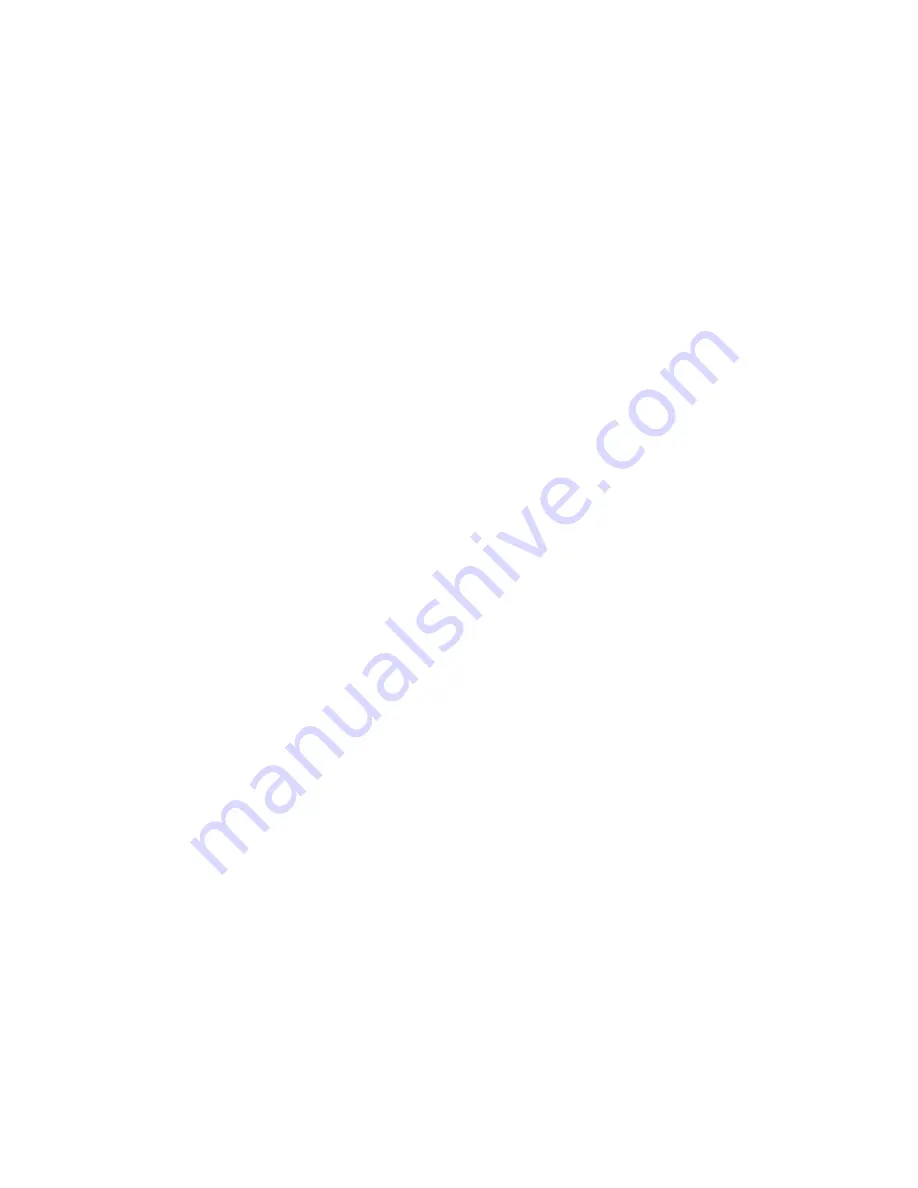
9
LP-171 Rev. 3.3.15
Modulating Combustion System
Modulation during operation is based on supply temperature and desired temperature set point. The set point used for the control
depends upon the programmed central heating curve. The heating curve slope can be changed by the installer to better fit system
needs. The control monitors the system to regulate burner output during operation to match system demand. This increase in efficiency
allows for substantial fuel savings.
Gas Valve
The gas valve senses suction from the blower, allowing gas to flow only if the gas valve is energized and combustion air is flowing.
Swirl Plate System
The gas valve swirl plate controls air and gas flow into the burner, assuring better mixing for improved combustion.
Supply Water Temperature Sensor
This sensor monitors heater output water temperature (system outlet/supply). The control module adjusts the heater firing rate so the
outlet/supply temperature is correct.
Return Water Temperature Sensor
This sensor monitors the return water temperature (system inlet/return). The control module reduces or increases heater input,
depending on how close the inlet/return water temperature is to the outlet water temperature.
Temperature and Pressure Gauge
Allows the user to monitor system temperature and pressure.
Control
The integrated control system monitors inlet/return and outlet/supply
water temperature and regulates fan speed to regulate the unit’s
BTU output. This allows the unit to deliver the required amount of heated energy and nothing more.
Flue Pipe Adapter
The flue pipe adapter may be positioned so that the installer is able to find a position that will best facilitate the exhaust and combustion
air pipe connections with the least number of elbows in even the most challenging of situations.
Burner
Constructed of metal fiber and high grade stainless steel, the burner uses pre-mixed air and gas and provides a wide range of firing
rates.
Electrical Field Connections with Terminal Strips
The electrical cover plate allows access to the line voltage and low voltage terminal strips. Attach line voltage conduits to the three
holes at the right of the line voltage terminal strip for power, CH pump and DHW pump. Route low voltage wires through the opening to
the left of the low voltage terminal strip (see Field Wiring Instructions, Part 9).
Condensate Drain Connection
As this is a condensing high efficiency appliance, the unit has a condensate removal system. Condensate is nothing more than water
vapor, derived from combustion products and similar to an automobile when it is initially started. It is very important that the condensate
line slopes away from the heater and down to a suitable inside drain.
If the condensate outlet on the heater is lower than the drain, you must use a condensate removal pump (kit p/n 554200 available from
HTP.) In addition, local authorities may require a condensate neutralizer to neutralize the condensate. Condensate neutralizers are
made up of lime crystals, marble or phosphate chips. Neutralizers can be installed in the field by the installer and purchased from HTP
(p/n N1100).
It is also very important not to expose the condensate line to freezing temperatures or any type of blockage. Plastic tubing must be the
only material used for the condensate line. Steel, brass, copper or other materials will be subject to corrosion or deterioration. A second
vent may be necessary to prevent condensate line vacuum lock on a long horizontal run. Also, an increase in pipe size may be
necessary to allow condensate to drain properly. Support of the condensation line may be necessary to avoid blockage of the
condensate flow.
Spark Ignition
The burner flame is ignited by applying a high voltage to the system spark electrode. This causes a spark from electrode to ground.
The Vision 1 Optional System
By controlling the temperature delivered to the central heating circuits based on outside temperature, the Vision 1 System allows the
installer to take this highly efficient heater and make it even more efficient. The Vision 1 System is also a two temperature system,
using one temperature for central heating and the other for use with an indirect water heater. This allows the user to increase the
temperature supplied to the indirect water heater to get a faster recovery by prioritizing the flow at a higher temperature than may be
needed for the central heating circuits (this requires two separate circulators). You must follow the piping, wiring, and programming
instructions located in the Vision One section of this manual.
Summary of Contents for MC120
Page 21: ...21 LP 171 Rev 3 3 15 M PIPING DETAILS Figure 5 ...
Page 53: ...53 LP 171 Rev 3 3 15 Figure 30 ...
Page 71: ...71 LP 171 Rev 3 3 15 Figure 34 ...
Page 72: ...72 LP 171 Rev 3 3 15 Figure 35 ...
Page 73: ...73 LP 171 Rev 3 3 15 Figure 36 ...
Page 76: ...76 LP 171 Rev 3 3 15 ...
Page 77: ...77 LP 171 Rev 3 3 15 ...