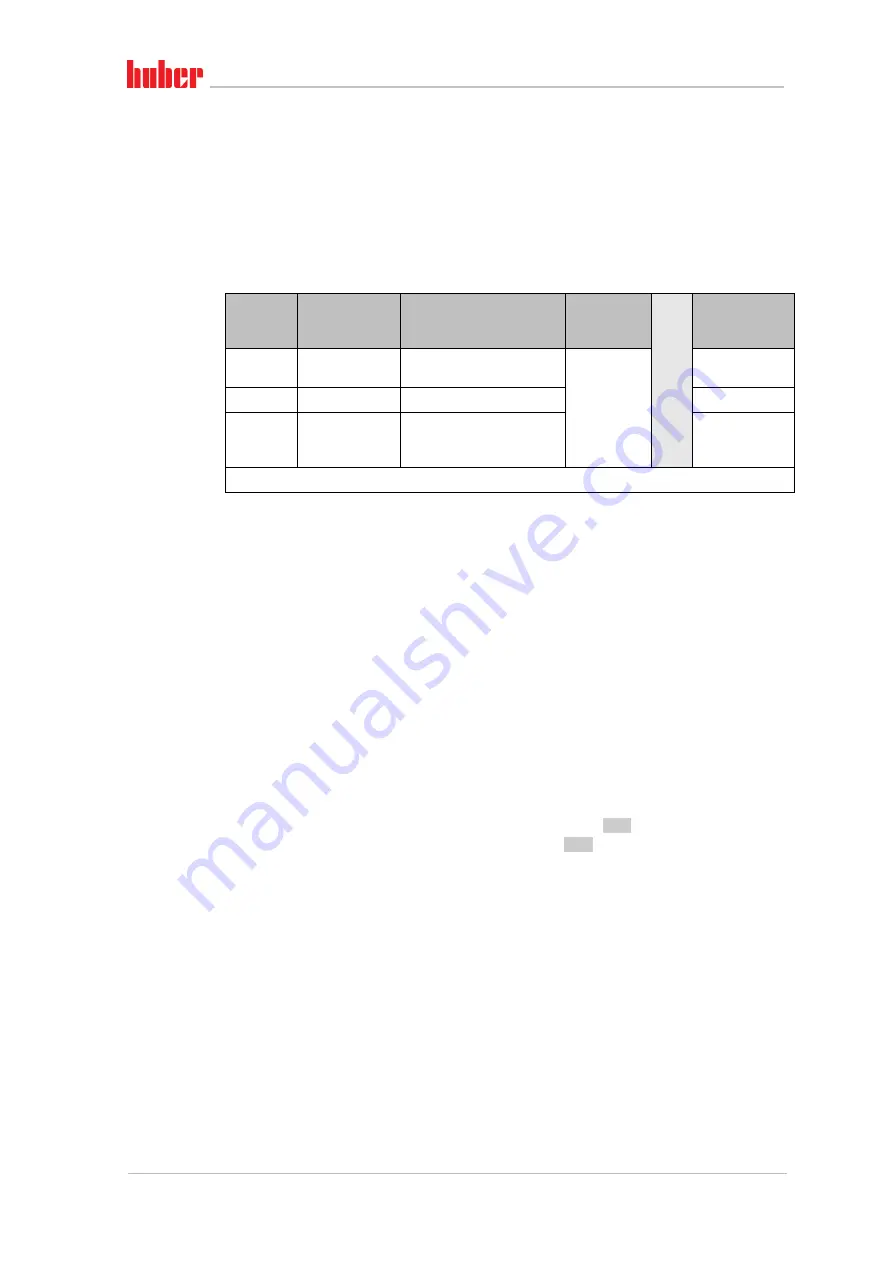
Introduction
OPERATION MANUAL
Chapter 1
Unichiller® eo Desktop
V2.2.0en/09.08.21//17.12
16
Huber temperature control units are constructed to be permanently sealed and are carefully
checked for leak tightness. Temperature control units with more than 150 g natural refrigerant are
equipped with an additional gas warning sensor. To find out whether your temperature control unit
is equipped with a gas warning sensor, refer to the data sheet.
→
For the filling capacity of the temperature control unit, refer to the data sheet.
→
From page 85,
section
. Or to the rating plate on the back of the temperature control unit. Please also
consider:
→
and
→
Class of
application
field
Application field
Example of the installation
location
Max.
quantity of
refrigerant
AND
Max. permissible
quantity above
ground level (GL)
A
General
Publicly accessible area in a
public building
8 g/m
3
ambient air
1.5 kg
B
Monitored
Laboratories
2.5 kg
C
Access only for
authorized
persons
Production equipment
10.0 kg
Temperature control units with
more than 1 kg
refrigerant
must not be installed below ground level
(GL).
Temperature control units with up to 150 g natural refrigerant
▪
The temperature control unit has been constructed to the requirements of EU and EFTA countries.
▪
Use the table as guidance for classifying the application field. Respect the max. refrigerant quanti-
ty stated therein.
Temperature control units WITH pre-installed gas warning sensor and > 150 g natural refrigerant
▪
The temperature control unit has been constructed to the requirements of EU and EFTA countries.
▪
Use the table as guidance for classifying the application field. Respect the max. refrigerant quanti-
ty or the permissible highest quantity above ground level (GL) stated therein.
▪
Ventilation with optional supply and exhaust air connection:
Use the temperature control unit’s
supply and exhaust air connection to connect it to the building’s exhaust system. For the exact
position please refer to the wiring diagram.
→
. First, remove the
cover to the air inlet connection; an air filter mat is installed behind it. This air filter mat must be
checked / replaced at regular intervals so that the air flowing into the temperature control unit is
not reduced.
→
»Function check and visual inspection«
. Connect the building’s
exhaust system with the temperature control unit’s exhaust air port. The cover of the supply air
port
must
not be removed
if the exhaust system provided in a building is not used
.
▪
The mounting plate for mounting a gas warning sensor is located inside the temperature con-
trol unit in the vicinity of the >Cable entry gas warning sensor<
[100].
▪
For the position of the
>Cable entry gas warning sensor<
[100] please refer to the wiring diagram.
→
▪
Additional information on the pre-installed gas detection sensor:
-
The built-in gas detection sensor enables a
safety shutdown at 20% of the lower explosive
limit via a power disconnect relay that is to be installed by the operator
. The tempera-
ture control unit is thus switched off early and safely in case of fault.
-
A
24 V DC external power supply
must be available for the pre-installed gas warning sen-
sor. The alarm output of the gas warning sensor uses a 4 - 20 mA signal. Please refer to the
data sheet of the gas warning sensor for further technical information. A
separate pro-
cessing unit is available as an accessory
for the control of the power disconnect relay. The
processing unit provides a potential-free switching contact and simultaneously provides
the power supply and analysis of the gas warning sensor. Both variants require the opera-
tor to provide the necessary dimensioning and installation. Please refer to the data sheet
of the gas warning sensor for the technical information necessary for the installation. The
alarm of the gas detection system can be connected to the operator’s alarm control unit.
The operator is responsible for this and for the other measures.
-
The operator is responsible for the
calibration of the gas detection sensor
prior to initial
operation and the observance of calibration and maintenance intervals according to the
Classifying the applica-
tion field