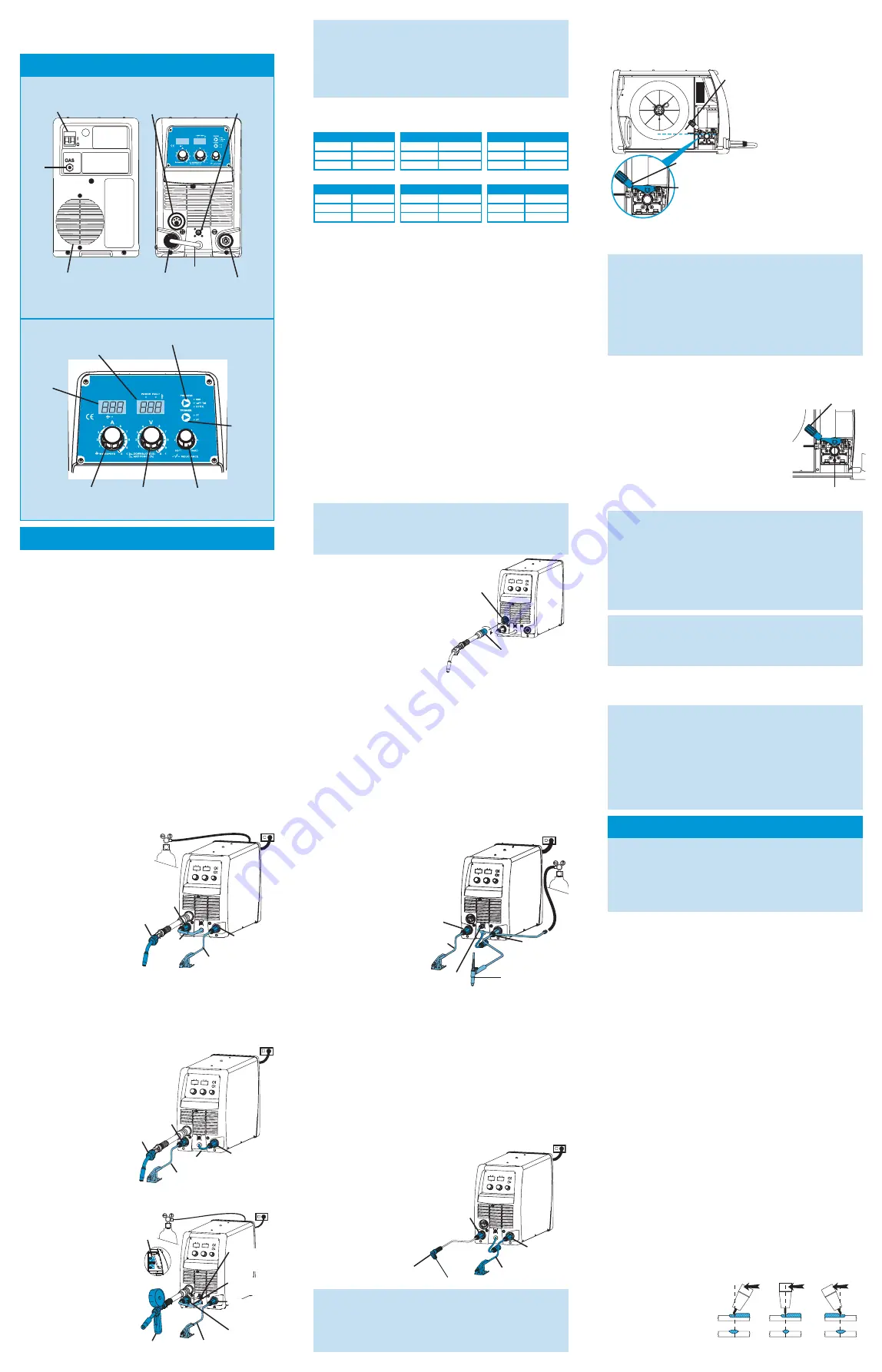
IDENTIFIER
The ON/OFF switch
(front panel)
is the main circuit
breaker. The Power Indicator display illuminates when
the power switch is in the ON position.
Amperage/
Wirespeed
switch
Voltage
switch
Process Selection
Control
Arc Control
(Inductance)
switch
Digital
Amps
Meter
Digital
Voltage
Meter
Trigger
Mode
Control
MIG
Gun
Adaptor
Positive
Welding
Output
Terminal
MIG
Polarity
Lead
Negative
Welding
Output
Terminal
Remote
Control
Socket
Gas
Inlet
Cooling
Fan
On / Off
Switch
GETTING STARTED
It is important that the equipment duty cycle is taken
into consideration when in use.
This welding power source is protected by a self resetting
thermostat. The indicator will illuminate if the duty cycle of
the power source has been exceeded. Should the thermal
overload indicator illuminate the output of the power
source will be disabled. Once the power source cools down
this light will go OFF and the over temperature condition
will automatically reset. Note that the mains power switch
should remain in the on position such that the fan
continues to operate thus allowing the unit to cool
sufficiently. Do not switch the unit off should a thermal
overload condition be present.
TRANSPORTING METHODS
This unit is equipped with a handle for carrying purposes.
Lift unit with handles built into the top of the front and rear
moulded panels.
Use handcart or similar device of adequate capacity.
If using a fork lift vehicle, place and secure unit on a proper
skid before transporting.
PREPARING FOR WORK
Place the unit on the
stable, levelled ground at a distance
of 300mm or more from the walls or similar that could
restrict natural air flow for cooling. Make sure the area
is free from moisture, dust, oil, steam and corrosive
gases. It is important to operate the machine in ambient
temperature between
0o C and 40o C.
ATTACHING MIG GUN
Fit the MIG gun to the
power source by pushing
the MIG gun connector into
the MIG gun adaptor and
screwing the plastic nut
clockwise to secure the MIG
gun to the MIG gun
adaptor.
WARNING
WELDING PRODUCTS AND WELDING PROCESSES CAN
CAUSE SERIOUS INJURY OR DEATH, OR DAMAGE TO
OTHER EQUIPMENT OR PROPERTY, IF THE OPERATOR
DOES NOT STRICTLY OBSERVE ALL SAFETY RULES
AND TAKE PRECAUTIONARY ACTIONS.
140A
20%
99A
60%
77A
100%
MIG DUTY CYCLE
125A
20%
80A
60%
60A
100%
STICK DUTY CYCLE
200A
20%
130A
60%
101A
100%
TIG DUTY CYCLE
DANGER!
ALWAYS MAKE SURE THE MAINS POWER SUPPLY IS
SWITCHED OFF BEFORE UNDERTAKING ANY TYPE OF
INTERVENTION ON THE WELDER
The HSS 200 amp Mig Welder is a self contained single
phase multi process welding inverter that is capable of
performing MIG (GMAW/FCAW), STICK (MMA) and LIFT TIG
(GTAW) welding processes. The unit is equipped with an
integrated wire feed unit, digital voltage and amperage
meters, and a host of other features in order to fully satisfy
the broad operating needs of the modern welding
professional.
Never use the 200 amp Mig Welder until you have fully
read and understood this User Guide and the machine has
been properly set up
using the information it contains.
MIG Gun
Adaptor
MIG Gun
Connector
INSERTING WIRE INTO THE WIRE FEED MECHANISM
Release the tension from the pressure roller by turning the
adjustable wire drive tension screw in an anti-clockwise
direction. Then to release the pressure roller arm push
the tension screw
toward the front of the
machine which
releases the pressure
roller arm. With the
MIG welding wire
feeding from the
bottom of the spool
pass the electrode wire
through the inlet guide, between
the rollers, through the outlet
guide and into the MIG gun. Re-
secure the pressure roller arm and
wire drive tension screw and adjust
the pressure accordingly. Remove
the contact tip from the MIG gun. With the MIG gun lead
reasonably straight, feed the wire through the MIG gun by
depressing the trigger switch. Fit the appropriate contact tip.
FEED ROLLER PRESSURE ADJUSTMENT
The pressure (top) roller applies pressure to the grooved
feed roller via an adjustable pressure
screw. These devices should be adjusted
to a minimum pressure that will provide
satisfactory WIREFEED without slippage. If
slipping occurs, and inspection of the wire
contact tip reveals no wear, distortion or
burn back jam, the conduit liner should be
checked for kinks and clogging by metal
flakes and swarf. If it is not the cause of
slipping, the feed roll pressure can be
increased by rotating the pressure screw
clockwise.
MIG Welding
Wire
DANGER!
BEFORE CONNECTING THE WORK CLAMP TO THE
WORK MAKE SURE THE MAINS POWER SUPPLY IS
SWITCHED OFF.
THE WELDING WIRE WILL BE AT WELDING VOLTAGE
POTENTIAL WHILE IT IS BEING FEED THROUGH THE
SYSTEM.
KEEP MIG GUN AWAY FROM EYES AND FACE.
Wire Drive
Tension Screw
Pressure Roller
Arm
Wire Drive
Tension
Screw
Pressure
Roller Arm
MIG (GMAW) WELDING WITH GAS SHIELDED MIG WIRE
The process selection control is used to select the desired
welding mode. Three modes are available, MIG
(GMAW/FCAW), LIFT TIG (GTAW) and STICK (MMA) modes.
Note that when the unit is powered off the mode selection
control will automatically default to MIG mode. This is
necessary so as to prevent inadvertent arcing should an
electrode holder be connected to the unit and mistakenly be
in contact with the work piece during power up.
MIG (GMAW) WELDING WITH GAS SHIELDED MIG WIRE
Select MIG mode with the
process selection control.
Next, connect the MIG
polarity lead to the positive
welding terminal (+).
Fit the MIG gun to the
power source.
Connect the work lead to
the negative welding
terminal (-).
Fit the welding grade
shielding gas regulator /
flow meter to the
shielding gas cylinder, then connect the shielding gas hose
from the rear of the power source to the regulator /
flowmeter outlet.
Refer to the Weld Guide located on the inside of the wirefeed
compartment door for further information.
MIG (FCAW) WELDING WITH GASLESS MIG WIRE
Select MIG mode with the
process selection control.
Connect the MIG polarity
lead to the negative
welding terminal (-).
Connect the work lead to
the positive welding
te).
Refer to the Weld Guide
located on the inside of the
wirefeed compartment
door for further
information.
SPOOL GUN MIG (GMAW) WELDING WITH GAS
SHIELDED MIG WIRE
Select MIG mode with the
process selection control.
Connect the MIG polarity
lead to the positive
welding te).
Fit the Euro Spool Gun to
the power source using
the front panel EURO
adaptor (see Attaching
MIG gun). Connect the 8
pin Remote Control Plug
to the 8 pin Remote
DANGER!
BEFORE CONNECTING THE WORK CLAMP TO THE
WORK MAKE SURE THE MAINS POWER SUPPLY IS
SWITCHED OFF.
SECURE THE WELDING GRADE SHIELDING GAS
CYLINDER IN AN UPRIGHT POSITION BY CHAINING IT
TO A SUITABLE STATIONARY SUPPORT TO PREVENT
FALLING OR TIPPING.
Positive
Welding
Terminal (+)
MIG Polarity
Lead
Negative
Welding
Terminal (-)
Work Lead
MIG Gun
CAUTION!
LOOSE WELDING TERMINAL CONNECTIONS CAN
CAUSE OVERHEATING AND RESULT IN THE MALE
PLUG BEING FUSED IN THE TERMINAL.
Positive
Welding
Terminal (+)
MIG
Polarity
Lead
Negative
Welding
Terminal (-)
Work Lead
MIG Gun
Control Socket on the power source.
Connect the work lead to the negative welding terminal(-).
Fit the welding grade shielding gas regulator / flowmeter to
the shielding gas cylinder, then connect the shielding gas
hose from the rear of the power source to the regulator /
flowmeter outlet.
Refer to the Weld Guide located on the inside of the wirefeed
compartment door for further information.
Select MIG mode with the process selection control.
Set the Spool Gun Switch located inside the wire drive
compartment, to SPOOL GUN.
TIG (GTAW) WELDING
Select LIFT TIG mode with
the process selection
control.
Connect the TIG Torch to
the negative welding
terminal (-).
Connect the work lead to
the positive welding
terminal (+).
Connect the TIG torch
trigger switch via the 8 pin
socket located on the front
of the power source as
shown below. The TIG torch will require a trigger switch to
operate in LIFT TIG Mode.
NOTE: If the TIG torch has a remote TIG torch current control
fitted then it will require to be connected to the 8 pin socket.
Fit the welding grade shielding gas regulator/flowmeter to
the shielding gas cylinder (see MIG Welding With Gas
Shielded Mig Wire) then connect the shielding gas hose from
the TIG torch to the regulator/flowmeter outlet. Note that the
TIG torch shielding gas hose is connected directly to the
regulator/flowmeter. The power source is not fitted with a
shielding gas solenoid to control the gas flow in LIFT TIG
mode therefore the TIG torch will require a gas valve.
STICK (MMA) WELDING
Connect the Electrode
Holder lead to the positive
welding te).
Connect the work lead to
the negative welding
terminal (-). Select STICK
mode with the process
selection control.
DANGER!
BEFORE INSERTING THE ELECTRODE IN THE TIG
TORCH MAKE SURE THE MAINS POWER SUPPLY IS
SWITCHED OFF.
BASIC TECHNIQUES
MIG WELDING
The easiest welding procedure for the beginner to
experiment with MIG welding is the flat position. The
equipment is capable of flat, vertical and overhead positions.
For practicing MIG welding, secure some pieces of 1.6mm or
1.2mm mild steel plate 150 x 150mm. Use 0.8mm flux cored
gasless wire or a solid wire with shielding gas.
Begin work by setting up power source. Power source has
two control settings that have to balance. These are the
Wirespeed control and the welding Voltage Control. The
welding current is determined by the Wirespeed control, the
current will increase with increased Wirespeed, resulting in a
shorter arc. Less wire speed will reduce the current and
lengthen the arc. Increasing the welding voltage hardly alters
the current level, but lengthens the arc. By decreasing the
voltage, a shorter arc is obtained with a little change in
current level.
When changing to a different electrode wire diameter,
different control settings are required. A thinner electrode
wire needs more Wirespeed to achieve the same current
level.
A satisfactory weld cannot be obtained if the Wirespeed and
Voltage settings are not adjusted to suit the electrode wire
diameter and the dimensions of the work piece.
If the Wirespeed is too high for the welding voltage,
“stubbing” will occur as the wire dips into the molten pool
and does not melt. Welding in these conditions normally
produces a poor weld due to lack of fusion. If, however, the
welding voltage is too high, large drops will form on the end
of the wire, causing spatter. The correct setting of voltage
and Wirespeed can be seen in the shape of the weld deposit
and heard by a smooth regular arc sound. Refer to the Weld
Guide located on the inside of the wirefeed compartment
door for setup information.
The angle of MIG gun to
the weld has an effect
on the width of the
weld. The welding gun
should be held at an
angle to the weld joint.
Hold the gun so that the welding seam is viewed at all times.
ADVICE
IF YOU HAVE NOT YET DONE ANY WELDING,
PRACTICE ON A PIECE OF SCRAP PLATE BEFORE
GOING ON TO MORE SERIOUS WORK. YOU MAY AT
FIRST EXPERIENCE DIFFICULTY.
ATTENTION
IF IN DOUBT, WHEN CONNECTING THE WORK LEAD
CONTACT HSS HIRE FOR ADVICE
WELDING CURRENT FLOWS FROM THE POWER
SOURCE VIA HEAVY DUTY BAYONET TYPE
TERMINALS. IT IS ESSENTIAL, HOWEVER, THAT THE
MALE PLUG IS INSERTED AND TURNED SECURELY TO
ACHIEVE A SOUND ELECTRICAL CONNECTION.
Positive
Welding
Terminal (+)
Negative
Welding
Terminal (-)
Work Lead
Electrode Holder
Positive
Welding
Terminal
(+)
Negative
Welding
Terminal (-)
TIG Remote
Control
TIG Torch
Work
Lead
MIG Polarity
Lead
Remote
Control
Socket
Negative
Welding
Terminal (-)
Positive
Welding
Terminal (+)
Work Lead
Spool Gun
Spool
Gun
Switch
Push
Vertical
Drag/Pull
210A
20%
130A
60%
101A
100%
MIG DUTY CYCLE
200A
20%
130A
60%
101A
100%
STICK DUTY CYCLE
200A
20%
130A
60%
101A
100%
TIG DUTY CYCLE
Duty Cycle for 110V Power
Duty Cycle for 230V Power