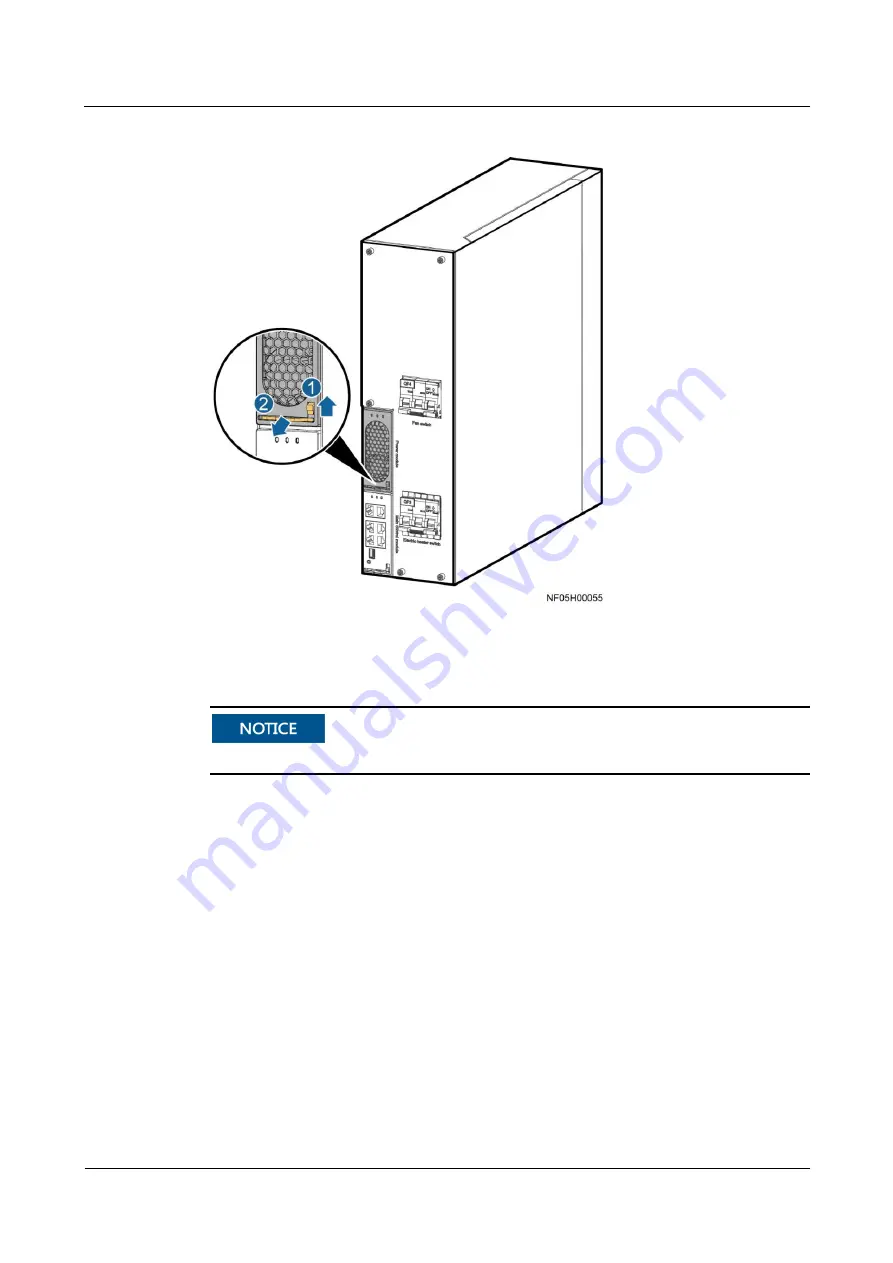
NetCol8000-C(070-260) In-room Chilled Water Smart
Cooling Product
User Manual
6 System Operation and Maintenance
Issue 06 (2020-01-13)
Copyright © Huawei Technologies Co., Ltd.
265
Figure 6-29
Removing a PSU
Step 3
Take out the handle and pull out the PSU from the subrack, as shown by (2) in
When installing a new PSU, ensure that the handle is in the lower part of the PSU.
Step 4
Insert the spare PSU into the corresponding slot of the power distribution subrack, and push
the latch downwards to lock the PSU.
----End
6.7.10 Replacing the Electric Heater
Context
Recommended tools and materials: protective gloves, a Phillips screwdriver, water-proof glue,
diagonal pliers, cable ties, and a new electric heater.