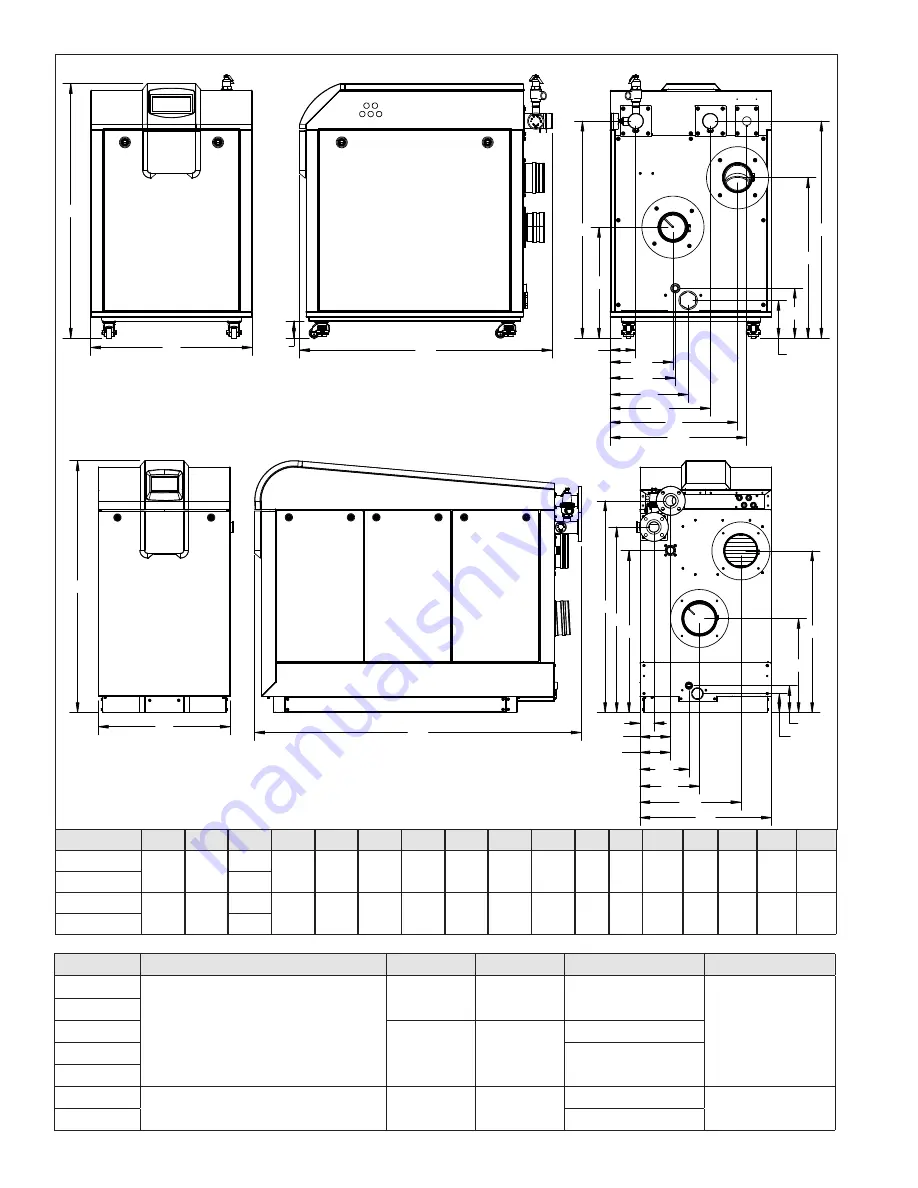
lp-666 Rev. 003 Rel. 001 Date 2.25.20
14
Figure 9 - ELX Specifications and Dimensions - NOTE: All Dimensions Are Approximate - *FOR REFERENCE ONLY
Model
Water Connection
Vent Size
Air Intake
Gas Connection
Condensate
400
2" NPT
4"
4"
1"
3/4" PVC
500
650
6"
6"
1"
800
1-1/4"
1000
1500
2 1/2” Flange
8”
8”
1-1/2”
1” PVC
2000
2”
Table 2 - ELX Adapter Dimensions and Specifications
R
C
M
L
E
Q
P
G
K
F
H
O
D
N
J
A
B
D
E
F
G
H
J
L
M
N
R
Q
P
O
K
LP-666-P
08/23/19
ELX1500 - 2000
ELX400 - 1000
C
A
B
MODEL #
A
B
C
D
E
F
G
H
J
K
L
M
N
O
P
Q
R
ELX400-500
41.0
26.0
40.7
17.9
35.0
4.1
10.1
10.5
12.6
16.1
20.5 22.0
6.1
8.1
25.8
35.0
2.8*
ELX650-1000
56.5
ELX1500
60.8
31.8
66.5
39.2
44.8
51.2
3.4
7.4
7.5
11.9
14.4 24.4
31.8
4.6
6.5
22.7
39.1
ELX2000
79.0